In an industry with large, capital hungry equipment, efficient management and maintenance of assets is critical to keeping costs down. Paper manufacturers need tools that standardize maintenance work flows, while streamlining business processes like procurement.
At Mohawk Fine Papers, a new Web-based enterprise asset management (EAM) system has replaced an older green-screen maintenance management system (MMS) to provide just such efficiencies for papermaking and converting equipment. In June 2008, the system was installed at the Cohoes and Waterford, N.Y., mills, and the Hamilton, Ohio, (Beckett) mill, as well as converting centers in Cohoes and Saybrook, Ohio.
![]() |
Paul Stamas, Mohawk’s vice president of
information technology. |
“Our first objective was simply to find an EAM system that could help us perform maintenance tasks more effectively,” says Paul Stamas, Mohawk’s vice president of information technology (IT), who is located at corporate headquarters in Cohoes. “Secondly, we wanted a tool that was flexible enough to easily integrate with our ERP (enterprise resource planning) system and to execute our vision for reducing the energy consumption of our assets.”
At its three mills, Mohawk produces more than 175,000 tons per year of fine papers on six paper machines. This tonnage includes Mohawk’s wind power grades, which have 100 percent of the electricity used in making them offset by renewable energy credits. The mills are served by the two converting centers, which offer state-of-the-art cut size, folio, roll converting and packaging to paper distributors, paper mills and OEMs.
Since implementing the new EAM system, Mohawk has standardized its maintenance processes across the company, streamlined work order flow, automated business rules, achieved more detailed tracking of assets and maximized use of electronic purchasing cards (p-cards). The new system has brought more benefits than were anticipated as the company moves into Phase II of its implementation, where even bigger gains are envisioned, such as reduced energy consumption.
“The business case we used to put this project together is still holding, and the EAM system is exceeding our expectations,” says Stamas.
Better accessibility, functionality needed
Since
1999, Mohawk has used the AS400-based BPCS (for business planning and control
system) from Infor as its ERP system. The installation is “very mature,” says
Stamas, and meets the company’s needs for financials and inventory, but its MMS
module was lacking in search capabilities and user friendliness. This became
especially apparent after Mohawk acquired International Paper’s (IP’s) Fine
Paper Division in 2005, adding the Beckett mill and Saybrook converting center
to its portfolio.
“The green-screen MMS was difficult to use on the factory floor, and it was unable to quickly locate available parts,” Stamas describes. “It just did not have the characteristics of a robust EAM system, which many of our former IP employees were accustomed to using.”
As for asset management functionality, the MMS “could not easily model the large moveable pieces of equipment associated with paper machines,” says Ben Whitaker, manager of enterprise process re-engineering in Cohoes, N.Y.
“A paper machine reel, for example, behaves somewhat like a piece of equipment, and the MMS was not capable of tracking an item as it moved into and out of positions, which is certainly a paper industry requirement,” Whitaker explains.
On a higher level, Mohawk wanted to streamline its procurement-to-pay process and lower its transaction costs for purchasing items. During team discussions geared at this goal, the need for an advanced EAM system became even more apparent. When Mohawk discovered that Infor was no longer planning to enhance the MMS after its purchase of DataStream, a best-of-breed EAM solution, the search was on for a new system.
The EAM system can track an item, such as
this paper machine reel at the Beckett mill, as it moves position.
(Shown:
John Boho, area manager, Beckett Mill)
A logical EAM choice
Mohawk began looking into
EAM systems in November 2007, with two in particular on its radar screen: Infor
(formerly DataStream) and IBM. The Infor EAM solution soon emerged as the
choice, not only because it was from Mohawk’s ERP system vendor, but also
because of technical considerations.
“The Infor EAM is a purely Web-architected solution, so we anticipated minimal issues with installing and using it because it can be deployed with a simple Web browser,” Stamas says. “Also, the Infor EAM is a very open product and its legacy has been to interface with a variety of systems, including our ERP.”
In addition, the EAM system would allow Mohawk to import documents or links to Web-based documents associated with its assets so maintenance personnel could reference them on the mill floor, an impossible feat for the MMS. Also, by running the EAM system in conjunction with Microsoft SQL Server 2005 database software, Mohawk could add work instructions to the system in the form of video files.
