When designing a robotic work cell, integrators and end-users must take into account many variables and components to ensure its success. Cabling is one element of robotic work cells that is often overlooked during the design phase.
Without proper planning, cable wear can be one of the first things to cause downtime on a robot work cell. Top experts talk about some of the most important cabling considerations in this article, and industry leaders will be on hand in Orlando, Fla., on November 5-7 at the 16th annual Robotics Industry Forum, where attendees make appointments to talk in detail about good business practices.
“Cables are often just an afterthought in work cells. After the end-of-arm tooling is selected, the programming is done and safety mechanisms are installed, the last thought is usually the cabling,” says Wayne Murphy, product manager at igus of East Providence, R.I. “Cables are the component that will give the work cell the most trouble, so engineering them later will be more difficult. If cable routing is engineered during the design of the work cell, integrators can plan for them correctly.”
Correct Cabling
A common error made by integrators and end-users in cabling is using the wrong type of cable in an application. Mark Noschang, applications engineering manager with Adept Inc. of Livermore, Calif., says, “A common mistake is not using the proper cabling for the job. Frequently, standard cabling is used where high-flex cable is required. The impact of repetitive motions on the cabling is magnified with faster robots, causing cabling used for end-of-arm tooling to wear prematurely.”
Kevin Marston, managing director with SAB North America of Fairfield, N.J., agrees with Noschang, saying, “The most common mistake is the most elementary. We replace many cables that were not designed for the application.”
Marston maintains that first-time users should test the capabilities of the cables before designing them into new work cells. “End-users and integrators can plan for proper maintenance cycles,” he says. “Many times, the cables are overlooked until the design is almost finished and then it becomes a problem because of cable size or function.”
Demanding applications like welding or foundry work cells place special demands on cables.
“Many integrators use off-the-shelf cables that are not intended for a flexing environment. The jackets on those cables will not withstand the rigors of weld flash or metal chips” says Mitchell Yencha, manufacturing representative at Applied Robotics of Glenville, N.Y.
“Integrators do not take into account the bend radius required as well as how cables need to be protected,” suggests Richard Deutsch, general sales manager at Murrplastik Systems Inc., Hatfield, Pa. “End-users should contact their cable supplier for suggestions on how to protect their cable by using conduit and cable drag chains.”
Incorrectly installing cables is another common mistake made when setting up a robotic work cell, says Thomas Collen, director of marketing at Northwire Inc. of Osceola, Wis. “The most common problem is incorrect installation. Often, cables are tied down too tightly with tie wraps on something that is moving. Another common problem is overfilling cable carriers and cable tracks. Ideally, cables are able to remain flexible when put into carriers and tracks.”
Collen adds that inaccurately underestimating the bend radius that the cable needs to be put through causes cracks and conductors to fail.
Collen’s sentiment is echoed by John A. Cooper, general manager with LEONI Engineering Products and Services of Troy, Mich. Cooper points out, “End-users must ensure that they have the right cable product for their application. Some cable suppliers offer items intended for high-flex linear applications when equivalent torsional designs are not available.”
End-users must make the distinction between how a cable will bend or twist torsionally on a particular robot axis, observes Michael Calardo, director of ABB Inc.’s Automotive Robot Products Division, Auburn Hills, Mich. “A cable bunch has individual wires that are twisted around each other to allow even distribution while bending. When axis rotation causes a cable to torsionally twist, the cables in the bunch must stay parallel with respect to each other to minimize stretching.”
Long Enough but Not too Long
Having cables of the proper length is fundamental to the success of a robotic work cell, asserts Uday Pathre, device building manager with DELMIA Corporation, Auburn Hills, Mich. “Integrators must make sure cables are long enough to be connected properly, but if too long, they could get snagged. End-users can save time and money by simulating the robotic system before it gets to the factory floor.”
Pathre says that simulation systems help in determining the behavior of cables in the actual work cell.
Flexing vs. Twisting
End-users need to distinguish between applications where cables are continuously flexing and those that are designed for torsion. The difference is explained by Timothy Phillips, product manager for Lapp USA, Florham Park, N.J. "End-users must be clear on what application the cable will be used for as well as the difference between continuous flexing and torsion cables."
Phillips goes on to say that flexing cables are subjected to constant bending when installed in a cable track. Torsional applications have cables twisted longitudinally in a back and forth motion while operating on an articulating robotic arm.
Phillips mentions that some robotic cables are subjected to both flexing and torsional stresses. "Some cables are strictly for torsion while others are rated for both torsion and bending. How the cable will be applied in the work cell determines the type of cable end-users should install." Phillips recommends that integrators look at performance characteristics of the application when ascertaining which cable to install. "A cable might be designed for only 180 degrees of torsion rather than 360 degrees. Look at the parameters of how the cable is designed and compare that to the requirements of the application.”
Cooper notes that end-users sometimes underestimate the demanding nature of robotic work cells. “Cables designed specifically for robotic applications may appear to the non-specialist little different from static cables, but have an enormous difference in life cycle performance. Cables validated in high cycle endurance testing for torsion and flexibility can provide reduced costs in unplanned maintenance and interrupted production.” Robotic cables can be expected to perform 10 to 20 million torsion cycles or flex cycles when the cable is properly routed and installed, reports Cooper.
