Officials at the U.S. Air Force’s Oklahoma City Air Logistics Center at Tinker Air Force Base are always looking for ways to improve the support they provide the warfighter by reducing costs and increasing productivity.
The 76th Propulsion Maintenance Group, with the assistance of the 76th Maintenance Support Group, recently launched a new initiative to the 76th Maintenance Wing called Total Productive Maintenance.
TPM, as it is known in private industry, is a maintenance strategy that adopts a life-cycle approach for improving the overall performance of production equipment by involving equipment operators in the maintenance process and evolving maintenance schemes from one that is reactive into a predictive, preventive and proactive program.
The goal of TPM is to achieve zero unplanned downtimes, zero defects, zero speed losses and zero accidents in all functional areas of an organization while ensuring healthy machine life cycles with minimal repair costs.
“No one knows more about our equipment than the people who use it every day,” said Jody LeBlanc, director of the 548th Propulsion Maintenance Squadron. “The best way for us to ensure our equipment successfully reaches the end of its natural life cycle is to give the operators more ownership of it and empower them to do the things they can that will ultimately make the difference.”
The 76th PMXG is currently deploying a pilot project to determine if TPM can achieve similar benefits across the depot and Air Force Materiel Command. TPM aims to transition from reactive maintenance to preventive and proactive maintenance through the continued involvement of the operator in the monitoring and maintenance of their machines. This includes their involvement in the visualization of their machines as well as their input toward the development of preventive maintenance actions documented on the standard AFMC Form 306.
“As we become more dependent on single pieces of equipment in the lean manufacturing Air Force we are currently transforming into, we are also becoming more dependent on the availability of that equipment,” said Paul Traweek, 76th MXW American Federation of Government Employees Council 214 representative.
“TPM will help our organizations transform from a reactive to a proactive workforce, resulting in increased production capabilities, and a safer and cleaner operating environment,” he said.
Jonathon Jones, a machinist with the 548th Propulsion Maintenance Squadron, reviews the newly developed Air Force Materiel Command Form 306 checklist on a vertical turret lathe prior to daily use. (Air Force photo)
Equipment operators, supervisors, maintenance and active-duty personnel participate in a three- or four-day training event during which they are introduced to TPM and then gain hands-on experience by cleaning, inspecting and developing standards for a piece of equipment.
The teams incorporate methods commonly used in process improvement, including lean, Six Sigma and “5-S plus 1”, to optimize the benefits of the events.
“TPM is a big step toward the goal of operator ownership, which lean and transformation are trying to achieve,” said David Robinson, an infrastructure engineer with the 76th MXSS.
As the team cleans and inspects the machine, they make notes of any discrepancies they find. During the event, the on-hand maintenance personnel fix the problems they can and place work orders for those things they cannot fix themselves. Throughout the process, the team also looks for ways to improve the machine’s reliability.
Toward the end of the training event, the team collaborates to create simple and visualized maintenance instructions for the machine that can easily be implemented and followed by the operator.
They also develop visual controls on the machine itself to guide inspection and maintenance actions, making TPM as easy as possible for the operators to include in their normal workday routines.
“By having the operators more closely monitor the equipment, problems can be caught before complete shutdown of the equipment occurs, allowing downtime for repairs to be planned around the production schedule,” said Walter Grimes, a repair technician with the 76th MXSG.
“This way the difficulty of repairs will become easier, and we won’t have to always be fixing the big failures,” he said.
Once the event is complete, the newly created inspection standard is placed in the hands of the operator for implementation.
“After going through the TPM training and being on the team for the first event that was for the machine I operate, I have a new sense of pride,” said Jonathan Jones, a machinist with the 548th PMXS Machine Flight. “Using pictures along with the inspection criteria developed by the team allowed me to quickly inspect and find any possible problems and get them fixed before they become major issues.”
A post-event session is scheduled for one month after the training event to follow-up with the operator to ensure the requirements are still acceptable.
“TPM places special trust in the operators who run our equipments’ preventive maintenance checklists before using the equipment each day,” said Charley Swanson, flight chief for the 548th PMXS Machining Flight. “We treat this as an opportunity to capture the experience of our highly skilled employees through their development of and compliance with each checklist. This is really a unique opportunity to leverage the expertise of our workforce to improve the reliability of the equipment we use and our productivity overall.”
Especially notable is that TPM is a cradle-to-grave philosophy; as the center brings in the latest technology of new generation machine tools that will increase productivity, employees will take ownership of that equipment and apply TPM.
“Some of our short-term returns have been unbelievable,” said Lt. David Schimke, a reliability manager with the 76th PMXG. “Ease of inspection combined with operator pride and ownership has dramatically increased what used to be low priority work order requests. We have also seen a tremendous boost in suggested safety improvements through our rapid improvement events.”
The 76th PMXG and the 76th MXSG know this pilot program, when combined with other reliability improvement methods, will lead to a significant improvement of overall equipment effectiveness that can then be spread throughout the 76th MXW.
This article was published in the Tinker Takeoff, the newspaper of the Oklahoma City Air Logistics Center. Writer Christy Jaworsky represents the OC-ALC Transformation Office.
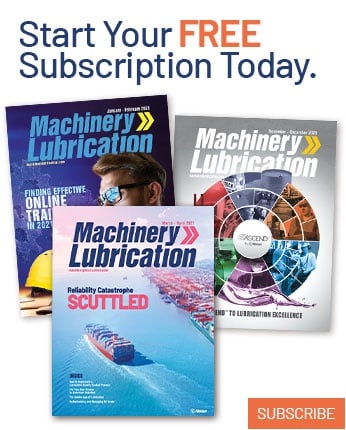