Reliable Plant editor Paul V. Arnold recently interviewed Wes Scott, the National Safety Council’s manager of occupational safety and health consulting services. Here are the questions and answers from that chat.
Question: Recent data provided by the Department of Labor’s Bureau of Labor Statistics points to some solid improvements for manufacturing companies in the area of safety. Non-fatal occupational injuries and illnesses declined for the fourth consecutive year in the most recent BLS report (a 4.1 percent improvement). Non-fatal cases requiring days away from work fell by 3.4 percent. Is everything as rosy as it appears for safety in U.S. manufacturing plants?
Answer: As the data shows, worker safety is certainly improving in today’s manufacturing plants. That doesn’t mean the job is done. Any preventable injury or fatality is one too many. While the overall trend is good, there are areas where the results are the opposite. For example, with Hispanic workers, we see rising injury and fatality rates. We also are seeing more workers injured off the job than on the job. Regardless of where they occur, injuries and fatalities are tragic and, beyond the personal loss, they represent a loss to a business.
Q: What have been some of the keys to the statistical improvements in manufacturing industry safety in recent years?
A: Studies show that training makes a difference. The more that safe practices become the everyday routine, the better prepared any employee is to face risks encountered in their workplace. Beyond training, deploying best practices for safety and health throughout the workplace makes a difference. The prevention -through-design approach, whereby safety is engineered into the processes, machinery and environment, makes a difference because it eliminates the risk. Recognizing its potential to protect workers, the National Institute for Occupational Safety and Health (NIOSH) launched a national initiative in March on safety through design.
Q: In the opinion of the National Safety Council, what are the biggest areas of opportunity for U.S. manufacturing plants in the area of safety?
A: As fatality and injury rates continue their downward trend, we are seeing increased production demands in many manufacturing environments. As one would expect, we are at risk from ergonomics-related injuries created by the demands of the job tasks. Since the late 1980s, crushing, cutting and other acutely traumatic injuries are declining, while at the same time, the chronic musculoskeletal injuries, such as strains and sprains, are increasing with the aging workforce. To combat these cumulatively traumatic injury causes, the focus for prevention is shifting from machine guarding to substituting mechanical lifting equipment, employee education and other behavior-modification techniques.
Employees now work far longer into their tenure than they did a mere 10 years ago. According to a survey conducted by the National Council on Compensation Insurance, even though older workers may not suffer injuries more frequently, they do experience higher costs per claim. When a young worker falls, he may walk away with a bruise. An older worker taking the same spill may encounter a broken hip. Raising employee awareness through training and addressing key behaviors is paramount in minimizing the affects of these challenges.
Q: Companies like to use slogans such as “Safety is our No. 1 priority” and “Everything starts with safety”. However in some plants, the push toward a safe work environment never makes it out of slogan mode. What can plant workers do to help their sites become more action-oriented when it comes to safety?
A: To drive preventable injury and fatality rates down requires more than just a campaign. Companies that never go beyond the campaign mode are likely to have higher rates of injury, or may just be lucky. Corporations that understand the ROI gained from a healthy and safe workforce embed safety into their corporate culture. In a safe culture, the C-suite and even the board assess the company’s safety and health performance or track record with the aim of making decisions that help to keep employees safe and healthy. A culture of safety permeates all levels of a plant and makes everyone responsible. Workers can begin by keeping their area free of hazards, following safe practices and modeling safe behaviors, and correcting unsafe or unhealthy practices of their co-workers without retribution.
Q: Please talk about June’s designation as National Safety Month and explain how a manufacturer can utilize the month’s tools and activities to gain momentum and a renewed focus on plant safety?
A: National Safety Month brings attention to where the preventable injuries and fatalities occur and what can be done to keep people healthy and alive at work, on the road, and in their home and community. Plants can use the tools to focus on awareness campaigns and solutions that are most relevant to their workforce. For example, a plant with low injuries and no fatalities can seek employee buy-in to apply the same safe practices they use in their workplace in their homes and help prevent falls for themselves, their family and friends. Or, it can bring attention to the injuries and deaths caused by distracted driving, a topic relevant to all employees. The first week of National Safety Month centers on preparedness for emergencies where CPR and AED skills are essential for survival. Plants can assess their level of preparedness, run drills and launch basic training for all employees. Increased attention on safety and help can pay rewards for individuals and companies.
To learn more about the National Safety Council or National Safety Month, visit the NSC Web site at www.nsc.org.
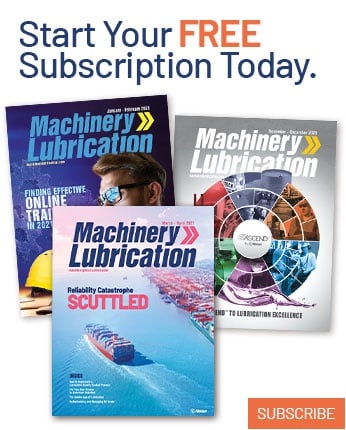