Properly designed insulation and refractories for industrial systems can mean big energy and cost savings for manufacturing companies. Dr. Arvind Thekdi, a U.S. Department of Energy (DOE) Energy Expert, regularly conducts Save Energy Now energy assessments and is proficient in helping companies realize energy savings through effective insulation practices. In this article, Dr. Thekdi answers questions about calculating heat loss, types of insulation materials and methods for maximizing system efficiency.
Question: What role does insulation and refractory design play in energy savings?
Answer: The terms “refractories” and “insulation” refer to a large family of inorganic, non-metallic materials used primarily to reduce heat loss or for thermal insulation. Insulation and refractories, individually or in combination, are used to contain heat in all applications where heat is generated, transferred, transmitted or recovered. Typical industrial applications include boilers, steam and hot fluid piping, furnaces, ovens, heaters, and storage tanks.
Insulating materials include those with low-thermal conductivity that divide an air space into very small pockets, thereby minimizing solid and gas conduction and radiation, and, for most applications, eliminating convection. Properly designed refractory and insulation systems reduce heat loss, conserve energy by reducing heat storage, maintain desired process temperatures, assist in heat transfer, and safely contain process atmosphere, such as flammable, toxic, or hazardous gases, vapors or liquids.
Q: How much energy can be saved through use of proper refractory and insulating materials?
A: All insulated surfaces lose some heat. The heat loss depends on a number of factors, such as the heating system or heat source temperature, selection and thickness of insulation used, and exposure of insulated surfaces to ambient conditions. Heating systems may lose 2 percent to 5 percent of the total heat input for the heating system through insulated surfaces. It is not feasible or always advisable to eliminate all insulation-related heat loss, but it is possible to reduce these losses by 10 percent to 25 percent. To achieve this, plant personnel must:
- review process requirements;
- know available and applicable insulation materials;
- select materials to meet the process requirements;
- properly design, install and precondition insulation systems during start-up;
- properly operate the equipment to avoid damage to the insulation; and,
- perform periodic maintenance, repairs and replacement of the insulation.
Q: How do I calculate heat loss?
A: For existing furnaces, ovens or heating systems, it is not necessary to perform detailed heat transfer analysis to calculate heat loss from a system; it is only necessary to measure the outside surface temperature. The heat loss calculations require measurement of surface temperature and information on conditions such as ambient temperature, wind velocity, orientation of the surface (vertical, horizontal facing upward or downward, etc.) and condition or emissivity (shiny vs. black or rusted) of the surface. Figure 1 shows values of heat loss per square foot of the heating system outside surface for a vertical surface with emissivity of 0.9 and wind velocity of zero miles per hour (indoor installation). This graph should be used as a general guide because wall heat loss depends on a number of factors.
Figure 1. Values of Heat Loss Per Square Foot of Heating Surface
Note that the heat loss calculated using Figure 1 or any other method should be corrected for the “available heat” for a heating system, particularly in a fired system that uses combustion of fuels such as natural gas. The available heat is the amount of heat that remains in the furnace after accounting or subtracting heat contained in flue (exhaust) gases leaving the heating system. The available heat for a fuel-fired heating system can be calculated by using graphs provided in Reference 1 (PDF 2.4 MB) or other industrial combustion books. The actual heat required and energy cost to compensate for the calculated wall heat losses could be considerably higher than the cost of energy calculated without correcting the heat loss calculated for the available heat.
Example: Calculating Savings by Reducing Wall Heat Loss of an Industrial Furnace From Figure 1, we can estimate the surface heat loss to be 275 Btu/square foot, or (275 x 500=) 137,500 Btu/hr. The furnace flue gases are discharged at 1,400°F with 5 percent oxygen in exhaust gases. The available heat for this system is approximately 55 percent as calculated by using graphs given in Reference 1 (PDF 2.4 MB) or other industrial combustion books. In this case, it is necessary to supply (137,500/0.55=) 250,000 Btu/hr to the combustion system. Reduction of surface temperature to 150°F by additional or alternate insulation would reduce heat loss by 35 percent, or approximately 90,000 Btu/hr. For annual operation of 8,000 hours/year and natural gas costs of $10 per MMBtu, the savings would be more than $7,200 per year. |
The heating system insulation design should consider the lowest possible and economically justified surface temperature using the economic considerations discussed above.
Q: What types of refractories and insulation materials are available?
A: Refractories are classified by chemical composition or physical properties. These include silica, alumina-silica, high alumina, basic and insulating. Most high-temperature refractories, such as firebricks, are high-density (greater than 120 pounds per cubic foot), and offer excellent resistance in challenging operating environments, such as containment of high-temperature slags with different chemical compositions, fumes, dust and gases. Insulating refractories have lower densities (50 to 70 pounds per cubic foot) and provide insulating properties while offering resistance to corrosion and chemical reactions in a less challenging operating environment.
The three basic types of insulating materials for industrial use are:
-
Thin (less than 20 micrometers), low-density (less than 12 pounds per cubic foot) fibers made from organic or inorganic materials.
-
Cellular material in closed or open cell form made of organic or inorganic material.
-
Flaked or granular inorganic materials bonded in the desired form.
In most cases, glass (silica), mineral wool, high alumina, mulite or zirconium are the base materials and can be used to temperatures as high as 2,900°F. See the table below for a list of insulating materials, along with values of range of densities in terms of pounds per cubic foot of dry material and range of thermal conductivities at 100°F. Exact values of the properties can be obtained from the suppliers. In general, lower-density materials offer lower thermal conductivity or higher resistance to heat flow and store less heat compared to higher-density insulating or refractory materials.
