Lambeau Field benefits from building automation system interface
The Green Bay Packers have fans worldwide and are one of the most popular football teams in the National Football League. The organization was originally founded in 1919. The team moved into new City Stadium in 1957, renamed Lambeau Field in 1965, upon the death of Curly Lambeau, and used the stadium primarily for football games, about 10 times per year. The Packers took on a 32-month, $295 million stadium renovation, completed in 2003. In order for all fans to enjoy Lambeau Field, it was clear that the stadium needed to become a year-round venue.
The challenge that the Packers faced with the renovation of Lambeau Field was to improve efficiency and manage the stadium’s additional equipment. It was crucial that no equipment was overlooked for both preventive and demand maintenance.
Initially, the building management purchased a Metasys system from Johnson Controls Inc. (JCI) to manage their HVAC and building efficiency. At the time, Lambeau Field tracked approximately 45 work orders per month. Recognizing a need for a computerized maintenance management system (CMMS), the Packers looked to JCI, headquartered in Milwaukee, for a recommendation of suppliers. JCI looked no further than Eagle Technology Inc. Eagle Technology’s ProTeus software solution was exactly what the Packers needed for peak efficiency because of its seamless interface to the Metasys system.
The Packers first purchased the ProTeus software solution in 2003. Currently, the Packers use Eagle Technology’s ProTeus Enterprise system in conjunction with Metasys. Additional modules that adapt to fit the Packers’ needs are ProLink, a Web-based Service Request, Preventive Maintenance (PM) Task module, and Crystal Reports. The Packers have also elected to purchase Premium Care Support, which provides unlimited support via telephone, e-mail, and Web, as well as any major upgrades or patches for the product, at no additional charge, for the duration of their contract with Eagle Technology.
Anne Krueger, administrative assistant in the facilities department at Lambeau Field, stated, “ProTeus works very well to fit our needs. Not only is ProTeus easy to use, but the staff is great to work with, especially in Support.”
Krueger’s first introduction to ProTeus was training at Eagle Technology’s headquarters in Mequon, Wis. Krueger spoke of her experience with training.
“The implementation and training of ProTeus was simple and full of detailed information,” she said. “It was fantastic to have the background information. The training was everything we needed to get the product up and running at Lambeau.”
Krueger also visited the City of Milwaukee, another client of Eagle Technology, to see first-hand how they successfully implemented their ProTeus system and how it was functioning.
ProLink, a Web-based Service Request, is one module in the ProTeus system that has helped out tremendously. It saves Krueger a lot of time because it is so easy to use. All Lambeau Field employees can access ProLink on the company’s intranet. A major outside contractor, Levy Restaurants, also uses ProLink. As the administrator for ProLink, Krueger likes the fact that “the system is easy to use and is more efficient than requests via phone and e-mail. Information is entered into the system and the requests can be modified in case of an additional maintenance need for a particular piece of equipment.”
The results
There have been numerous benefits that Krueger has realized since the implementation of ProTeus. ProTeus has been completely up and running at Lambeau Field for a little more than a year. No stone gets unturned in ProTeus. The data is well organized, and with more than 120 reports, there is one to fit any situation. Topics include Equipment, Labor, Inventory, Demand Maintenance (DM) and Preventive Maintenance (PM), Vendor, Purchasing, and Customers, as well as other management reports. When Lambeau Field first started reporting on their work orders, they averaged 75 PM and 225 DM work orders per month. The average number of work orders per month in 2007 was 137 PM and 158 DM work orders.
One feature of ProTeus that particularly helps out Krueger is the Multi-Cycle Scheduler. It displays current, overdue and upcoming PM and DM work orders in both calendar and tree-view formats. The Scheduling function allows for a better picture of what maintenance is coming up in the future. It enables the user to reassign labor, reschedule work orders, skip active work orders and more.
Krueger commented on the Metasys interface, stating, “Through the interface, work orders are able to be automatically generated based on the alarms in Metasys. This saves a lot of time because I will not have to create a separate document with the information I need. It is already there for me to give to our technicians. At this point, Metasys sends alarm messages directly to the technician’s pager, but we look forward to taking advantage of this time-saving interface in the future.”
Future goals
Krueger emphasizes that the biggest goal is staying current with all information, both preventive and demand maintenance, on every piece of equipment within the stadium. Lambeau Field is the only sports facility to be sold out for decades, so it is imperative that all equipment is managed properly and working at peak efficiency. Eagle Technology is proud to provide ProTeus in order to continuously improve that effort.
About the Green Bay Packers
Additional information about the Green Bay Packers and Lambeau Field can be found on the Web at www.Packers.com or www.LambeauField.com.
About Eagle Technology
Additional information on Eagle Technology Inc. and ProTeus can be found on the Web at www.EagleCMMS.com or by calling 800-388-3268.
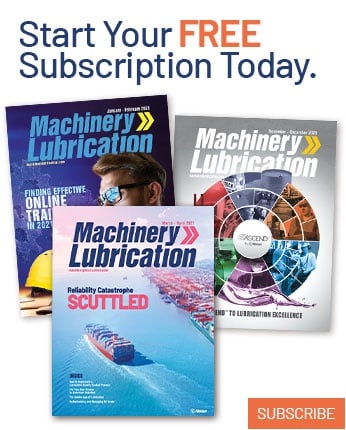