As automation devices have grown more complex and incorporated more plant data in their operation, there is an increased need for programming changes to continue smooth operation or improve performance. In environments requiring frequent changes, it is not uncommon for code to be lost or changes overwritten, resulting in increased downtime and decreased productivity.
Before MDT AutoSave was installed at the Nestlé Purina plant in Mechanicsburg, Pa., the plant used a home-grown program to track changes in its programmable devices. Approximately 15 programmers regularly made changes by accessing the most current program from Explorer, making changes and then saving the new version of the program back on Explorer.
The Challenge
Nestlé Purina sought to maintain plant performance and eliminate the risk of downtime and safety issues.
“Before we installed AutoSave (automation change management software), we really had no way to manage all of the different program versions created by our programmers,” says Alan Hiler, controls engineer, Nestlé Purina Mechanicsburg plant.
In facilities where multiple people are making changes from multiple computers, the documentation of changes is often lost, archives of older copies are non-existent and the wrong programs may be running on the devices.
“We made the decision to use AutoSave because we wanted to get away from having different people making changes and not documenting it properly,” says Mark Buettner, director of electrical and controls, Nestlé Purina Petcare. “We didn’t want a situation where an emergency occurs, such as a processor dies, and production is stopped because we don’t know where the latest version of the program is located or have to decipher which program is the current one.”
The Solution
The plant needed to gain plant-wide control of the automation environment. Here’s how the software solution came to the plant’s aid:
Rapid disaster recovery: There are many events that can have a negative effect on plant performance, including human error, equipment failure, sabotage, power surges/interruptions and fire. In providing a central repository of all program changes, AutoSave ensures that, if a device fails or a program results in undesired performance, a prior version of the program is readily available so plant operations can be restored quickly and correctly.
Reduce downtime, increase performance: “Before we had AutoSave, we had situations here where somebody made a change to a program and, since there really is no way to test the new program until it is in operation, the new program created a production problem,” describes Hiler. “With AutoSave, we can easily download the previous copy of the program and get things running again quickly. If one device is down, the entire plant could potentially be down, so the ability to get up and running again is very important.”
Decrease cost of operation and engineering: Stopping production because there are no older versions of a program available is costly enough, but consider the cost associated to completely rewrite a program.
“If you lose a copy of a program, it isn’t just the production time we are losing, but we also lose the intellectual value of the program we have created,” says Buettner.
The cost to rewrite, test and commission a single program is often greater than the cost to implement a change management solution.
Prevent errors and product waste: “Before AutoSave was installed in the plant, we had some problems with program version mismatches, the biggest issue being the assumption that the copy on file was the program running in the PLC, but in some instances, it was not,” says Hiler.
This situation has the potential of creating incorrect recipes resulting in discarded product. MDT AutoSave periodically queries automation devices and compares the code running in the processor with what is on file. If a mismatch is detected (indicating someone went around the software to make a change), an e-mail notification is sent highlighting the mismatch along with information pinpointing the changes. This ability to regularly verify that the correct version of the program is running significantly decreases product waste and safety risks.
Increase productivity and reduce safety hazards: The in-house program used by Nestlé Purina, before installing AutoSave, required multiple steps to make changes, all of which were manual.
“With AutoSave, the right program is listed right in front of you and all you have to do is click on it and you are in the program,” says Hiler.
To further complicate matters, the old program required user knowledge of all the communication parameters for connecting to a particular PLC or programmable device.
“For example, let’s say we would go through Windows Explorer and copy the batching system program to our computer. And then, when you get into the programming software, you have to type in the physical address of the processor to connect,” says Hiler.
He estimates this manual process would take approximately four minutes each time a change was made. Considering there are 15 programmers, if each programmer makes only one change in a day, an hour of productivity is lost just from having to perform manual routing. The time and money lost increases significantly if the current program is not readily accessible, the wrong program is downloaded, or the programmer connects to the wrong PLC.
“A big benefit for us is AutoSave’s ease of use for our maintenance guys. We have guys here that have never accessed a PLC program before, and they have to download a program to make a simple change. Before AutoSave, we had to write pretty detailed documentation on how to find the file, open it, connect to the server and so on. Not only does AutoSave save us time, it also significantly reduces any chance that the wrong PLC is accessed, causing big safety issues,” says Hiler.
Safeguard all automation assets: If the change management solution cannot support every programmable device in the organization, only selected systems are backed-up, leaving the facility still partially vulnerable to production and safety issues.
“We are a multi-platform organization; we use Modicon devices, Rockwell devices, Schneider devices and more,” says Buettner. “We needed a change management solution that would work with everything rather than using multiple types of change management software. That is what only MDT can bring to the table. MDT AutoSave is third party, it isn’t affiliated with a particular PLC manufacturer, it supports everything.”
As the only independent change management provider in the PLC/CNC/robot marketplace, AutoSave supports the most comprehensive range of devices and editors in the industry – from Schneider, Siemens, Mitsubishi, Indramat, Wonderware, GE, Rockwell Automation and others.
The Product
MDT Software is a world leader in factory automation device change management. For more than 20 years, MDT has delivered change management and version control solutions for automated manufacturing devices. In addition to Nestlé Purina, MDT’s food & beverage customers include: Campbell’s Soup, Coors Brewing, General Mills, Coca-Cola, Iams, Kraft Foods, Miller Brewing, Sara Lee and Tropicana. MDT also serves other leaders in the automotive, pharmaceutical, mining, petrochemical, airport and utilities industries. To learn more, visit www.MDTsoft.com.
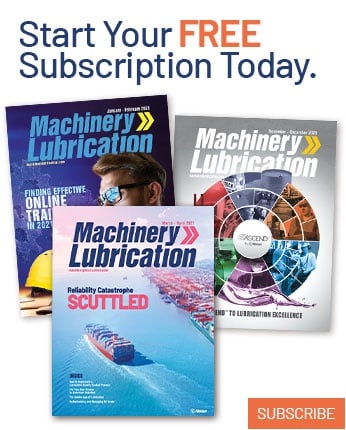