Enterprise resources planning (ERP) software is designed to perform a broad spectrum of functions right out of the box. Other functions can be achieved through modifications to the code, which can be expensive and cause problems down the road during software upgrades. However, managers at FEV Inc. have found that an ERP program can also be used in innovative ways to achieve organizational goals.
FEV is a privately owned, independent engineering services company working in the automotive, marine, heavy-duty trucking, commercial vehicle, large engine (locomotive, stationary power) and government-sponsored research markets. The company designs and develops powertrain and vehicle solutions for a global complement of customers through its technical centers in Aachen, Germany; Detroit, Mich.; and Dalian, China, in addition to many other engineering support offices around the world. These locations house design, testing and other equipment that are billable assets.
This article relates how FEV’s North American facility adapted functionality already deployed in the company’s IFS Applications to perform functions that were not part of the company’s original implementation – specifically equipment time tracking. Rather than making costly expenditures on additional functionality or modifications, FEV’s management leveraged the tools they had already implemented, and in a three-month time period were up and running on a new automated process for equipment time tracking.
Equipment time tracking is a critical function for FEV due to the company’s business model. FEV calculates a unit price for each piece of equipment, tracks time during which the equipment is used, enters comments on each job and ties that billable equipment time to projects being completed on behalf of customers. For each shift, FEV also tracks asset utilization within three classes: runtime, fabrication time and downtime.
Previously a manual process
Although FEV had been running IFS Applications as its enterprise application since 1999, the company had not yet implemented automated functionality for equipment time tracking. The company’s management wished to avoid changes to the existing instance of IFS or to modify the code because an upgrade to a new version was planned in the near term. The manual process for equipment time tracking required FEV technicians to fill out a daily paper log reflecting how equipment was used during the hours of their shift, including comments and project numbers. Then this information was entered in a monthly log in Microsoft Excel for review by management. Later, it was sent to accounting, which would sort the data by project numbers in order to complete project logs. Accounting would also track downtime entries and items required under ISO 9001-2000 and ISO 14001 quality standards. The accounting department would then need to compute the runtime totals for pieces of equipment used in billable work and enter those totals into IFS.
The work involved in equipment time tracking consumed approximately 36 hours of staff time each month, and information necessarily passed through several different spreadsheets and departments in the process. In addition to being manual and time-consuming, this process used created opportunities for mistakes as hand-written entries were entered into Excel.
The manual process also delayed the time at which FEV’s engineering department could determine how much time was being charged against each project.
The management team established process priorities to be: reporting key elements of equipment use on projects to facilitate project management and billing, and to follow procedures required under ISO. At the same time, FEV managers wanted to reduce the time required by various people who touched this data and reduce manual interactions with the information that created the opportunity for mistakes.
Automating the process
FEV’s management recognized that this project represented more of a business process upgrade than an information technology (IT) project, and planned accordingly. They assembled a multi-departmental team to assure that the various stakeholders could provide input necessary for its success and take ownership of the solution.
The team leveraged the existing IFS functionality by setting up each piece of equipment as an “employee” in IFS. A billable rate was assigned to each piece of equipment, and during each shift a technician logs into IFS as that piece of equipment and inputs runtime hours, fabrication hours, downtime hours and their own initials. The technicians can also add any other comments they feel are relevant.
At the end of each shift, managers can pull time tracking data from Crystal Reports to decipher the comments and summarize the tracking numbers.
Figure 1: In the IFS time registration screen, a technician is logged in as an employee using a specific piece of equipment. The hours billed to the customer are shown, as are the initials of technician. Other codes, such as Fab = 2, indicate the fabrication hours to set up the equipment or facility. Shift number is also indicated by listing s=1, s=2, etc. This allows analysis by shift of the issues encountered.
While the pre-IFS process for equipment time tracking required multiple levels of manual entry in a number of spreadsheets, FEV’s workaround solution requires only one input process. In order to allow for later division of equipment time by fabrication/setup, runtime and downtime, technicians enter codes along with a number of hours for each function (see Figure 1).
When analyzing these data, managers can determine that, of those 12 hours, only two hours were fabrication time, thereby defining the remainder to be actual runtime. In undertaking this project, FEV also made a special effort to track “downtime” that can not be billed to a customer, and the project team was keenly interested in modally analyzing reasons for downtime. In some cases, downtime is facility or equipment related, or occurs because necessary staff is not available to operate the equipment (see Figure 2). In other cases, downtime occurs because the customer is late in delivering test hardware or software or because technicians are waiting for results from another program.
Figure 2: FEV developed a parallel project specifically to track downtime that is not billable to a customer.
This system facilitates engineering project management by easily tracking progress in the test cell. The tracking screen (see Figure 3) indicates the quantity of runtime and fabrication time hours. This information can be used by various managers during the month to see how much facility or equipment cost will be charged to their project.
All the elements entered in the IFS system are then brought together in a custom Crystal Report which allows the managers to see the total reported runtime, fabrication time and downtime. They can also see the trends related to the facility or equipment, and gauge how their revenues or costs will be impacted at the end of the month.
Figure 3: Technicians input information on fabrication, runtime and downtime using a series of initials and numerals.
This project has been deemed a success for FEV because not only does the new system make information much easier to access, thereby allowing more effective project management, but because data is entered directly into IFS Applications, FEV has achieved a significant time savings in terms of reducing the man-hours necessary to manage equipment time tracking. Training of staff on this process change was minimal because FEV leveraged the capability of a familiar, in-house system to accomplish these goals rather than implementing new software or tools which would have been more costly and more training-intensive for the technicians.
Critical success factors
To ensure that the new system functions as required, it was necessary to guarantee that IFS Applications would be available at all times (24/7). Since FEV conducts a three-shift operation, technicians needed the ability to input data around the clock. FEV also had to train its technicians in the proper method and syntax for entering codes regarding equipment operation.
To minimize errors, convenient, logical codes were developed for data input. For instance, f=4 represents four hours of fabrication. Potential input errors, such as mistyping the codes or entering spaces between the characters, would create problems for the background code that deciphers the input data. FEV found that its technicians had no difficulty learning this data entry system, and additional measures were put in place to help alert the manager if a mistake was made.
In addition, the project team needed to make sure that projects were set up properly and that test cell codes for each project were made available to technicians before work began. To ensure that this information was made available on a timely basis, FEV created a test cell team within the Project Access module and granted the team access to all projects across the company. This guaranteed that all technicians logged in as equipment were able to access all projects within the company for time registration.
Overall, FEV’s automation of equipment time tracking delivered extremely positive results. The benefits greatly exceeded the financial and human capital invested primarily because the project team leveraged a system that was already being used and, therefore, didn’t incur the expense for software modification or the need to license any additional software.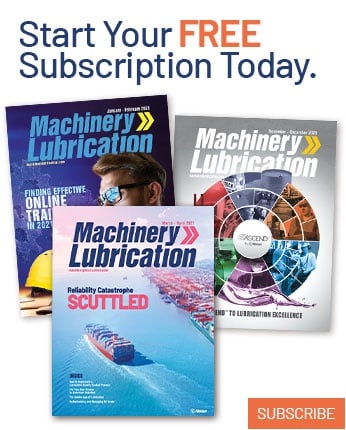