Infor’s basic EAM system is comprised of work order, purchasing and preventive maintenance modules. By addressing parts, equipment, work and purchasing, this configuration is “pretty traditional” for maintenance software, says Kim Osgood, manager of maintenance and engineering in Cohoes, but its business intelligence layer, with accessible interfaces, information dashboards and inherent flexibility, could help “catalyze the standardization of processes throughout our facilities.”
Mohawk has a history of deploying interconnected mill floor and enterprise systems so that it can analyze and react to process level trends in a way that adheres to business and financial goals (Pulp & Paper magazine, April 2008 issue, p. 30). The mills in Cohoes, Waterford and Hamilton use the OSI PI system to capture process information. By integrating the PI system with the new EAM using standard OPC interfaces, Mohawk will be able to consider energy as an input within the asset management process, a key consideration in meeting Mohawk’s diverse environmental objectives (Pulp &Paper, March 2007, p. 26).
“Our vision is to reduce the energy consumption of our equipment by 5 to 10 percent with the EAM,” says Stamas. “This is very important to our culture and to the environmental marketing message that differentiates us and our products.”
Like all of Mohawk’s fine papers, Beckett grades bear its wind power designation. All electricity used in manufacturing is offset with Green-e certified renewable energy certificates from wind power projects. Mohawk expects a further such reductions in its carbon footprint as it optimizes the EAM system.
Minimal installation issues
Mohawk kicked off Phase I of
its EAM project in February 2008, with the goal of going live by June at the
three mills and two converting centers. Spread across three geographically
separate locations, Mohawk used technology to unite its cross-functional teams
(see box below).
From an IT standpoint, the EAM system installation was “phenomenally easy,” according to Whitaker, who used service oriented architecture (SOA) techniques to integrate the new system with the ERP system. Most purchasing processes are now implemented via the EAM system. Results from these processes are sent to the ERP system’s general ledger and accounts payable modules (Figure 1).
“In many cases, integrating one system with another is a challenge, but here
there were only trivial issues,” Whitaker describes. “Within just a few days of
development, we were passing vendors from our ERP system to the EAM system,
which sent back the actual invoices. This ease of integration is something I
haven’t seen. It surprised me.”
Because of the seamless ERP/EAM integration,
Mohawk will further engage SOA in the future, particularly within the Infor
portfolio. The company will also push more of its IT vendors toward SOA
compliance in an effort to fully integrate its IT architecture, according to
Stamas.
As part of the project, Mohawk embraced the idea of server virtualization, which allowed the company to reduce the number of HP Proliant DL380 servers from 20 to just three, which run the Windows Server 2003 operating system. Whitaker says the computing environment was ironed out in one week using two people and assistance from Infor.
The EAM system’s flexibility was extremely helpful during implementation. Whitaker says that the system’s openness allowed for an easy configuration that meets Mohawk’s needs, without requiring customization that involved core system modifications.
Mohawk went live with the system in June 2008 as planned at the five locations. After the yearly maintenance shutdown in August, Mohawk kicked into gear on Phase II of the project, which is aimed at maximizing benefits from the EAM system beyond simply replacing MMS functionality related to maintenance and purchasing tasks.
Figure 1 - Flow of purchasing data between EAM and ERP systems
Tracking assets, standardizing processes
With the Infor
EAM system, Mohawk can now track all major equipment associated with its six
paper machines and converting machinery. It can also track assets in more
detail, looking at almost every item that has a motor, including pumps and
drives. With this level of detail, Mohawk can now monitor valuable assets like
motor and gearboxes throughout their lives as they are removed, repaired and
possibly designated for use in a different application or at another mill.
“Each paper machine is broken down into more than 100 positions within the EAM system,” explains Whitaker. “For large motors and machine rolls, we go down one more step to determine which particular motor or roll is on the machine, so it is quite complex.”
In addition to tracking assets more accurately, Mohawk has improved various processes relating to maintenance and purchasing. Some of these improvements were linked to the Beckett mill’s former association with International Paper.
“After the acquisition, Mohawk was not well standardized in its maintenance processes between facilities, so when the EAM system went live, it provided the incentive and support to do so,” says Scott Batts, IT project manager at the Hamilton, Ohio, mill. “It has allowed us to incorporate maintenance best practices from both Mohawk and IP.”
One example of how Mohawk has standardized maintenance processes is part naming conventions, which had been slightly different across storerooms within the company. This situation made it difficult for a storeroom manager at one site to identify a usable part in another storeroom. By standardizing nomenclature, Mohawk can keep parts inventory lower and potentially leverage purchases in the future by having common stores items.
