The manufacturing of cement is an energy-intensive process, consuming energy at every stage of production. The industry as a whole has been operating at less than 40 percent thermal efficiency, which indicates that there are significant opportunities to improve energy efficiency and reduce emissions.
Today, some companies are taking advantage of those opportunities to reduce the impact of their operations on the environment. CEMEX is one of those companies, and is committed to mixing sustainable business practices with profitability. To help achieve this goal, CEMEX is collaborating with DOE’s Industrial Technologies Program (ITP) to improve energy efficiency at several of its U.S. cement plants.
CEMEX’s Davenport, Calif., plant strives for sustainable operations
The partnership between CEMEX, one of the world’s largest cement producers, and ITP is already producing energy savings in several of the company’s plants. These savings result from upgrading inefficient electric motors and improving the efficiency of motor-driven pumps, fans and compressed air systems.
For instance, staff at CEMEX’s Davenport, Calif., cement plant used DOE’s MotorMaster+ software tool to evaluate motor inefficiency; they found that 13 of the plant’s electric motors required upgrading. These upgrades are saving the company $168,000 in annual energy costs while increasing reliability and production. What’s more, CEMEX is actively participating in several Industrial Technologies Program (ITP) Save Energy Now energy assessments, bolstering its commitment to sustainable and environmentally responsible manufacturing while improving the bottom line.
Blending Productivity with Sustainable Manufacturing
CEMEX – which is headquartered in Monterrey, Mexico – is one of the world’s leading providers of cement, ready-mix and aggregate products. It operates in 50 countries and has 14 cement plants in the United States. CEMEX produces more than 96 million metric tons of cement, 80 million cubic meters of ready-mix concrete and 222 million metric tons of aggregates each year.
With such large operations, meeting energy-efficiency and emissions-reduction challenges while remaining globally competitive are top priorities. To address these challenges proactively, CEMEX helped found the Cement Sustainability Initiative (CSI), a consortium of cement industry leaders. CSI works to reduce CO2 emissions, restore quarries, manage waste, ensure the safety of workers, and minimize operational impacts both to the local community and the global environment.
Cement manufacturing generates 5 percent of global CO2 emissions, and reducing this impact is of paramount concern. Each of CEMEX’s plants are monitored online by the CO2 Emissions Inventory Electronic Platform, which provides data to help develop strategies to increase efficiency. Other efforts include substituting alternative raw materials, increasing the use of biomass and other alternative fuels in pyroprocessing, improving energy efficiency, and using renewable energy sources such as wind energy.
CEMEX also takes action to rehabilitate the land around its operations. By the end of 2007, 94 percent of its active cement sites had quarry restoration plans in place. In addition, the company recently signed a 10-year agreement with BirdLife International, committing to the conservation of ecosystems on its operation sites around the world.
Shining a Spotlight on Energy Savings and the Environment
The CEMEX plant in Davenport strives for sustainable operation, both in its energy-efficiency efforts and in its care of the surrounding environment. These include developing an energy management program that tracks energy usage, working jointly with the local utility company to reduce consumption in times of high demand, and partnering with ITP to identify energy savings opportunities.
In 2004, plant personnel at the CEMEX Davenport facility used the MotorMaster+ software tool to evaluate the efficiency of motors on cement blowers and silo pumps. Before the evaluation, the plant experienced regular motor shutdowns that interrupted production and increased maintenance costs. Thirteen worn motors were replaced with high-efficiency ones, resulting in annual energy cost savings of $168,000, annual electricity savings of 2.1 million kilowatt-hours (kWh), and maintenance cost reductions of $30,000 per year. Learn more about the project in the Performance Spotlight (PDF 220 KB). Download Adobe Reader.
In addition to improving energy efficiency, the Davenport plant actively practices environmental stewardship. This includes reclaiming more than 26,000 tons of cement dust per year from an existing cement kiln dust landfill; collecting and recycling wastewater from a nearby sanitary treatment system; and establishing a land stewardship program on its 9,000-acre forest land. For these achievements, the plant was recently awarded the Overall Environmental Excellence Award at the Portland Cement Association and Cement Americas magazine’s 2008 Environment and Energy Awards – the highest honor among cement manufacturing facilities in the United States and Canada. The Davenport plant also received the Land Stewardship Award for the second consecutive year.
Collaborating to Save Energy Now and Tomorrow
To identify near-, medium- and long-term energy saving opportunities, CEMEX is partnering with ITP in the Save Energy Now initiative by conducting energy assessments at several of its U.S. plants. So far, six assessments have been conducted, identifying ways to increase efficiency in pump, fan, process heating and compressed air systems. Additional energy assessments are scheduled for the coming year.
“DOE’s energy assessments allowed us to uncover substantial opportunities for additional energy savings on specific systems at various CEMEX facilities across the U.S.,” said Bhaskar Dusi, CEMEX USA corporate technical energy manager. “Thanks to DOE, we are able to build on our past progress and move quickly to implement ideas for improved energy efficiency. The program validated the merits of some projects we had previously identified, and provided access to some valuable software-based tools that were useful in evaluating energy improvements.”
Learn more about the CEMEX energy assessments on the Save Energy Now participating plants Web site.
CEMEX is committed to reducing energy use and minimize its environmental footprint through sustainable business practices. The partnership between CEMEX and ITP links a company with a strong corporate energy management program with sound resources to help it achieve greater energy savings and reduce environmental impacts.
This article appeared in the Summer 2008 issue of Energy Matters, produced by the U.S. Department of Energy. For more information, visit www.eere.energy.gov/industry.
Read More Energy Matters Articles on These Topics
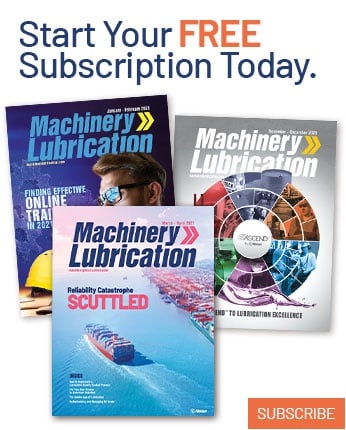