Ron Wroblewski is a DOE Energy Expert who is proficient in optimizing industrial fan systems and who regularly conducts Save Energy Now energy assessments to help companies pinpoint ways to save energy and costs. In this article, Ron addresses some common questions about efficiency and operational costs of fan systems.
Question: How can I tell if I have an inefficient fan?
Ron’s answer: It's not always obvious when a fan system is running inefficiently. Look at the system closely and understand the needs of the process to determine if inefficiency is an issue.
Indicators of fan system inefficiency usually fall into one of three categories: control, production/maintenance, or system effect. Use indicators to qualitatively select the systems that will benefit most from optimization projects.
Control indicators relate to the use of dampers to restrict flow and include:
- A motor that overloads unless a damper restricts flow
- Excess flow that is spilled or bypassed
- Use of a discharge damper, inlet damper, variable inlet vane or system damper
- A damper that is mostly closed.
Production and maintenance indicators signify wasted energy that causes equipment breakdowns and can include:
- Either too much or not enough flow or pressure for production
- A system that is unstable or hard to control
- Regular breakdowns
- Excessive noise, heat or vibration
- The need to weld ductwork cracks regularly.
System effect indicators point to problems with the design of the fan system that create excessive turbulence and instability. For example, abrupt turns can sometimes rob you of a significant portion of fan capacity. Some system effect indicators are:
- A 90-degree turn at or near the fan outlet or inlet
- A “dirt leg” at the bottom of the inlet duct, where the inlet duct is tapped into the side of a duct
- Lack of an outlet duct
- Restricted or sharp inlet.
If your facility has multiple fan systems with more than one of these indicators, use the Fan System Optimization Checklist (PDF 86 KB) to help you identify which systems are the best candidates for optimization. (Download Adobe Reader.)
Q: How can I determine what it’s costing me to operate my fans?
A: Fan systems can consume a considerable amount of energy on an annual basis, making it important to estimate power usage and annual energy costs.
If you are planning a project to improve the efficiency of your fan system, estimate fan operating costs before you begin. This process, called baselining, lets you document the current system status, come up with accurate savings estimates and provide results to management after project completion.
1. The first step is to obtain accurate estimates of your system’s annual operating hours and the average cost of electricity from your utility company. To find your average electric rate, review the last 12 months of electric bills for your facility and choose one or two months that look typical. On the bill, look for two numbers:
- Total bill amount ($)
- Total energy used (kWh).
Divide the total bill by the total kilowatt-hours (kWh) to get the average electric rate for your facility:
Electric rate = Total bill/Energy used
This gives you the rate in dollars per kilowatt-hour ($/kWh). In most instances, the average electric rate is adequate to make an accurate estimate of operating costs.
2. Have a qualified electrician take measurements of the system, using one of the methods described below:
- The power meter method is very accurate at measuring power, but requires the use of an expensive meter and takes only a snapshot measurement.
- A recording power meter that can be left on the process for a week is the best way to monitor the power consumption so you can see any variation over time, and know exactly how long the equipment is run.
- The volt-ammeter method is widely used because the meters are less costly and readily available. Although based on actual measurements, it depends on an estimate of the motor power factor, thus introducing some uncertainty.
3. Calculate the operating costs using DOE’s Industrial Technologies Program Fan System Assessment Tool (FSAT) software or the following method. The equations below are used for the volt-ammeter method.
- Calculate electrical power drawn by the motor:
Where:
A word on power factor: If the motor is greater than 60 percent loaded, then it is probably fine to assume that the power factor is 0.8; however, if the motor is very lightly loaded, then the power factor can be much lower.
- Calculate annual energy use:
- Calculate annual energy cost:
For example, for a 125-horsepower combustion air fan that uses an average current of 107.3 amps, operates at an average voltage of 461 volts and runs 8,760 hours/year at a facility where the electric rate is 0.05 $/kWh, the calculations would be:
For the electrical power drawn by the motor:
For the annual energy use:
And, for the annual energy cost:
These steps are used by FSAT to estimate baseline energy usage. Instead of the equations above, you could use FSAT to baseline operating costs; FSAT also includes a very good method to estimate power factor based on motor loading.
If the fan is operating with a damper that is mostly closed, you can also calculate the cost of the pressure drop across the damper. This is done by determining the ratio of the drop across the damper to the pressure rise across the fan, which shows you how much of the system’s energy is actually feeding the damper.
Baselining can also be performed on pumps, motors and compressors. Use this technique to identify the major energy users among your systems. This allows you to prioritize the systems for project work to increase efficiency. To learn more about baselining your fan systems or the effects of dampers, attend DOE's Industrial Technologies Program Fan Systems Assessment training session.
Additional Resources
For more information on how to improve your plant's fan system efficiency, see the following ITP resources.
- Fan System Assessment Tool (FSAT)
- Technical tip sheets and briefs
- Improving Fan System Performance: A Sourcebook for Industry (PDF 1.2 MB) Download Adobe Reader.
- Fan System Assessment training.
About Ron Wroblewski:
Ronald G. Wroblewski, P.E., has more than 25 years of engineering experience helping customers design, analyze, specify, and optimize commercial and industrial energy systems. In addition to earning both bachelors and masters degrees in mechanical engineering, Ron is a highly rated trainer who applies proven principles of adult education to make his technical seminars beneficial and fun. He is a senior U.S. Department of Energy fan systems instructor, and also provides industrial energy efficiency training for the United Nations. You can contact him at Ron@ProductiveEnergy.com.
Read More Energy Matters Articles on These Topics
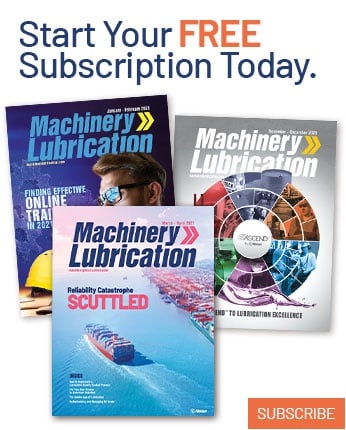