Material for Insulated Heating Systems |
Thermal conductivity at 100°F (Btu/hr-ft/°F) |
Density lb/ft3 |
Carbon steel (0-500°F) |
26.363 |
480.00 |
Rock (mineral) wool (0-1,200°F) |
0.021 |
9.25 |
Ceramic blanket-4 pcf density (300-2,000°F) |
0.009 |
4.00 |
Merchantable ceramic board (200-1,800°F) |
0.019 |
14 to 20 |
Ceramic fiber board (300-2,300°F) |
0.043 |
16 to 28 |
Ceramic fiber block (300-2,400°F) |
0.025 |
8 to 11 |
Low density castable (300-2,200°F) |
0.149 |
48 to 65 |
High density castable (300-2,600°F) |
0.429 |
95 to 140 |
Low temp. insulating firebrick (300-2,300°F) |
0.065 |
38 to 44 |
High temp. insulating firebrick (300-2,800°F) |
0.182 |
48 to 82 |
High density firebrick (300-3,000°F) |
2.288 |
180 to 190 |
With the exception of certain high-density materials, thermal conductivity of the insulation generally increases significantly as temperature increases. Figure 2 shows relative thermal conductivity values of commonly used refractories and insulating materials. Note that these values are relative to thermal conductivity of the material at 100°F. Actual values of the thermal conductivity should be obtained from the supplier. Consider temperature of the refractory and appropriate value of thermal conductivity to estimate accurate value of heat loss.
Figure 2. Thermal Conductivity of Refractories and Insulating Materials
Q: What should I keep in mind when selecting refractories and insulation?
A: Proper design and installation of refractories and insulation are important for a system’s performance and life and the overall economics of plant operation and profits. Consider the following four factors when selecting insulation materials and designing insulation systems:
-
Thermal performance: This includes temperature limit; melting or fusion temperature; thermal conductivity that represents insulation capability; heat capacity or storage; thermal expansion; and thermal shock (spalling) resistance.
-
Physical properties: These include density or porosity; abrasion; wear and erosion resistance; electrical resistivity for use in electric heating; mechanical strength; and other structural properties at high temperatures.
-
Chemical considerations: These include uniformity of composition; reactions between base materials and operating environment such as gases, liquids or solids in contact with the refractory or insulating materials; and volatilization of the constituents or binding agents, corrosion, chemical attack or diffusion and reactions with the product.
-
Economics: This includes initial cost of insulation; installation cost (labor and materials); maintenance and repair; and replacement costs.
Most applications require the use of more than one type of insulating material. All major suppliers offer guidelines and help in application and installation of insulation systems. In some cases, special tools and techniques are developed, and personnel must be trained for proper installation work.
Q: What tools and methods are available for design and selection of insulating systems?
A: When selecting proper insulation thickness, consider the technical factors mentioned above along with economic factors such as energy cost savings and insulation system costs. Cost of insulation is almost proportional to the thickness; however, the rate of energy savings (savings with additional increase in insulation thickness) decreases as the thickness increases. Hence, there is an optimum value of insulation thickness for any application that gives the minimum payback period.
Figure 3 shows a qualitative example of variation in the cost of insulation, energy cost savings and payback period for a typical industrial insulation system. The savings are directly related to reduction in heat loss or energy cost savings; therefore, the optimum thickness will be directly affected by the energy cost. Most suppliers have developed “rules of thumb” for applicable insulation thickness based on certain energy costs. Users should always ask for an explanation of such rules because they may not necessarily give you the optimum values when energy costs rise substantially.
Figure 3. Variation in Insulation Cost, Energy Cost Savings and Payback Period
The cost of an insulation material relates to its temperature capability. Hence, insulation and refractory systems are designed to include several layers of different materials that offer optimum economic performance.
In some cases, the most economical thickness may not meet regulatory requirements for the safety of personnel and property, and appropriate design and materials should be used. In other cases, thickness may be reduced when there is a danger of exceeding the limiting refractory or insulating temperature.
A number of tools and design methods are available for selecting the most economical or appropriate refractories or insulation:
-
3E Plus software, developed jointly by the Department of Energy’s Industrial Technologies Program and the North American Insulation Manufacturer’s Association (NAIMA), can be used to calculate and select the insulation thickness for a variety of conditions.
-
The Process Heating Assessment and Survey Tool (PHAST) can be used for preliminary selection of insulating and refractory materials for high-temperature furnaces.
-
Several insulating material suppliers use their own software programs to design insulation systems for a given application using their own materials with more accurate values of thermal properties. These programs allow users to select a number of combinations of the available materials and calculate heat losses, surface temperature and heat storage for the selected system.
This article appeared in the Winter 2009 issue of Energy Matters, produced by the U.S. Department of Energy. For more information, visit http://www.eere.energy.gov/.
References:
-
Improving Process Heating System Performance: A Sourcebook for Industry, Second Edition (PDF 2.4 MB) Download Adobe Reader.
-
ITP BestPractices process heating system tip sheets
-
Improving Steam System Performance: A Sourcebook for Industry (PDF 1.3 MB) Download Adobe Reader.
-
ITP BestPractices steam system tip sheets.
Read more Energy Matters articles on these topics:
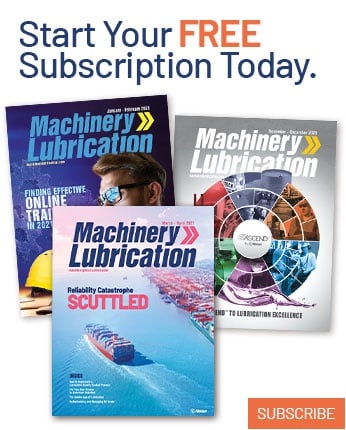