When reporting verbally or in writing on the results of an accident investigation, it's tempting to sum up the cause as "carelessness." This indicates that the accident probably could have been avoided if someone hadn't done – or failed to do – something. But it doesn't really help in pinpointing the real cause, let alone correcting whatever behavior was involved, in order to prevent recurrence.
If an individual's "careless" behavior was at the root of the incident, it probably means that the person did not:
THINK
Comply with safety regulations
Follow instructions (written or verbal)
Use safe work procedures
Use sound judgment
Know how to do the work properly
Pay full attention to the work
Wear proper personal protective clothing and/or equipment
Use tools or equipment in a safe manner
THINK!
So, if your input is ever sought as to the cause of a particular accident, find a better term than "carelessness." You'll probably find it on the foregoing list. Remember, the more exact you can be, the more likely we can avoid a repetition.
Employee incident reporting
An incident is similar to an accident except that it does not necessarily result in injury or damage. No matter how trivial they are, incidents should be reported to supervision just as accidents are. Employees should be encouraged and periodically reminded about the importance of reporting incidents, or as they are frequently called, near-misses. Consider this article just such a reminder.
Why incidents should be reported
Nothing is learned from unreported incidents. Hazards, causes and contributing circumstances are lost if not reported. Employees who don't take the time to report near-misses they are involved in may not learn from them. The fact that many incidents come within inches of being disabling injury accidents makes failing to report them all the more serious. When incidents are not reported, their causes usually go uncorrected. That means they may happen again, perhaps producing tomorrow's disabling injury or fatality.
This can be illustrated by the case of the worker who slipped on a floor made slippery by a small leak in a hydraulic line. He did not suffer any injury. Two days later, when the line was still leaking, another employee slipped on the liquid, fell, and broke her leg. At that point, the first employee told the company investigating the accident about his own previous near-miss. Had he reported it promptly, chances are the defective hydraulic line would have been repaired before the accident happened.
Why incidents often are not reported
There are many reasons why a worker might choose not to report an incident in which he or she was involved. All of these are understandable, but we should recognize that none of them are acceptable when we realize why the report should have been made.
What are some of the reasons workers don't report incidents? Probably the most common is failure to understand the importance of reporting and the harm that could result by not doing so. Here are some others that we've heard about:
Fear of the supervisor's disapproval.
Not wanting the incident on their work records.
Dislike for the red tape involved.
Not wanting to lose time from the job on piecework assignments.
Reluctance to spoil the unit's safety record.
Not wanting to be the subject of an incident investigation.
What can be learned from an incident?
The whole purpose of reporting and investigating a near-miss incident is to find ways of making sure the same elements that were present on that occasion don't result in an accident at some future time. So here are some of the questions to which answers must be sought:
- What were the circumstances surrounding the near miss? Was there a hazard that the employee should have been aware of?
- Is there a safety rule covering the situation? If so, did the almost-victim know it? If there isn't such a rule, should there be one?
- Were any safety devices, clothing or equipment used improperly or not used at all when they were called for?
- Have there been other near-misses of the same type?
The answers should suggest ways to prevent a recurrence. Perhaps there need to be new rules or procedures developed. Or, maybe more thorough training is required. In any case, the reporting of the incident is the vital first step.
Almost an accident: Be warned
How many times have you come close to having an accident, shrugged it off as a near-miss, and gone on your merry way without giving it another thought? Give it thought. Many times, the difference between a near-miss and an accident is just a fraction of a second in timing or a fraction of an inch in distance. Next time, the difference may not be there.
Near-misses are warnings of accidents in the making. If we accept the warnings and look for the causes, we may be able to prevent similar situations from developing. Let's say you're going up a gangplank onto a bridge footer. Your foot slips, but you're young, agile, fast, and empty-handed. So, you regain your balance with no harm done. The reactions of the next person to come along are a little slower than yours. Then comes the third worker, just as fast as the first two but unable to maneuver because he's carrying a heavy load. He slips and falls off the plank with the load on top of him. How seriously he's injured is a matter of luck – perhaps only scratches, but maybe a broken ankle or rib or neck. Now the loose cleat, sand, mud or ice is discovered, and the condition is corrected. But it's like locking the garage after the motorcycle is stolen. Two people saw the thief but didn't recognize what was happening, so didn't report anything.
There are a few accidents that occur without some advance warning, and that is what a near-miss is. If we heed that warning and check into the hazard, most accidents can be eliminated So, keep your eyes open for those advance warnings. Don't shrug off the near-misses as only close calls; find out why they happened and who can take corrective action.
Don't take unnecessary chances or ignore warnings, and don't think "it can't happen to me." It can happen to you if you don't take precautions to protect yourself.
About the author:
This article provided by TrainingOnline.com, an e-learning division of Business and Legal Reports Inc. and a publisher of quality compliance, training and productivity tools for the workplace. For more information on the company’s range of products and services, visit www.TrainingOnline.com.
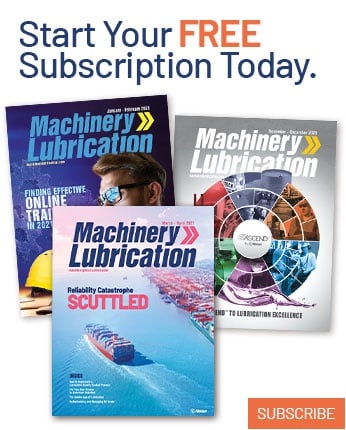