“Using energy efficiently is cool again,” says Paul Twite, referring to the current high cost of energy.
Twite is a power quality engineer, a Level II certified thermographer and a co-owner of 24-7 Power, an electrical consulting and engineering service company in the business of helping other companies discover and fix their energy inefficiencies. 24-7 Power is also a full-service manufacturers’ representative for many of the instruments Twite uses in energy audits.
Figure 1. A three-phase power logger can measure demand over time, which can help identify areas where companies can cut energy costs.
Twite uses a three-step approach to help a company lower its energy bills. With the right tools and knowledge, your company can follow the same process using your own personnel. Here’s how it works:
Step 1: Energy accounting
This step consists of three parts: 1) reviewing utility bills, 2) using thermal imagers to scan the electrical, mechanical, process and HVAC (heating, ventilation and air-conditioning) systems as well as the building envelope (everything that separates the interior of a building from the outdoor environment) and 3) monitoring for power consumption, power quality, power factor and other relevant aspects of energy use.
Reviewing utility bills reveals what your utility is charging for the electricity they say you used, but it will also reveal any utility demand charges and/or power factor penalties assessed. Any and all of these charges require follow-up monitoring to confirm that the utility’s metering is accurate, that you are getting what you’re paying for and that you are not paying excessive penalties.
“Utility meters have been known to drift out of calibration or malfunction over time, so we feel it’s good to double-check the utility as a regular part of the energy auditing process,” Twite reports.
Scanning electrical, mechanical and HVAC systems and the building envelope using thermal imagers can reveal overloaded or imbalanced circuits, loose connections, overheating motors on HVAC equipment, malfunctioning steam traps, and a host of other conditions that might signal an inefficient use of energy.
Twite compares using a thermal imager (infrared camera) in energy auditing to your doctor’s use of a stethoscope during an annual checkup.
“If you go in for a physical exam, the first tool the health care provider will pull out is a stethoscope,” he says. “While this tool is not sufficient for the health care provider to say, ‘I’m sorry, you have a serious problem,’ it is sufficient for a determination such as, ‘Hmm, that sounds odd. Maybe we should order some more tests.’ In my opinion, thermography is like that stethoscope. It is an extremely powerful tool, but it is most potent when it is used in combination with several other tools.”
So, Twite has a host of diagnostic equipment at his disposal when he does a commercial energy audit.
“Typically, I travel with a four-wheeled utility cart loaded with tools and personal protective equipment (PPE),” he explains. “It carries my thermal imager, three-phase power logger, vibration analysis equipment, ultrasonic listening equipment and a digital autoranging multimeter. When I find what appears to be a problem area with my thermal imager, I have several resources to fall back on.”
Monitoring for power consumption, power quality and power factor can be used to follow up on issues or unusual anomalies identified by the use of a thermal imager. The appropriate meter can also identify harmonics and other internally caused power interruptions that may affect machine performance. Additionally, the right tool can measure peak demand and power factor, which are the focus of what follows.
Utilities set demand charges. Often they are higher in the summer and at certain times of day. A utility also typically sets demand intervals; 15 minutes is common. Based on these, your utility will monitor the amount of power your facility consumes several times an hour based on the average demand for each interval. Peak demand is the highest average demand during all of the intervals in a billing cycle. If, for example, your facility’s normal demand is about 500 kilowatts (kW), but three large process pumps start at once and your demand hits 600 kW at 4 p.m. on a weekday in July, the episode could be costly. If the utility’s demand charge is $100, then peak demand penalties for July would be (600 kW-500 kW) x $100 = $10,000 (U.S.).
A three-phase power logger like the Fluke 1735, or a three-phase power quality analyzer like the Fluke 435, can measure demand over time, pinpointing large loads operating concurrently and verifying readings for individual loads.
Some utilities also penalize for a low power factor (PF), which indicates the customer is not efficiently using the power supplied to it. Twite says that by using a thermal imager, in conjunction with other power analyzing instruments, you can quickly identify power consumption and inefficiency issues if any of the feeders or neutral conductors appears warmer than ambient temperature conditions. This thermal imbalance also may be due to a high harmonic content on the circuit or could be indicative of broken rotor bars, windings or failing bearings on a motor circuit.
“That’s why it’s important to blend thermal imaging and power analysis to gain a clear perspective on what is happening with the electrical distribution,” says Twite.
Twite explains power factor this way: “Suppose you are a machine shop and you have a lot of arc welding and machine tools – end mills, CNC machines and the like – that cycle on and off. A high current load cycling on and off on a regular basis could lead to a significant PF problem. The difference between how energy is delivered to you and how you use it is the power factor. It’s just a ratio between the apparent power and the applied power (Power/VA=PF).”
A purely resistive linear load can have a perfect PF of 1.00, but your utility may charge a healthy penalty for a PF that dips below a certain level, say 0.90. For example, the utility might add one percent of demand charge for each hundredth (0.01) your facility averages below a PF of 0.90. So, if your operations have an average PF of 0.88 each month and your demand charge is $6,000, then you will pay $5,400 in PF penalties annually.
With a good power quality meter, you can measure and validate your average PF over time. Twite emphasizes that all he does during the first step in an energy audit is collect data from utility bills, thermal imagers and meters; then blend the data from those three sources and do a “roll call” of the power-consuming equipment and devices inside the plant.
“The goal of Step 1,” he says, “is to come up with an energy accounting spread sheet which addresses the question, ‘Where is all the energy going?’”
The power quality engineer says that in-house personnel usually can perform the accounting phase of an energy audit as long as they have a little electrical savvy along with training in using the monitoring equipment safely. It is, of course, critical always to keep in mind arc flash hazards and awareness of high energy potentials.
