Titanium, a protean element with applications from pigments to aerospace alloys, could get a new role as an environmentally friendly additive for automotive oil, thanks to work by materials scientists from Afton Chemical Corporation (Richmond, Va.) and the National Institute of Standards and Technology (NIST). In a recent paper,* the researchers established that a titanium compound added to engine oil creates a wear-resistant nanoscale layer bound to the surface of vulnerable engine parts, making it a credible substitute for older compounds that do not coexist well with antipollution equipment.
Modern engine lubricating oil is a complex, highly engineered mixture, up to 20 percent of which may be special additives to enhance properties such as viscosity and stability and to reduce sludge formation and engine wear, according to Afton specialists. For years antiwear additives for high-performance oils have been phosphorous compounds, particularly ZDDP,** that work by forming a polyphosphate film on engine parts that reduces wear. Unfortunately phosphorus is a chemical poison for automobile catalytic converters, reducing their effectiveness and life span, so industry chemists have been searching for ways to replace or reduce the use of ZDDP. It’s not a simple problem because the additive has several useful functions in addition to wear resistance.
Titanium is one candidate replacement. Mechanical tests of an organic titanium compound at Afton demonstrated that it provided superior wear resistance when added to a fully formulated engine oil, suggesting that oil chemists could use less ZDDP. Just how the titanium compound works was an open question, however. Surface analysis tests could detect titanium in the wear tracks of test surfaces but not with enough sensitivity to determine its chemical nature – and whether, for example, it was just lying there or bound to the metal surface. To resolve the issue, the researchers turned to NIST’s soft X-ray beamline at the National Synchrotron Light Source (NSLS) in Brookhaven, N.Y.
The NIST beamline instruments use low-energy (“soft”) X-rays that can be precisely tuned to specific elements to measure chemical bonds both at the surface of a sample and deeper into the bulk of the material. Powered by the NSLS, the facility is at least 10 times more sensitive than commonly available instruments. The measurements revealed that the antiwear enhancement comes from titanium chemically bound into the metal structure of the engine surface, forming a hard oxide, iron titanate. Comparing the test data to that of several possible compounds, the research team was able to identify the specific oxide. While considerably more work remains to be done, the results suggest that titanium could play an important role in future low-phosphorus lubricating oils.
* J.M. Guevremont, G.H. Guinther, D. Szemenyei, M.T. Devlin, T.-C. Jao, C. Jaye, J. Woicik and D.A. Fischer. Enhancement of engine oil wear and friction control performance through titanium additive chemistry. Tribology Transactions, Volume 51, 324-331, 2008.
** zinc dialkyldithiophosphate
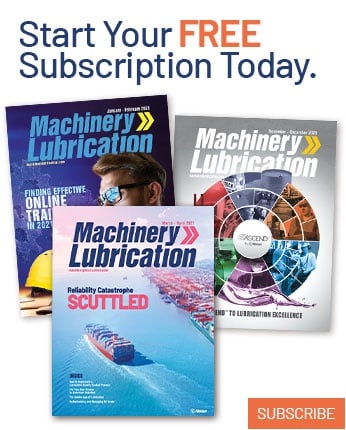