Mark Emkes, the chairman and chief executive officer of Bridgestone Americas Holding Inc. and the chairman and CEO of Bridgestone Firestone North American Tire, will provide the general session keynote address at Noria Corporation’s 2008 Lean, Reliable and Lubed conference and exhibition. The event will be held May 20-22 at the
In his May 20 keynote address, entitled “Where the Rubber Hits the Road: Innovation, Reliability and Lean as Viewed by Bridgestone’s CEO”, Mr. Emkes will explore how innovation, reliability and lean manufacturing are driving success and growth at Bridgestone. This exclusive keynote session will give you a first-hand look at this global leader in tire technology. Bridgestone is one of the most respected and dynamic companies in manufacturing today. Bridgestone Americas, based in
Mr. Emkes will provide an inside look into this industrial giant and outline the plant-floor initiatives that are positioning this well-known manufacturer for continued success. In this session, you will hear how Bridgestone pursues innovation, reliability and lean, and see why Mr. Emkes is a strong supporter of these and other plant initiatives.
This session kicks off three days of presentations focused on lean manufacturing implementation and optimization. For full information and to register for the event, visit www.driveyourplant.com.
Lean track keynote addresses include:
KEYNOTE: How Boeing Does Lean Maintenance
Mark Calkins, Seattle Site maintenance manager, The Boeing Company
Over the past three years, Boeing’s maintenance organization in
KEYNOTE: Process-Centered vs. Person-Centered Lean Leadership
Dr. Ross Robson, executive director, Shingo Prize
Ross Robson knows what makes a company lean and knows what it takes to get there. As the executive director of the Shingo Prize for Excellence in Manufacturing since 1989, he has participated in more than 100 comprehensive site evaluation visits to companies that have challenged for the prize. He has also edited and authored books and articles on the subject of lean. In this informative keynote session, Dr. Robson draws upon his decades’ worth of experience and tackles the subject of lean leadership. Leadership has frequently been identified as key to continuous improvement. However, traditional leadership theory and practice in the
KEYNOTE: The Confused State of
Dr. Richard Schonberger, president, Schonberger & Associates
Lean too easily goes into remission, burns out or never gets started. Dr. Schonberger’s “leanness” research (15 or more years of hard inventory-trend data from some 1,260 companies in 37 countries), backed up by company interviews, examines why — and explores what it takes to sustain a strong lean effort over the long term. Emergent are eye-opening, often out-of-the-mainstream answers. While the lean landscape is littered with weak and fallen companies, numerous others emerge as unsung “stars” of lean. Some of the best trends are in companies not notably proficient in the Toyota-based “lean core.” Rather, much of their leanness comes from: a) culling lesser, capacity-gobbling products, customers and suppliers; (b) simplified product design; and (c) facing up to the difficult, but higher potential issues residing in the logistics pipelines.
Pure Lean sub-track case studies and presentations include:
Gauging the success of LeanSigma
Michael Gerster, CEO, WIKA Instrument Corporation, and Joe Panebianco, senior management consultant, TBM
WIKA Instrument Corporation has earned its industry reputation and business growth by combining world-class LeanSigma operations and agile manufacturing. This company is using various lean tools and applications to improve the flexibility, productivity and reliability of their plants.
Lean Is More Than Tools
Joseph P. Ziskovsky, director of operational excellence, Johnson Screens, a Weatherford International company
Lean is a management system, not just a bunch of tools. There are some that even call it a religion, a culture or a way of thinking. It is all of these and more. It has to do with commitment to improvement, seeing value, seeing the processes that exist in any operation. This goes for not only manufacturing but services, healthcare, government and even education. Everything consists of processes. Every process has components, some value added some not value added (wastes). Seeing waste is integral to finding improvements. Implementing improvements has to be a daily activity in a true lean environment. Tools are involved, but it is the proper management of those tools that makes lean sustainable.
