Researchers at the National Institute of Standards and Technology (NIST) and Colorado School of Mines (CSM) have developed a prototype sensor that quickly detects very small amounts of hydrogen accumulation in coated pipeline steel. The new sensor could provide early warning of pipes that have accumulated excessive amounts of hydrogen – a notorious source of embrittlement – and avert potentially disastrous failures of pipelines carrying hydrogen fuel.
Hydrogen is attractive as a fuel because it burns cleanly without carbon emissions and can be derived from domestic sources. However one long-recognized challenge is that hydrogen can cause gradual embrittlement in conventional pipelines by slowly diffusing into the metal. The NIST/CSM sensor, described today at the seventh International Pipeline Conference,* could monitor for hydrogen buildup before a pipeline actually fails in service, or during testing or production.
The nondestructive, non-contact hydrogen sensor is approximately 4 square inches and is designed to be a portable sensor to make measurements on excavated or unexcavated pipeline steels. The sensor sends a current through the pipe and measures changes in impedance (resistance with a function of depth) as an indicator of hydrogen content within the steel and the overall steel pipe integrity. The hydrogen sensor is based on electromagnetic concepts to generate alternating currents into the pipeline steel, which in turn induces an opposing magnetic field. Any change in the hydrogen content in the steel modifies the current, resistivity, and thus the impedance.
NIST laboratory and field test results show that a pipe’s impedance, and thus resistivity, increases with increasing hydrogen content. The measurement sensitivity is exceptional: the sensor can measure hydrogen content levels in pipeline steel well below 1 part per million (ppm). High strength pipeline steels can tolerate only a few parts per million of hydrogen before significant problems arise. By contrast, conventional analytical techniques do not have sensitivity or accuracy below 1 ppm. The new hydrogen sensor also acts as a forewarning or preventative monitoring system to detect the agents that actually cause the flaws, cracks and defects before they arise. Most traditional nondestructive tools used in the pipeline industry (such as ultrasonics and magnetic flux leakage) are used for determination of cracks, corrosion or other flaws that have already occurred.
The sensor development was supported in part by the Minerals Management Service and Department of Transportation.
* A. Lasseigne, K. Koenig, J. Jackson, D. Olson, B. Mishra, T.A. Siewert and J.D. McColskey. Advanced non-destructive hydrogen sensors to prevent material degradation from hydrogen damage. Paper presented Oct. 1 at IPC2008, 7th International Pipeline Conference, September 29 to October 3, 2008, Calgary, Alberta, Canada.
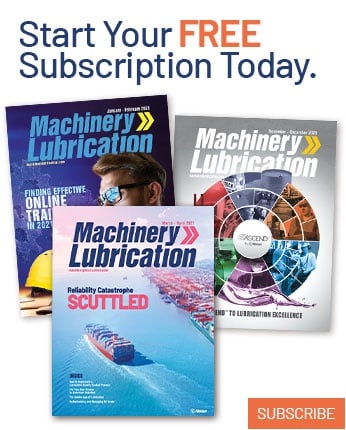