Photo Etch of Fort Worth, Texas, delivered sophisticated communication devices in a seemingly impossible timeframe, thanks in part to lean manufacturing processes promoted by the Supplier Excellence Alliance (SEA). The fulfillment of the $4 million contract further proves the value of lean techniques, as well as Photo Etch’s ability to quickly design and deliver high-quality, complex equipment for its manufacturing clients on demand.
In May 2007, Photo Etch was contacted by an electronics supplier that produces hardware and software for military and aerospace applications. The company needed to outsource production of 1,250 communication devices, which needed to be designed, tested and delivered in just nine months. In addition, the devices were required to pass stringent environmental and electromagnetic immunity standards, guaranteeing that they would operate under extreme electromagnetic, weather and environmental conditions.
“The difficulty of producing these high-tech communication devices under such stringent standards prompted our client to outsource,” said Randy Fry, chief executive officer of Photo Etch. “Despite our client’s sophistication, they simply did not feel comfortable taking on the project in-house.”
After accepting this challenging contract, Photo Etch immediately assigned an in-house team of 13 to design and test the devices, which they accomplished in just 11 weeks.
“Our client was shocked that we were ready to start manufacturing in October, less than five months after we won the contract,” Fry said. “At that point, we were well ahead of schedule.”
To ensure zero defects and on-time performance, Photo Etch’s engineering department solicited input from the supply chain, which resulted in a design that was truly manufacturable in a lean and Six Sigma environment. Then, for the assembly process, Photo Etch assigned four independent contractors to a dedicated work cell designed to support one-piece flow. The contractors were given thorough training and a set of visual work instructions to eliminate errors. The manufacturing work cell had a takt time of 20 minutes. Photo Etch then used an automated test documentation process with checks and balances to avoid duplication errors and ensure that each device met the client’s strict engineering requirements.
“With this high-speed project, Photo Etch has definitively proven the value of SEA’s lean manufacturing processes,” Fry said. “We leveraged these techniques to make these communication devices fast, make them right, and make them reliable. We look forward to taking on similar ‘impossible’ challenges for other manufacturing clients with fast-approaching deadlines and sophisticated products.”
Photo Etch joined SEA in August 2006 and became the first supplier in Texas to engage in SEA’s lean enterprise conversion process. The initiative already has achieved significant improvements for Photo Etch in key areas, including order entry, purchasing, material control and engineering.
SEA is a non-profit alliance formed by aerospace, defense and space companies. The organization’s mission is to make the U.S. supply chain more globally competitive by creating a single lean enterprise system.
About Photo Etch
Photo Etch designs and manufactures displays and control panels used for navigation systems, as well as military and commercial airborne and ground communications. The company also manufactures flight simulation and training components. One of Photo Etch’s specialties is night vision technology for airborne military operations. Photo Etch’s client base includes major defense contractors like Boeing, Lockheed-Martin, L-3 Communications and Rockwell Collins, as well as U.S. Department of Defense agencies like the U.S. Air Force and U.S. Navy. Founded in 1960, Photo Etch follows ISO 9001 and SAE AS9100 quality standards and has implemented a company-wide lean manufacturing initiative. The firm operates from a 50,000-square-foot facility in Fort Worth.
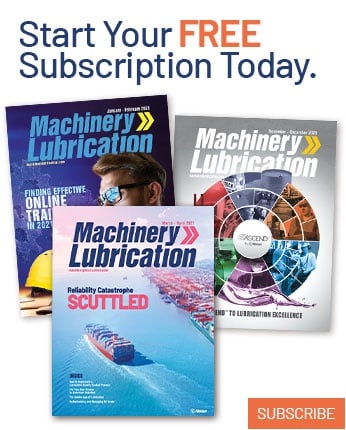