Reliability and Lean Six Sigma
Lynn D. Nelson, Six Sigma master black belt, Rio Tinto/Kennecott Utah Copper
In today’s fast-paced business world, companies are constantly looking for ways to improve. Successful business improvement initiatives must include programs that identify system constraints, reduce variation, improve equipment reliability, and continuously improve the business performance and culture. Theory of constraints, Six Sigma and lean are just such programs. This presentation will discuss the various improvement methodologies and illustrate how all are vital to continuous improvement and reliability.
Key Performance Indicators for Lean Manufacturing Excellence
Subramaniam Manivannan, quality coach/assessor, Ford Motor Company
Key performance indicators (KPI) help organizations achieve organizational goals through the definition and measurement of progress. The key indicators are agreed upon by an organization and are indicators which can be measured that will reflect success factors. The KPIs selected must reflect the organization’s goals, they must be key to its success, and they must be measurable. KPIs usually are long-term considerations for an organization. This session will focus on how to use KPIs to drive lean excellence and remove muda (waste) from the system. It will also help you select/create KPIs by using the Six Sigma DMAIC process.
Working with Machines: The Nuts and Bolts of Lean Operations with Jidoka
Michel Baudin, owner, Manufacturing Management & Technology Institute
The more manual a manufacturing process, the more severe the competitive handicap of high wages. Yet, full automation and “lights-out” factories remain impractical in most industries. Successful manufacturing in advanced economies is neither fully manual nor fully automatic. Instead, it involves interactions between small numbers of highly skilled people and machines that 1) account for the bulk of the manufacturing costs and 2) equalize the playing field by being no cheaper to competitors. This session is dedicated to the engineering and management of this type of factory, starting from the human interfaces of individual machines to the linking of machines into cells, the management of monuments and common services, autonomation, maintenance, and production control. The goal is for manufacturing managers and engineers, lean champions and others to leave this session with strategies and tools to make the technical and managerial decisions that turn working with machines into lasting business success.
“But We’re a Large Job-shop …” Transitioning to Lean Case Study
Mike Thelen, lean facilitator, Hub City Inc., a subsidiary of Regal-Beloit Corporation
A Framework to Guide Lean Contribution to Business Performance
Walter Tullis, lean implementation leader, Boeing Commercial Airplanes
This session will outline a practical framework for defining, aligning and deploying actions to strengthen lean maturity. This framework has been successful utilized by a production support group of Boeing. The key elements described are: Contribution Assessment: Voice of the customer and “win” performance targets; Production Analysis: Product/services variables and production system type; Lean Levers: Leadership, flow optimization, empowered teams, value stream flow, standard operations; continuous improvement and workplace culture; Lean Plan: Actions and deliverables, alignment-to-contribution targets; Deployment and Assessment: Project plans and lean assessment.
The Road to Continuous Improvement in a Manufacturing Environment
David McDonald, vice president of operations/supply chain, Therma Tru
In this session, you’ll learn the steps to running a successful manufacturing operation by utilizing lean principles and continuous improvement techniques. These include: how to set the stage, organizational techniques, lean strategy/execution, and how to move the organization forward to new heights. David McDonald has spent 26 years in various manufacturing operations with two Fortune 100 companies, with the last 18 years spent as a vice president of operations/supply chain in manufacturing operations ranging from $39 million to $600 million. The techniques elaborated on in this session are tried and proven techniques that deliver stellar results in order to drive competitiveness.
Just-In-Time Job Shop Production Management – A Wire Manufacturing Case Study
Jim Price, faculty principal, University of Kentucky Center for Manufacturing
This presentation will describe methods to reduce lead time and effectively manage just-in-time (JIT) work-in-process (WIP) flow through a job shop-oriented electrical cordwire manufacturing facility using the principles of
Lean Reliability sub-track case studies and presentations include:
Mini-workshop: Lean and the Downtime Life Cycle
Mike Verdin, principal, and Sue Gillman, co-founder, Aveus LLC
So where does the time go? You all experience it – the time between equipment down and productive use often seems much longer than the actual wrench time. Take home a different way to think about downtime by attending this mini-workshop that will provide you with an approach to analyze, describe and deal with the total downtime life cycle. The session will provide tangible takeaway methods for you to apply in your site and, thus, make a difference in your site’s performance. Explorations of downtime metrics and business aspects will also be provided.
