With energy costs projected to rise as much as 12 percent this year and "carbon footprint" an issue of increasing importance, plants are taking a hard look at their energy consumption. Facilities can save tens of thousands of dollars in yearly electric costs, and cut harmful emissions by thousands of tons, by implementing a handful of simple, cost-effective efficiency measures. While efficiency investments of every size and cost are possible, this article addresses those measures which reduce electrical consumption and have a payback period of three years or less. There are three areas of "low-hanging fruit" for a facility seeking to lower electric costs: electrical motors, cooling systems and lighting.
Figure 1. Capacitor (gray rectangular box) attached to a 40-horsepower lathe to improve power factor and motor efficiency.
MOTORSThe main opportunity for fast-payback electrical savings in plants is by addressing rotating electrical motors, including drives, pumps and compressors. These are found in most industrial machinery, and in heating and cooling equipment such as fans, air handlers, boilers and air conditioning units. Motors can account for up to 90 percent of a facility's electric bill and are inherently inefficient in two ways. First, because they typically lack the ability to vary their speed, they may run at full speed even when the device they are driving (such as a fan, pump or blower) does not require it.
Second, motors rely on both "active" power and "reactive" power. Imagine pushing a ball across a field which slopes to the side; active power is the force that drives the ball across the field, and reactive power is the force that keeps the ball from rolling down the slope. "Power factor" measures the relationship between active power and reactive power. If the field in this analogy was level, requiring no reactive power, power factor would be 100. Motors typically run at a power factor of 80 or 90 out of 100, representing a potential efficiency loss of 10 to 20 percent. An idling motor, or one not under load, runs at an even lower power factor - sometimes as low as 50. A motor running at a power factor less than 100 is inefficient in two ways. First, the motor demands extra current to compensate for the power factor deficiency, which increases the electric bill, and second, the extra current causes the motor to run hotter, which reduces its life span. Correcting a motor to reduce its electrical consumption by 10 percent can increase the motor's life by 50 percent.
Figure 2. Harmonic filtering and canceling devices installed at lighting panel to reduce harmonic distortion.
One way to improve a motor's efficiency is to regulate it with a variable frequency drive (VFD). This allows the motor's speed to change with the changing demands of the device it is driving, such as a fan, pump or blower. A VFD can reduce a motor's electrical consumption by 10 percent or more.
Another way to help a motor run more efficiently is to increase its power factor by attaching a capacitor to the motor (Figure 1). A capacitor acts like a short-term battery, regularly storing and discharging current as necessary to provide power to the motor in a more efficient manner. In fact, a capacitor can be attached to a motor fitted with a VFD, and it will help both the motor and the VFD operate more efficiently. When addressing low power factor, it may be prudent to install capacitors in banks at electric panels, individually at particular loads or both.
Low power factor is generally a problem when a facility has many motors. Electric utilities impose a surcharge when power factor falls below a designated threshold, such as 90. To determine whether a building has a power factor problem, check the building's electric bill for any extraordinary charges related to power factor (e.g., "Power Factor Adjustment").
COOLING SYSTEMSCooling systems - refrigeration and air conditioning - use compressors and refrigerant to cool water and air. These systems can represent a large component of a plant's electric bill - sometimes accounting for as much as 30 percent of the total cost. There are three cost-effective ways to improve the efficiency of cooling systems:
-
implement controls to optimize the operation of mechanical components;
-
add oil lubricants to refrigerant; and
-
treat fans and compressors to improve operating efficiency.
Various controls can be used to improve the efficiency of cooling systems' components. Such controls include:
-
Fan speed control - uses pressure or temperature signals to control fan speed, reducing electrical consumption when operating at lower speeds.
-
Lube oil control - monitors and controls compressor lube oil circuits to ensure proper lubrication and efficient operation.
-
Defrost control - improves the efficiency of the defrost cycle by defrosting on demand rather than on a simple timer.
Implementing a set of controls can lower a cooling system's electricity consumption by 10 percent or more. With payback periods as short as one year in some cases, these controls are a great place to start for a facility seeking to immediately lower its electric bills.
Another way to improve a cooling system's efficiency is to add oil lubricants to the refrigerant. Oil lubricants serve to reduce friction in the compressor's moving parts, improving mechanical efficiency and lowering power consumption. Such additives may also provide other benefits, such as reducing wear on bearings and improving seal life.
Finally, as discussed in the section on motors, you can lower cooling systems' electrical consumption by improving the efficiency of rotating motors that drive compressors and fans.
LIGHTINGLighting is another large piece of a plant's electric cost, sometimes as much as 20 percent of the monthly bill. Most plants understand the need to replace incandescent lighting with fluorescent lighting and have already taken this important step. However, where fluorescent lighting is prevalent in a facility, it can create a new problem: harmonic distortion. This is a disruptive force in a building's electrical system which causes lights to consume more power and operate at higher temperature.
Harmonic distortion can be treated with harmonic cancellers or filters. These devices are typically installed at a lighting panel or fixture, and they work to eliminate harmonics and improve the electrical system's efficiency. There's a great side benefit of installing such corrective devices - they will actually cause other electrical loads in the system (such as computers, printers and monitors) to use less power and operate at lower temperatures.
Lighting can also be made more efficient by the use of controllers. Lighting controllers can serve to reduce overall voltage, or to turn fixtures off or on depending on time, area occupancy or other factors. Of course, the least expensive lighting controllers are posted signs reminding personnel to turn off lights when an area is not in use.
THE BOTTOM LINE
What can these efficiency measures achieve in financial and ecological benefits? By correcting electrical inefficiencies using the fast-payback methods described above, a plant can lower its electric consumption by 10 percent or more. At a facility using 500,000 kilowatt hours monthly, a 10 percent reduction would lower annual electric bills by $60,000 or more and annual carbon emissions by 500,000 pounds.
David Simon is the chief executive officer of Evergreen Energy Solutions, an energy consulting firm. For more information,
visit www.evergreensolves.com, e-mail david.simon@evergreensolves.com or call
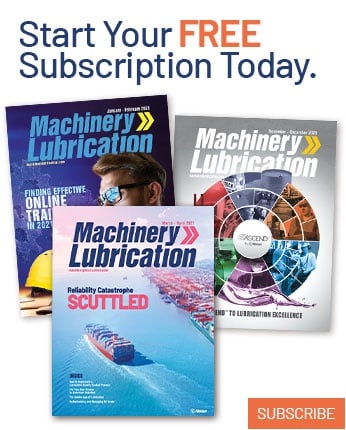