Honda's auto plants in Ohio and Alabama have received Energy Star awards from the U.S. Environmental Protection Agency (EPA) for advances in curbing energy use during the production of passenger cars and light trucks.
For the fiscal year that ended March 31, 2008, Honda's average CO2 emissions per vehicle produced in North America were at their lowest levels since the company began measuring results in 2001. The EPA bases the award points on the amount of energy needed to produce an automobile, and includes factors such as vehicle size and production volume.
In Ohio, Honda of America Manufacturing Inc.'s Marysville auto plant and East Liberty auto plant each earned top energy performance scores of 100 points. Both plants continue to find new ways to reduce the use of electricity and natural gas. Honda has focused most of these activities on more efficient use of lighting, chiller systems, motors, metering, heating, compressed air and air conditioning. The Marysville plant produces the Honda Accord sedan and coupe, and the Acura TL and RDX, while the East Liberty plant manufactures the Honda CR-V and Element.
"Improving the energy efficiency of Honda factories is the single biggest focus to reduce the impact of our manufacturing operations on climate change," said Gary Smith of Company Facilities at Honda of America Manufacturing, who worked with EPA on the project. "We have launched significant efforts throughout our operations to reduce the energy intensity of automobile production."
At the Marysville plant, associates significantly reduced electricity use by reprogramming plastic injection molding machines to run only during the production cycle. This has reduced carbon dioxide emissions by 80,000 pounds per year. At the East Liberty plant, Honda replaced older chiller pumps with smaller more efficient units that reduce carbon dioxide emissions by 508,000 pounds per year.
Honda Manufacturing of Alabama LLC, which produces the Odyssey minivan, Pilot sport utility vehicle and now the Ridgeline truck, also earned the Energy Star award. The Lincoln, Ala., plant implemented an initiative to monitor the use of equipment between shifts, during lunch and breaks, and on weekends. The monitoring program helped reduce electricity use on the paint line by 10 million kilowatt hours, representing about 15 million pounds of CO2.
In addition, these auto plants are implementing a unique "intelligent paint booth" technology that reduces energy consumption and related CO2 emissions from painting operations by as much as 25 percent. Automobile body painting consumes large amounts of energy because automakers need to condition the temperature and the relative humidity of the air to achieve the desired product appearance and finish quality. Developed by Honda in Ohio and Ohio State University, the system uses a predictive control mechanism to keep the temperature and humidity within specifications, even as weather conditions change.
"Our objective is to reduce the CO2 emissions throughout Honda's manufacturing operations," Smith said. "Initiatives like these are helping meet our commitments to reduce the environmental impact of product manufacturing."
In addition, Honda's strategy of building products close to its customers helps to reduce energy, emissions and waste associated with the transportation of products and component parts. Approximately 77 percent of the vehicles Honda sells in the U.S. are produced in North America.
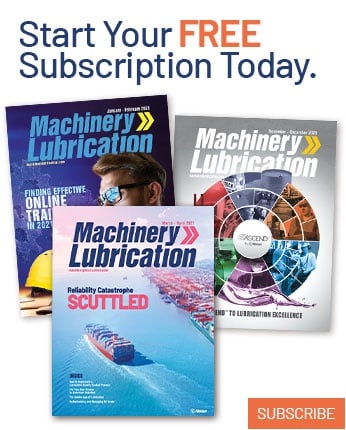