Forest City Gear on December 12 announced it has invested more than $6 million in the purchase of new capital equipment for the manufacture of gears, during the last 18 months. According to CEO Fred Young, this reinvestment of revenue was made for a variety of reasons, primarily to expand the company’s manufacturing capabilities and to maintain Forest City Gear’s industry-wide reputation for staying on the leading edge of manufacturing technology.
“Our customers expect Forest City Gear always to lead the way in devising new production techniques to make better gears for them, at competitive cost and with superior service. That’s a tall order, but it’s one we welcome,” said Young. “Our track record speaks for itself in this area, as Forest City Gear has reinvested an average between 25 percent and 40 percent of our annual revenue for the last 30 years in the purchase of gearmaking machinery and ancillary equipment. In addition, we’ve made some major investments in green technology, over the last two years.”
He further explained the company’s strategy in purchasing new, high-technology equipment at Forest City Gear. “We always buy high-end equipment, not only because it generally affords us higher quality, service and training from our suppliers, but also because we realize better performance, lower maintenance requirements, better trade-in value and more substantial depreciation allowances.”
Young also commented that one impetus for these new purchases was the company’s success in supplying many of the gears on the 2011 Mars Rover, a win achieved in part because of the previous investment in leading edge technology. “We never wait until we get an order to buy machines with enhanced capability. We already have it and have developed it, before we start exploring new opportunities. That’s a real advantage for FCG.”
Gene Fann, gear technology manager at Forest City Gear, joined Fred Young in detailing these recent equipment purchases and the new capabilities that resulted from this substantial investment. These include:
· Gleason PSA 500 gear shaper with electronic helical guide to eliminate the need for helical lead guides; special face gear attachment (perhaps the only one in the USA presently) allows increased shaping capability, more prototype capability and shorter lead times, along with more accurate face gears, which in some instances can substitute for bevel gears
· Gleason PSA 300 gear shaper with electronic helical guide and automatic column inclination, also accepting our face gear attachment
· Fellows/Bourn & Koch MS450-125 CNC gear shapers with radial crowning and electronic helical guideless shaping
· Koepfer 200 CNC 7-axis gear hobbers with automatic loading and worm-milling high-helix hob head
· Koepfer MZ130 CNC 5000 rpm gear hobber with auto-load gear and worm hobber; expands the company’s size range in gear diameter and diametral pitch
· Hofler Helix 400 SK gear grinder, using a 20mm dia. CBN wheel for closer to shoulder tolerances on cluster gears
· Samputensili RI 400 CNC 5-axis twin generating and form gear grinder with linear motors for precise positioning down to 0.001mm, according to the builder
· Samputensili RI 375 CNC gear and thread grinder with internal, spur and helical gear grinding; highly modified profiles and crowned teeth to 400mm diameter and shafts up to a meter in length can be machined in this grinder, along with worm and special thread form grinding
· Wenzel Gear Tec LH87 CMM with rotary table; up to 900mm diameter gears inspected and large bore to accommodate long shafts
· Wenzel Gear Tec WGT 600 CNC analytical checker with air bearing technology; said to be the most accurate in the industry
· Mitutoyo Digimatic Model HDS H24C height gages
· Sunnen SV1005 automated honing machine
· (2) Kellenberger Kel-Vista Type UR Model 175-600 universal cylindrical grinding machines; ID grind capability, size monitoring devices, flagging devices; allows bump grind and hold face widths on pump gears to 0.0003”
· Centric Senjo Seike PLC 101SAII automatic chamfering machine with swivel; allows constant depth chamfering around the periphery of a gear tooth
· Hurco VM1 machining centers for increased secondary operations
· Jenfab Mini Belt inline cellular spray washer/dryer with oil scavenge
· Star/SU PTG-1 hob and shaper cutter sharpener; Class AA tolerance work
· Retrofit on an isotropic superfinishing REM tumbler
· Installation of an Oberlin filtration system with environmentally-friendly chiller; when temperature is 50ºF or lower, outside air is used for chilling the grinding oil; includes advanced oil capturing and scavenging system
“With all this new equipment,” Young notes, “we’ve needed substantial training from our suppliers. What we’ve enjoyed as a collateral benefit is the cross-pollination from other customers’ plants around the world. This has made us a better gear company, I’m certain.”
Young also mentions that Forest City Gear frequently sells gears to its competitors, based on the advanced technology developed at his company. “We really believe in raising the bar for our entire industry. It gives us a competitive advantage, of course, but it’s also a benefit to American manufacturers, who represent our customer base and our future in business.”
Forest City Gear was founded in Rockford, Ill., in 1955 by Evelyn and Stetler Young, parents of the current CEO, Fred Young.
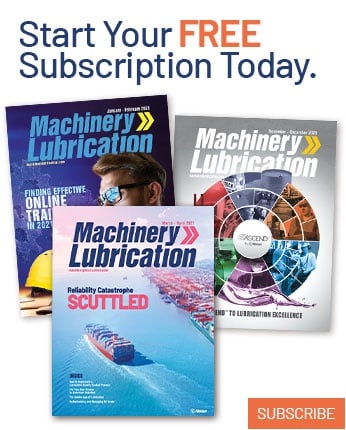