Lean manufacturing principles are successfully migrating from plant floors to aerospace and defense (A&D) maintenance, repair and overhaul (MRO) operations, but they typically fail to address significant sources of waste found in equipment maintenance activities. A&D MRO lean initiatives usually focus on eliminating wasted movement of people, parts and information by reconfiguring physical workspace layouts and related systems. These activities are essential in any lean implementation, but they are not sufficient to uncover and mitigate a fundamental source of waste that drives turnaround times higher: inefficient project schedules.
For years, typical A&D maintenance events for aircraft, helicopters, tanks, etc., have looked something like this:
- planners assign a package of routine inspections intended to identify “non-routine” repair requirements;
- the project manager focuses single-mindedly on completing the routine inspections, also known as shake, as soon as possible to achieve milestone timing;
- mechanics work around the clock in an attempt to complete required repairs;
- and ultimately, an unmanageable repair scope leads to delivery delays and the negative ramifications cascade from there.
This is frustrating for all parties involved, especially as requirements become more stringent for turnaround time duration and reliability, quality, cost and mechanic productivity. While the task may seem daunting, there is a disciplined approach available to combat the frustration and constraints.
Challenging the traditional approach to routine inspection shake is paramount to breaking the cycle of frustration. In particular, this requires a fundamental change of scheduling mind-set from completing routine inspections to identifying the non-routine maintenance requirements that so often throw projects behind schedule. Rather than attempting to complete shake within a set period of time, successful providers focus on discovery, which is the process of identifying non-routine maintenance requirements.
Figure 1 shows sample project results from two different perspectives. The shake graph on the left tracks only the completion of routine inspections, while the discovery graph on the right tracks only the identification of non-routine repair requirements. Given the long “tail” on the discovery graph, it quickly becomes clear that not all non-routine requirements are identified during shake, which ends at 20 percent of “Planned Project Days” on these graphs.
Figure 1 Relative Timing: “Shake” vs. “Discovery”
Few of those who are close to the MRO world would find it surprising that non-routine work requirements drive turnaround times. While many of these non-routine requirements are typically discovered during the completion of scheduled routine inspections, they may also present themselves as “hidden damage” found while conducting other repairs, hence the “tail” on the discovery graph in Figure 1. If project managers can increase the slope and shorten the “tail” of the “discovery curve” by identifying non-routine work requirements earlier, they will allow more time to plan the work, procure parts and turn wrenches.
Of course, doing so requires a change in priorities for project managers who are often judged on metrics that measure their ability to complete the pre-determined package of routine inspections. Luckily, a significant portion of the routine work has little to no critical path impact on overall project turnaround times, allowing the flexibility to reprioritize it to a later point in the maintenance event. Taking advantage of this fact to achieve effective discovery requires informed scheduling, focused project management and targeted tracking.
To properly schedule a maintenance event with a focus on discovery, planners must first understand the primary sources of non-routine work and hidden damage. Just as importantly, they must quantify the lead times on those repairs and identify the sources of the long lead-time work. The planners and project managers then must work together to fully document the key activities that are necessary to facilitate the discovery of non-routine work. These activities could simply include the routine inspection, but oftentimes there is a specific sequence of events that must occur before a non-routine requirement can be discovered. For example, conducting discovery on aircraft wings requires open-up, washing, flight control removal and routine inspection.
Additionally, if particular non-routine repairs are known to be sources of hidden damage, mechanics that are properly focused on discovery may begin working on those repairs even before lower priority routine inspections are complete in order to pull forward requirements identification. In order to do this, the planners and project managers must also understand which routine inspections pose limited to no risks to turnaround times and can, therefore, be pushed later in the schedule.
Once the sources of non-routine work and the sequencing of events are known, the planners can rewrite the project plan with a focus on completing the key activities and discovering non-routine requirements as soon as possible. A common best practice goal is to identify 90 percent of all non-routine requirements in the first 20 percent of the maintenance event. Figure 2 shows the project sequence change from the traditional approach (i.e., Before) to the discovery approach (i.e., After). By starting non-routine repairs even before the routine inspections are complete, project managers enhance their ability to complete projects on time.
Figure 2 Timeline: Traditional Approach vs. Discovery Approach
After finalizing the plan, also known as the discovery roadmap, successful execution depends upon project management. Given that project managers often follow some form of a schedule today, their job will not change significantly. However, they must actively manage the focus of their crew. Specifically, they must:
- Focus the entire maintenance team on following the discovery plan
- Instill a mind-set to quickly discover the “right” non-routine work first (e.g., long lead repairs)
- Ensure that work begins expeditiously on priority non-routine repairs to accelerate identification of hidden damage
By expediting the discovery of work requirements, project managers will have more time remaining in the project to sequence activities, allowing them to pull forward long lead time repairs which may have previously driven project turnaround times higher because they started too late in the event to be completed on time.
As one might assume, there is a significant learning curve component inherent in the discovery process, and the more times that a particular type of event is run, the more the mechanics, project managers and planners will learn. As a result, it is imperative that the planners track project results and review them on a regular basis. In addition to compiling pertinent project data, the planners must seek input from project managers, inspectors, mechanics, purchasing representatives,and anyone else who may have insight into the event. This will allow them to develop an understanding of the key drivers of turnaround time performance, whether it is the sheer number of non-routine repairs, the duration of those repairs, the amount of hidden damage that they yield or even the replacement part procurement cycle time. This knowledge facilitates the development of an even more effective discovery approach for the next maintenance event of that type.
Figure 3 Impact of the Discovery Approach
Lean MRO organizations that ultimately develop a library of discovery roadmaps addressing each of their event types realize turnaround times and variability even better than those that are achieved with the base improvements observed in traditional lean programs (Figure 3). This is because they not only remove the wasted part, people and information movement, but also the time associated with waiting too long to commence critical path repairs.
Even before the aircraft arrives and the mechanics pick up their tools, a better understanding of what is expected to happen during a maintenance event and how to respond will result in better reliability in turnaround times, which is beneficial to the customer for their own planning purposes. Eventually, the successful implementation of a discovery program eliminates the focus on shake and shifts the focus to discovery of non-routine work, the ultimate driver of turnaround time performance.
About the author:
Greg Maynard is the director of Archstone Consulting. With an uncanny ability to unlock potential and empower growth, Archstone has amassed a world-class resumé of successful engagements – providing consulting services to 24 of the top 100 companies and 58 of the top 500 and 65 of the top 1,000, according to the latest Fortune rankings. To learn more, visit www.archstoneconsulting.com or call 203-940-8200.
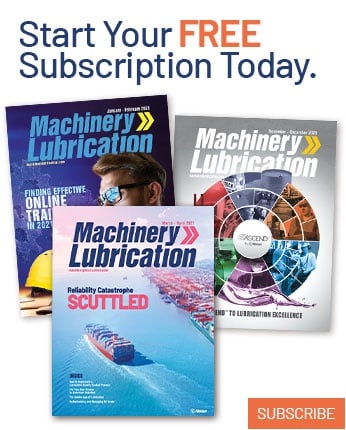