Thanks to its global lean initiatives, Kennametal boasted substantial savings in all divisions in 2007. As a systematic process, lean thinking is an integral part of the Kennametal Value Business System (KVBS) and, consequently, of the corporate strategy.
The specific lean tools to be applied depend on the task at hand, and each is designed to filter out the processes that generate added value for the customers and have potential for improvement. Thus, wasteful or inefficient processes are systematically spotted and eliminated. The lean process shall increase productivity and offer savings in materials, expenses and other resources. Lean tools are systematically applied in special projects and integrated into the routine work processes of all employees.
Regular training is offered to ensure awareness, application and integration of lean thinking throughout Kennametal, and all managers are encouraged to attend a special Lean Management Training. This provides the organization with the necessary skills and knowledge of the tools so all teams can pursue continuous improvements and avoid waste. In the end, the customers will benefit from faster processes and better service. Almost all European locations employ a staff member full-time as lean coordinator to coordinate all lean initiatives on site. This is ample proof that the lean process is not merely a paper strategy at Kennametal, but rather very much alive in all production and administrative units.
Since the program's inception, more than 120 employees have become certified as green belts in Europe, indicating the qualification level they have achieved within the lean process. To avoid the initiation of projects just for the sake of having a project, all ideas are scrutinized in regular, local or cross-functional reviews and steering council meetings. The decisive point always is the generation of added value or the elimination of waste. Success is documented after the project's completion as basis for the identification of further process improvements.
The Kennametal production facility Vohenstrauss/Germany implemented a best practice project for customer service last year. The plant frequently had to struggle with capacity bottlenecks in production due to stronger customer demand for the KenTip product. Cycle time had to be significantly reduced to shorten production times and, thus, increase the production output with the resources available. A team was formed that applied lean tools and succeeded in increasing productivity by 15 percent within half a year; and getting better still. Product availability even went up by 50 percent during the reporting period due to continuous improvements. The project team's ideas were integrated into a new standard process for all production operations and put into practice. Both the work processes for the KenTip production and the collaboration of the different departments are now controlled by an optimized process schedule, which was ultimately decisive for the impressive result to the customers' benefit.
Peter Bird, Kennametal’s lean manager for Europe, is convinced that the company’s global, customer-oriented lean culture is a permanent incentive for the workforce to observe their own work processes attentively, thus uncovering improvement potential.
"A great number of lean projects have already been defined for next year,” says Bird. "We are, therefore, quite close to our target of turning ineffective processes into productive ones."
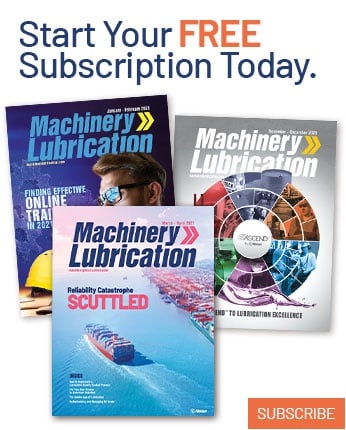