When Solvay Advanced Polymers began plastics compounding operations in its Augusta, Ga., facility 10 years ago, severe abrasion was causing unexpected conveyance line failures – multiple elbow and pipeline blowouts throughout its dilute-phase pneumatic conveyance system less than two weeks after the first compounding line began.
The plant extrudes, palletizes and packages polymers for advanced industrial applications. The most abrasive products are AMODEL polyphthalamide pellets, composed of up to 50 percent glass. These high-velocity pellets travel up to 5,000 fpm through straight piping sections and around elbows, which are particularly susceptible to blowouts.
Undetected blowouts cost the plant more than $200,000 annually in lost product, with each hour of undetected blowout costing $4,000. The plant spent an additional $60,000 a year on labor to repair blowouts occurring daily. Eventually, such blowouts began to create significant yield reductions, affecting process distributions and causing safety and housekeeping issues.
Alternative Methods Tested
Ken Bowles, compounding equipment asset coordinator at Solvay, began searching for a permanent solution. Numerous fixes were tested with unsatisfactory results. Standard Type 304/316 short-radius stainless steel pipes had a service life from seven to 21 days in low pressure (4 psi) conveying. The plant experimented with long-radius bend elbows, pocket-back deflection elbows, ceramic-lined elbows, glass and glass-lined elbows, and chrome coatings with tungsten-carbide flame spray. Solvay also considered altering the system to accommodate a dense-phase product pneumatic conveying system or spiral conveyors with vibratory feeders.
Each method produced unacceptable outcomes, including excessive pellet degradation and undetectable product contamination. Certain approaches required elbow removal and cleaning between product and color changes. These methods were unfeasible because of the large number of elbows installed throughout the system.
The Kennametal Conforma Clad Solution
The Solvay plant had used Kennametal Conforma Clad’s popular WPR-29 cladding to prevent severe wear on their extruder barrels for several years. As a trial, Bowles installed his first Kennametal Conforma Clad conveyance components – short-radius 45-degree and 90-degree elbows – on his dilute-phase four-, six-, and eight-inch conveyance lines.
The elbows performed well, and Bowles quickly realized he had found a permanent wear solution. He gradually began cladding additional conveyance system components. First, he installed clad pneumatic conveying lines, which experienced the most aggressive wear. Then, he began attacking less-aggressive wear issues. The original Kennametal Conforma Clad elbows lasted from two to three years, with some performing after nine years of service.
Following the success with elbows and turns, Bowles also specified clad pipe for 30-inch downstream sections. He installed clad diverter valves in 2001, then clad extruder transition chutes and pelletizer strand guides. Clad cyclones were installed in 2002. In 2003, he added clad pipe sections to the gravity systems and began rotating straight sections 90 degrees to increase wear life.
Today, he continues to install additional clad parts and keeps spare field repair components on hand. According to Bowles, “Kennametal Conforma Clad was the only walk-away-from solution.” He now specifies Kennametal Conforma Clad cladding on all new equipment.
Bowles is particularly pleased with the active role Kennametal Conforma Clad engineers take in his projects. “We’ve faced a few challenges over the past nine years,” says Bowles, “but Kennametal Conforma Clad took joint ownership of the projects and we worked together to solve them. They want to understand our wear problems and are accountable. This has made all of the difference.”
Bowles admits that at first, it was a challenge to convince top management to invest in the cladding. He collected data demonstrating labor, parts, and lost-product savings resulting from the significant reduction in blowouts. The company quickly realized that up-front cladding expenditures would eventually reduce expenses. Now, the plant recoups the cladding expense in four to five months through yield improvements and reductions in product loss.
Solvay’s Mike Clark and Stan Branham used to spend their time making daily weld repairs on elbow and piping blowouts throughout the plant. Today, they concentrate on proactive projects instead of reacting to unexpected blowouts. Branham says, “Every time an unprotected pipe blows, we replace it with one from Kennametal Conforma Clad. We paint all of the Kennametal Conforma Clad parts yellow. One day, we’d like to paint the whole line yellow.”
Kennametal Conforma Clad Technology
Kennametal Conforma Clad is a leading provider of severe-wear solutions for industrial applications involving extreme abrasion, corrosion, and erosion.
Kennametal Conforma Clad components are particularly effective in high-wear environments where equipment failures are persistent problems. Its proprietary infiltration-brazed tungsten carbide cladding is metallurgically bonded to component surfaces. Kennametal Conforma Clad’s cloth delivery system enables densely packed tungsten carbide to be uniformly applied to complex geometries, providing a protective layer that wears at a uniform and predictable rate. The result is a durable cladding that is extremely abrasion and corrosion resistant.
In addition, Kennametal also offers high-performance components utilizing hot isostatic pressing (HIP) technology from Kennametal HTM. HIP-lined barrels and screw element blanks are two such products offering outstanding wear characteristics for improved product life and process performance. More information on HIP technology and other advanced material solutions from Kennametal HTM may be found at www.kennametal.com.
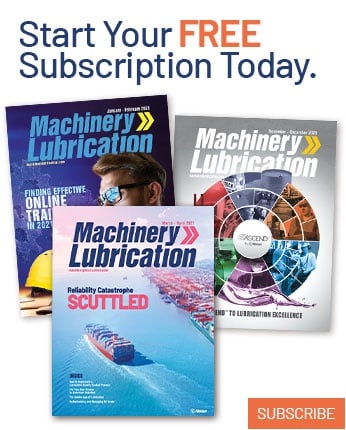