Since 2000, Ford's U.S. facilities have improved energy efficiency by 18 percent and reduced CO2 emissions by more than 15 percent. Actions leading to those reductions were among the reasons cited by the EPA in presenting the award, in the Energy Management category.
"Ford Motor Company believes a sustainable, profitable business requires responsible use of environmental and social resources," said Sue Cischke, vice president, environmental and safety engineering. "Our partnership with Energy Star has been instrumental in driving energy efficiency improvements."
"Buildings cause about 17 percent of U.S greenhouse gas emissions," said Kathleen Hogan, director of EPA's Climate Protection Partnerships Division. "Energy Star partners such as Ford are showing that their buildings can be effectively managed - with great results for their energy bills and our environment."
The most significant energy efficiency actions included installation of large-scale networked heating, ventilation and air conditioning systems, air compressor controls and energy-efficient production tooling. Data-driven processes and automated systems further drove efficiency improvements at manufacturing, corporate, and research and engineering facilities.
Ford is reducing its impact on the environment through implementation of technologies such as geothermal cooling, landfill gas reclamation, converting paint fumes to fuel, hydroelectricity, wind and solar technology to power manufacturing plants in clean, sustainable ways. In the U.S., renewable, or "green," power supplies 5 percent of Ford's energy needs.
As part of the Energy Star award selection process, the EPA recognized Ford for several key innovative programs:
Fumes-to-Fuel
Ford, in partnership with Detroit Edison, developed a fumes-to-fuel system that uses paint booth gases to generate electricity. The system captures paint booth fumes, a plant's largest source of CO2 emissions, and then uses them to produce electricity. A production-scale pilot project at Ford's Michigan Truck Plant represents the final test of the system before full-scale implementation by the end of the decade. Ford, in partnership with Detroit Edison, earned the EPA's 2004 Clean Air Award for developing this technology in partnership with Detroit Edison.
Geothermal Energy
The Lima (Ohio) Engine Plant uses cold water from two abandoned limestone quarries on the property to cool a portion of the plant and its equipment. The geothermal system saved Ford $300,000 in installation costs - compared with the cost of installing a traditional cooling tower - and saved more than $300,000 in annual operating costs. The system earned the 2005 State of Ohio Governor's Award for Excellence in Energy, and the Design-Build Institute of America's 2005 National Award.
Alternative Energy Sources
The Wayne (Mich.) Assembly Plant uses landfill gasses to heat and cool the facility, reducing the consumption of natural gas. The Ford Rouge Visitor Center in Dearborn, Mich., houses a photovoltaic array, a solar thermal collector and an automated building management system. The adjacent Dearborn Truck Plant holds the world's largest living roof that reduces solar thermal load while ground cover converts CO2 into oxygen.
The Partner of the Year Award is given to a variety of organizations to recognize their efforts to use energy efficiently in facility operations and to integrate energy efficiency into overall organizational strategy. Energy Star was introduced by the U.S. Environmental Protection Agency in 1992 as a voluntary market-based partnership to reduce greenhouse gas emissions through increased energy efficiency.
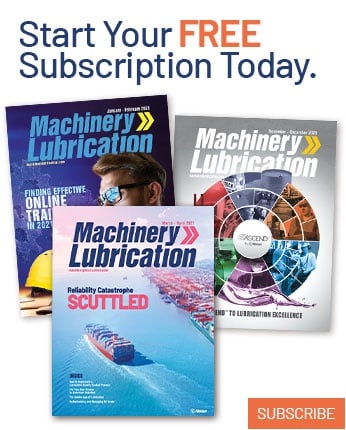