“There is no certification or college degree required,” he points out, “and it’s usually not necessary to be a licensed electrician. You should, however, consult with your company’s safety manager if you plan on self-performing this work.”
Step 2: Analysis and identifying problems
In the second step of an energy audit, Twite analyzes the data collected in Step 1, asking questions such as: Do I have an overloaded circuit? Do I have a loose connection? Do I have phase imbalance? Why is the circuit overloaded? Is that motor running hot because of an alignment problem, a lubrication problem or a bad bearing?
Often the auditor must look at the bigger picture: What process does this circuit feed? What about the process is causing power factor problems or peak demand problems?
Also in this step, the auditor assesses the age and efficiency of lighting systems, HVAC systems, motors and drives, and other plant equipment and systems.
“By reviewing the nameplate data on equipment, or metering the point load or checking for unusual hot spots with a thermal imager – or better yet, a combination of the three – you can make a pretty solid determination of the useful life of the equipment. Sometimes the quickest route to the biggest energy savings is simply replacing old, inefficient equipment with new, more efficient versions,” Twite adds.
Step 3: Proposing and prioritizing solutions
The third step is not really auditing. It consists of engineering solutions to problems uncovered in Steps 1 and 2.
“In Step 3, I’m trying to figure out different strategies to lower the energy bills,” Twite says. “To be effective in this step, you (or your auditor) have to have an engineering background or at least have been in the energy business for a while. You need to understand how everything affects your energy costs.”
Step 3, then, is proposing and prioritizing ways to lower your energy bills. There are at least three kinds of things that might be done to achieve that goal: 1) adjust processes, 2) repair faulty equipment and 3) replace inefficient systems and equipment.
Once the action items for improvement are identified, then traditional return on investment (ROI) calculations can be used to help prioritize them. In what follows, some typical payback periods are included. Most come from Paul Twite’s years of experience helping companies cut their energy bills.
Adjusting processes is often the most expedient way to eliminate demand charges and power factor penalties. Maybe process controls can be set to disallow those three large process pumps mentioned earlier from all kicking on at the same time. Or, maybe there are electric water heaters that tend to run during peak demand periods, but you have enough water-heating capacity to allow you to push the water heating until after 10 p.m., when electric rates are lower. The calculations you did using energy bills and the confirmation of their correctness using a power quality analyzer will provide the data required for calculating the ROI for such strategies.
In another kind of process adjustment, you can immediately improve PF by the installation of power-factor capacitors either at the entrance of your service or at the point load. Twite uses the following analogy: As your big machines are cycling on and off, the capacitors act much like sponges that soak up water, except capacitors “soak up” electricity. Then, just as water comes out when you squeeze the sponge, a capacitor “squeezes out” electricity when your voltage starts to dip. It fills in the low spots and trims off the high spots of your electricity profile.
Twite notes that in many cases with very steep power factor penalties, capacitors can pay for themselves within 30 to 60 days.
“In fact, we have seen manufacturing customers with low power factor getting charged over $1,000 a month on their energy bills. For those manufacturers, 24-7 Power has installed correctly-sized capacitor banks and verified an immediate improvement in the overall power factor and resulting drop in kW demand. In some cases, the entire installation was paid for in 60 days by energy savings.”
Repairing faulty equipment should follow from listing the problems that thermography uncovered in the electrical distribution system. Such problems might include loose or corroded connections, phase imbalance or worn insulation. Similarly, misaligned sheaves might be revealed by overheating. Laser alignment equipment can help fix that problem. In some cases, a motor bearing that is starved for lubrication can cause the motor to run hotter and use more energy. In that case, simple lubrication can significantly cut temperatures and full load current.
Of course, the repairs that should take priority are those that threaten a production stoppage followed by those with low cost of repair and/or quick payback. Twite points out, for example, that building-envelope problems (except for some roof problems) have relatively long payback periods. Typically, these will get a much lower priority in Step 3 than, say, installing power-factor capacitors.
Replacing inefficient systems and equipment goes far beyond peak shaving. Often, following an audit, Twite recommends replacing an old HID or other inefficient lighting system with a new, high-efficiency compact or linear fluorescent system. He points out that the U.S. Department of Energy lists the two biggest energy consumers in most plants as the HVAC and lighting systems.
“Upgrading to an energy-efficient lighting system can offer the easiest and quickest payback,” he says. “In many cases, it’s usually less than a year, especially if your utility company participates in the form of rebates.”
Other recommendations he often makes to his clients are adding new premium efficient motors that have 94 percent NEMA ratings as opposed to 80 percent ratings. Twite says, “Many motors from the 1930s and 1940s are built like tanks, and are still running today. However, new motors with the same horsepower rating use a lot less energy.”
Looking for rebates paid by utilities for the installation of energy efficient equipment and systems is something every company should do. Twite notes that to build a new coal-fired generating plant can take 12 to 14 years. One of the simplest ways that large, power-generating utilities can continue to run profitably is to lower demand by encouraging companies to cut energy consumption by using equipment that is more efficient.
Twite notes that not all rebate programs are the same and recommends that you check with your utility to see what is available.
This article was provided by the Fluke Corporation. To learn more, visit www.fluke.com.
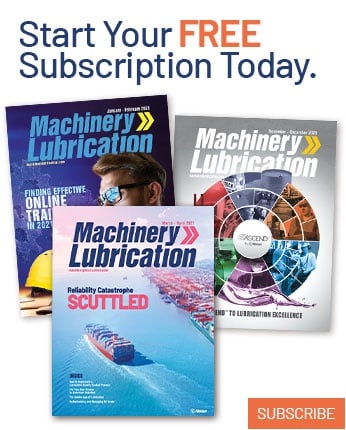