In addition to SQL Server, the EAM system works with other Microsoft tools like Excel and Project Server. For example, Osgood can easily export shutdown workloads into Excel and Project, which are used as major outage planning tools.
On another front, the EAM system’s flexibility allowed Mohawk to automate business rules and work order status flows without customizing the software. In other software packages, work order flows are often predetermined and staff must work within those rules. With the Infor EAM system, Mohawk embedded its own rules and flows into the software so that it could provide better control of the work order process and automatic, immediate views of the work order’s progress. This flexibility to implement Mohawk’s business rules extended to invoice processing, purchase order processing and other areas – all without requiring customization of the software.
Mohawk discovered an unexpected application for the new EAM system in meeting its business goal to maximize use of p-cards. With the MMS, tracking visibility for order contents, purchase rationale, delivery dates and purchase history was lost when using p-cards as opposed to buying with traditional purchase orders (POs). On the flip side, POs provided a less efficient payment process. The EAM system, however, supports Mohawk’s business need to use p-cards by linking maintenance views with p-card views.
“We were able to work around the problem of data clutter, which is what we experienced with the MMS, and go from a limited policy around p-card purchasing to a new policy that allows us to buy everything on a p-card,” says Whitaker.
Mohawk also uses the EAM systems to
manage converting assets at its Waterford, N.Y., and Saybrook, Ohio (shown),
converting centers.
Initial benefits, future
plans
The implementation phase for the EAM project was “relatively quick and quite successful,” says Stamas, with Mohawk reaping immediate benefits during its yearly maintenance shutdowns in August. Osgood reports that the EAM system added visibility into tasks that allowed more effective organization of shutdown workloads. He also notes that the system has helped him more effectively manage capital projects at Mohawk through improved individual and aggregate project cost visibility.
Maximizing p-card use has helped Mohawk to reduce accounts payable processing while still having the benefits of purchasing tracking. “This was a big unexpected win for us on the EAM project,” Whitaker says.
On the mill floor, Mohawk currently uses the EAM system for generation of work requests that become work orders. As Mohawk embarks on Phase II, Stamas says the EAM project team will move into “the more visionary value-added goals we have for the system.” The EAM teams meet weekly to discuss opportunities for the system, and many of these goals relate to better workflows and more proactive, predictive work orders.
In the area of asset management, Mohawk continues to build history within the
EAM system that will help it better understand asset performance and improve
uptimes. As more and more data is collected and documents are linked to the
system, the system will place the data within easy reach for meaningful
decisions.
“As information migrates to EAM system, it will become more
useful to our craftsmen on a daily basis,” Batts describes. “This will include
zero energy or lockout/tagout information that help them safely and effectively
complete maintenance tasks. They will also be able to access bill of materials
for parts breakdowns, manuals and drawings. We are very close to deploying all
these capabilities.”
Reduction of energy consumption is a major business objective for Mohawk in which the EAM system will play a role. By integrating energy data from PI systems, power monitoring systems and other sources into one window, the EAM system will help isolate opportunities for energy and carbon emission reductions.
“We will be able to determine whether a particular machine’s motor should be replaced for energy or efficiency reasons,” Stamas explains. “The amount of energy cycles that we utilize could also be an input in terms of when we perform maintenance or not. We may choose to execute a maintenance task every X amount of kilowatt hours as opposed to every six months. This supports a more predictive, proactive approach to work orders rather than a reactive one.”
About the author:
Monica Shaw is a freelance
writer based in Atlanta.
With the help of open systems technology, Mohawk Fine Papers experienced few
technical issues when implementing its EAM system. Project management presented
another set of challenges, though, as Mohawk created project teams at three
geographically separate sites, ranging from the New York State capital district
(two mills, converting center) to sites near Cincinnati (mill) and Cleveland
(converting center). Once again, however, flexible technologies provided the
link for a successful go-live in June 2008 as scheduled. |
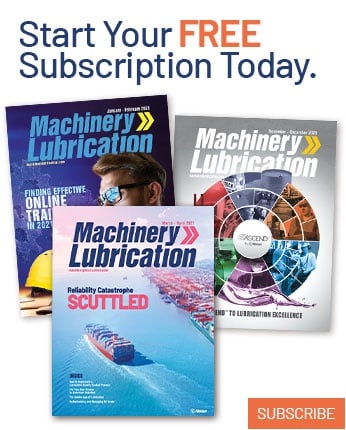