Research and Markets ( http://www.researchandmarkets.com/research/e92111/lean_manufacturing) has announced the addition of the "Lean Manufacturing" report to its offering.
Why is lean manufacturing or lean thinking so prevalent in the modern current economies of scale? To remain competitive, agile and the lowest-cost producers, providers and streamlined business, getting rid of waste and being highly, consistently and sustainable is key for survival and thriving in this new economy.
Authors Jim Womack and Dan Jones define lean thinking as a set or collection of “efficiency tools” that you can unleash in your business to save money, reduce cost and waste and deliver consistent and effective service that is affordable and pleasing to your customers. It is about vision and tools for reducing variability and cutting down on waste, being efficient and running a smooth and competitive, even profitable operation, well.
Some have referred to lean manufacturing as the Toyota Production System, or JIT (just-in-time) manufacturing, paying attention to things like flow productions, line operations, value streams and kaizen. In any lean manufacturing process and approach, there are a couple of things to pay attention to. There is discipline, planning, rigor, scientific approach and statistically based tools required and applied to make this business paradigm fit, work and last.
Lean manufacturing will help you in your business take a serious look at visible causes and effects in your business. Aspects that could get some attention could include things like:
- Inventory;
- Movement/motion;
- Waiting or queues;
- Broken machines or tools (missing);
- Dirt and clutter; and
- Noise.
... And many others.
Things that we can see that are obvious waste or inefficiencies attract attention and demand action. This is where lean manufacturing steps in and makes the difference. It deals with the problems that we can actually see and do something about.
Key Topics Covered:
· Executive Summary
· Introduction
· Types of Waste
· History of Waste Reduction
· Pre-20th Century
· 20th Century
· Toyota Develops Lean Thinking
· What is Lean Manufacturing and Which Tools Can I Use in My Business?
· Why use Lean Manufacturing?
· Benefits of Lean Manufacturing
· Lowering Overhead Cost and Inventory through Lean Manufacturing
· Lean Implementation
· Problems with Lean Manufacturing
· The Process of Lean Manufacturing
· Step 1: Leadership and Commitment
· Step 2: Educate and Empower
· Step 3: Making Things Visible to All and Accountability
· Step 4: Focused Improvement Activities and Advanced Lean Tools
· Lean Manufacturing Tools
· 5-S
o Phase 1 - Seiri (Sorting)
o Phase 2 - Seiton (Straighten or Set in Order)
o Phase 3 - Seiso (Sweeping)
o Phase 4 - Seiketsu (Standardizing)
o Phase 5 - Shitsuke (Sustaining)
· Cellular Manufacturing
· Process Design
· Product Design
· Implementation of Cellular Manufacturing
· Advantages and Costs of Cellular Manufacturing
· Mistake-Proofing (Poka-Yoke)
· Set-up Reduction
· Questions, Diagnostics, and Assessments
· Operational and Economic Benefits or Metrics
· Where to Apply LM in Your Business
· Leadership
· Infrastructure, Support, and Deployment
· Vision
· Right Resources and Projects
· Teamwork
· Process and Tools
· Making it the Way You Do Business
· Key Lean Manufacturing Principles
· Related Concepts
· Six Sigma
· Toyota Production System
· Theory of Constraints
· Conclusion
For more information, visit http://www.researchandmarkets.com/research/e92111/lean_manufacturing.
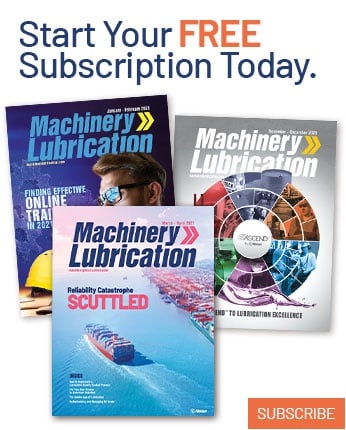