Using Visual Controls to Support TPM
David James, autonomous maintenance/progressive maintenance resource, Clorox Corporation
This presentation will address the use of visual controls as a Total Productive Maintenance tool utilized in the plant environment. The speaker has responsibility for developing and standardizing the use of visual controls for Clorox plants across
Lean and Green: BMW Turns Landfill Gas to Plant Energy
Cleveland Beaufort, plant engineering section manager, BMW Manufacturing
Plant engineers keep the BMW Manufacturing site in Spartanburg, S.C., on the leadership path by coming up with innovative solutions to its needs. One amazing example has saved millions of dollars in energy costs. The plant, for the most part, runs on burned trash gas from a local landfill. BMW transforms methane gas produced from the nearby Palmetto Landfill into electricity and heat for the plant. It also utilizes landfill gas to fuel 23 oven burners in the paint shop and supply indirect heat to the area. This is lean and saves plenty of green.
Clean, Lean and Reliable: The New Standard for MRO Storerooms
Frank Murphy, founder, Inventory Management Services Inc.
Clean, lean and reliable MRO storerooms are essential for plants practicing or implementing lean manufacturing. Emerging or established preventive maintenance (PM), predictive maintenance (PDM), Total Productive Maintenance (TPM) or Reliability-Centered Maintenance (RCM) programs require a reliable parts storeroom to support their best maintenance practices. Having the right parts, at the right time, located and accessed efficiently and stored in minimum yet sufficient quantities are prerequisites needed to sustain successful maintenance operations. This presentation outlines how MRO storerooms become lean and reliable through the implementation and application of methodical, common-sense and practical part organizing methods and day-to-day storeroom operating procedures.
Creating a Culture to Drive Continuous Improvement Forever
Mike Wroblewski, lean sensei, Batesville Casket Company
For the past 25 years, the Batesville Casket Company has traveled down the path of Continuous Improvement. In this case study, you will learn about the challenges, practices and lessons, especially the relentless focus on the lean basics that enabled them to achieve year-over-year success on the never-ending lean journey. Batesville Casket has been nationally recognized for its success by winning three IndustryWeek Top 10 Plant Awards in the last four years. In addition, Batesville Casket plants have earned recent AME Manufacturing Excellence Awards, both regionally and nationally.
Whirlpool Puts a New Spin on Assembly Area
Matthew Herman, assembly process engineer, Whirlpool Corporation
This case study will demonstrate how a mature process was dramatically transformed to reduce non-value-added work, improve material flow and improve system reliability, all with minimal investment. It had been thought that a product line that was nearing 20 years of production had been perfected, and that all the low hanging fruit had already been taken. However, by taking a step approach, tremendous gains were realized in an area that was thought to have achieved full potential. Topics of discussion include: the conversion of an index and dwell main assembly line to run continuous, developing a new means for direct feeding subassemblies, and the methods used to improve reliability.
Hammering Home the Importance of Lean Implementation
Curtiss Quirin, director of operations, The Stanley Works
The Stanley Works, a worldwide producer of hand tools and security products, is transforming the company through the implementation of the Stanley Fulfillment System (SFS) as well as developing and implementing Continuous Improvement projects using Lean and Six Sigma methodologies. These tools are eliminating waste and inefficiency and driving the importance of value-added activities throughout organizations such as maintenance. This session hammers home the notion that lean done right means reliability done right. Its key points include: Lean Starts at the Top (leadership), Make it Visual (5-S), Make it Count (value stream mapping), and Make it Stick (constancy of purpose).
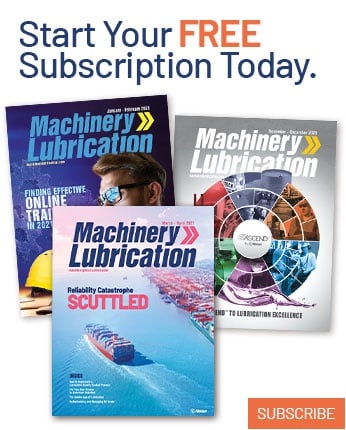