Murphy of igus says because a cable is flexible does not mean that cable is very bendable. “Flexing cable is not necessarily the most supple or most bendable cable. The structure inside the cable, such as the conductors, can disintegrate with movement.” Murphy recommends bundled conductors.
A flexible robotic cable is not necessarily one that has a long flex life, says Dennis Anweiler, business unit manager at Draka Cableteq USA of North Dighton, Mass. “Because a cable is flexible does not mean it can provide long flex life. I have found that if end-users use a very small gauge cable for increased flexibility, that cable might provide less flex life over time.” Anweiler continues, saying, “Smaller strands tend to decay more quickly than heavier gauge strands. End-users need cable that provides long flex life, not just cables that are flexible.” He recommends that end-users invest in cables that have been tested and have a sufficient warrantee.
Firm but Not Rigid
Securing cables in robotic work cells is important but caution must be exercised to prevent making them too tight, warns Ernest Aughenbaugh, engineering manager, at Güdel Inc. (Ann Arbor, Mich.). “A common mistake is not calculating final cable count and size for energy chain fill. Cables need to be restricted to prevent twisting among other cable but have space to move to prevent damage.” Overfilling an energy chain can cause premature cable wear and failure, contends Aughenbaugh.
At the same time, care must be taken to prevent over-tightening cables emphasizes Anweiler. “A common mistake is over-clamping cables that restrict their movement. Another mistake is importing twists into the cable during installation and not letting the cable relax.”
"If cables are installed with too much tension or integrators do not provide for enough movement for torsion, cables may break and fail in the application," remarks Phillips of Lapp. Aside from determining the optimal length for each cable in a work cell, integrators and end-users need to think about the possibility of cables wrapping around the robot's arm, snagging on other peripheral equipment during movement, as well as becoming entangled with other cables. Cables and other loose components, such as hoses, must be organized, protected and secured.
“Improperly securing the cables in the energy supply system is a mistake made by some integrators. If the cables are not properly secured inside of a dress pack, they will twist among each other during the robot’s motion,” describes Michael Maximiuk, engineering manager at KUKA Robotics Corporation, Clinton Township, Mich. “This twisting causes excessive wear as well as restricting the motion of cables as they bind with each other.”
No Cables
High on the wish list of end-users is to utilize wireless technologies in place of some cables. Robert Winkel, senior product development engineer with FANUC Robotics America Inc. of Rochester Hills, Mich., addresses the desire for wireless work cells. “FANUC’s customers continuously inquire when wireless technologies will be used on robots. While we have seen an advance in some wireless communication equipment, these technologies still must be better validated in an industrial environment before they can be used to eliminate cables in robot systems.”
While end-users would like to see the elimination of cables thorough a wireless system, some robot manufacturers are offering machines with cables routed internally. Motoman Inc., West Carrollton, Ohio, is among those marketing robots with internal cables. “Motoman offers application-specific robots, where most cables are internally routed to maximize cable life,” says Thomas Sipple, handling technology leader at Motoman. “With externally routed cables, end-users have more issues with them. When cables are routed internally, end-users do not have to worry about snagging, which maximizes cable life.”
Manufacturers are developing “smart” cabling, which can indicate to end-users that it is fatiguing or has too much tension on it. This will provide the ability to perform preventative maintenance as necessary, cutting down-time.
Making Connections
At this year’s Robotics Industry Forum, cable makers will be able to connect with others in the industry to exchange ideas and network. A continuing popular feature of the Forum is “Connectionering,” 20-minute pre-arranged meetings between end-users and top experts in the robotics industry.
In addition to Connectionering meetings, several speakers will discuss public policy, the state of the world’s economy and new horizons for the robotics market.
Stuart Shepherd, KUKA’s president, is looking forward to attending all sessions offered at the Forum. “I am particularly interested in hearing what Peter Kane of Evergreen Solar Inc. (Marlboro, Massachusetts) and Henning Behrens of Rosenberger AG (Simonswald, Germany), have to say. I also like to get updates from industry experts who bring data from other perspectives.” Kane’s talk is entitled “Solar Energy: A Hot Market for Automation,” while Rosenberger will speak on “An Effective Method of Producing Tube Combination Assemblies with a Robotic System.”
Accompanying Behrens and Kane on the agenda is Robert Axtman, DELMIA’s executive director of worldwide marketing, who will speak on “Experience Manufacturing Excellence.” “My presentation will cover three-dimensional simulation for robotic manufacturing as it relates to off-line programming (OLP). I will talk about experiencing virtual manufacturing with robotics before deploying actual equipment.”
Axtman previews his offering, saying, “I will show the metrics of cost-savings for industry by using robotic simulation programs. I want to introduce OLP and three-dimensional simulation to those who are not using them, as well as show how much time and money they can save.” End-users need to use simulation and OLP to have truly lean manufacturing. “OLP reduces waste of materials, waste of time, costs and inventory. Manufacturers must take advantage of everything available today to be lean,” Axtman says.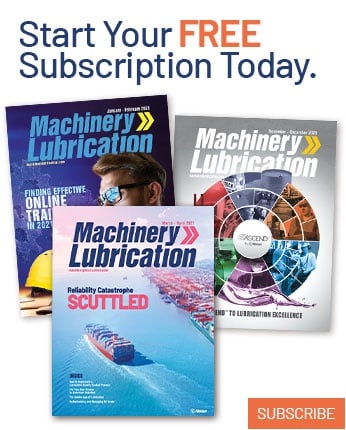