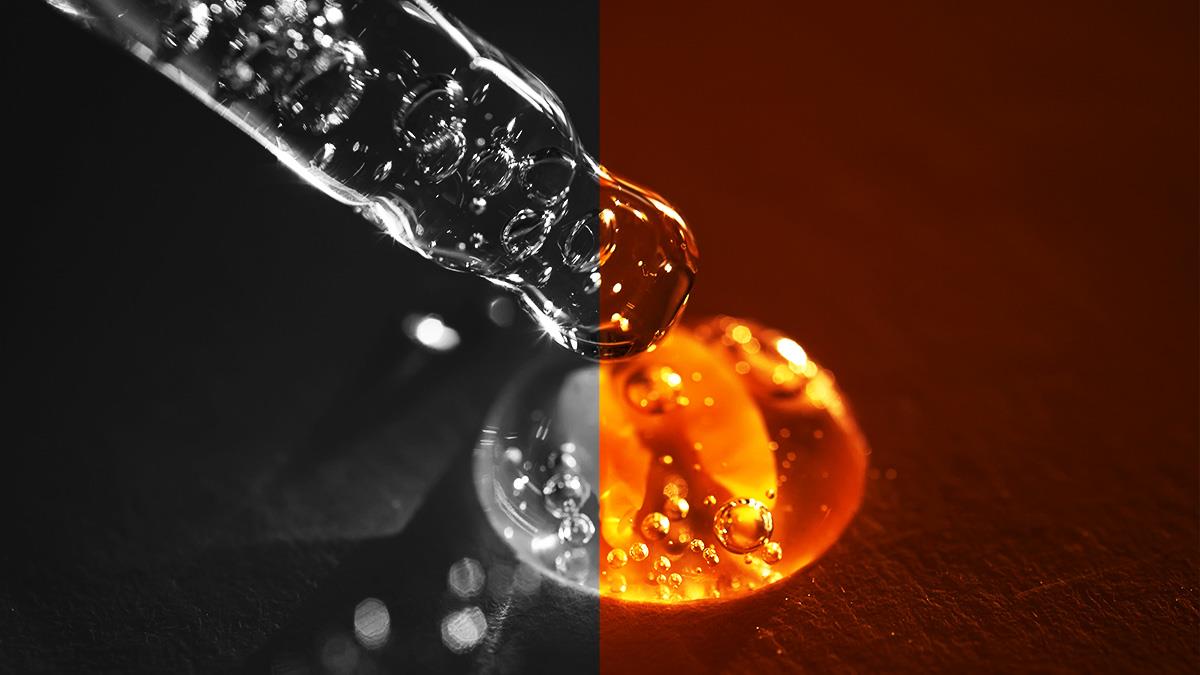
Maximizing plant reliability and efficiency is crucial for success. Unexpected downtime and inefficiencies can lead to lost production, increased costs, and safety concerns. One essential tool for achieving these goals is oil analysis. By exploring the possibilities of oil analysis, facilities can understand how implementing this strategy can help identify potential problems early, allowing team members to prevent failures, optimize their maintenance practices, and ultimately enhance plant reliability and efficiency.
Implementing an Oil Analysis Program
Oil analysis is a
predictive maintenance technique that involves analyzing a lubricating oil's physical and chemical properties to understand the condition of the oil and the machinery it lubricates. Common tests that have proved extremely useful for facilities in every industry include:
-
Wear Metals Analysis: This test helps identify abnormal wear patterns in machinery by detecting metal debris from specific components. This enables early detection of potential failures, preventing catastrophic breakdowns and costly downtime. The analysis also allows for targeted maintenance on specific components showing wear, allowing facilities to unnecessary repairs and reduce maintenance costs.
-
Viscosity Measurement: This test assesses the oil's thickness and ability to flow efficiently, which is essential for proper lubrication performance. It ensures that the viscosity is optimal for the operating conditions, reducing friction and energy losses and leading to smoother operation. It also minimizes oil consumption by utilizing the correct viscosity grade, eliminating unnecessary oil changes and associated costs.
-
Measurement of Acids and Bases: This test evaluates the oil's ability to neutralize acids formed during operation and monitors acid buildup, helping to protect components from corrosion. This helps maintain an adequate TBN (total base number) or TAN (total acid number), preventing acidic wear and maximizing equipment lifespan, which reduces replacement costs. Additionally, it optimizes oil change intervals based on TBN depletion or TAN accumulation, preventing unnecessary changes and reducing disposal costs.
-
Particle Counting: This test measures the size and quantity of contaminants present in the oil, indicating potential evidence of wear or external contamination. This early detection of excessive contamination allows for timely filtration or oil changes, preventing abrasive wear and protecting equipment. It may also assist in identifying sources of contamination, such as dirt, enabling corrective actions to prevent future issues and improve overall system health.
-
Infrared Spectrometry (IR): This test provides a detailed analysis of the chemical composition of oil contaminants by identifying oxidation and nitration products, fuel dilution, water, and other potential issues. This early detection allows for prompt oil changes, preventing lubrication performance from deteriorating and avoiding increased friction.
Essential Tips for an Oil Analysis Program
Oil analysis goes beyond merely checking oil cleanliness. It offers deeper insights into the health of your equipment by analyzing wear debris, contamination levels, and the oil's ability to perform its lubrication functions. This information aids in predicting potential issues before they escalate into costly failures.
When designing or updating an oil analysis program, there are four steps that should be taken:
-
Define Program Goals and Scope: Clearly identify what you want to achieve with oil analysis, such as improving reliability, reducing downtime, or optimizing equipment performance.
-
Establish Sampling Procedures: Determine sampling points, frequencies, and procedures to ensure representative and reliable data.
-
Partner with a Qualified Laboratory: Choose a reputable laboratory with expertise in your industry that performs the tests you require.
-
Analyze and Interpret Data: Regularly analyze results, identify trends, and take corrective actions based on insights.
In addition, it can be beneficial to seek the advice of a data analyst. A data analyst's job is to explain and, if necessary, recommend actions for rectifying significant changes in the lubricant or the unit's condition. Reviewing comments before looking at the actual test results will provide a road map to the report's most important information. Any actions that need to be taken are listed first in order of severity, and justifications for recommending those actions will immediately follow.
Working with the Lab
Effective communication between customers and the laboratory is crucial for enhancing the laboratory's performance and overall client satisfaction. By establishing clear, two-way communication channels, customers can provide valuable feedback on services, results, and recommendations, allowing the lab to improve and tailor its offerings to meet client needs.
This dialogue also ensures customers are promptly informed about their test results, analyses, and recommendations, fostering trust and reliability. By encouraging transparent communication, laboratories can address concerns, implement necessary changes, and build stronger relationships with their clients, ultimately leading to increased satisfaction and success for both parties.
To automate and streamline the entire process from the laboratory to the customer end, consider the following steps:
-
Develop an integrated digital platform that connects customers directly with the laboratory, including E-labels. This platform should provide a portal where customers can place orders, track sample progress, receive results in real-time, and communicate directly with lab personnel.
-
Use advanced data management systems to store and analyze test results. These systems automatically generate comprehensive reports that are shared directly with customers via the digital platform, minimizing delays. With the help of a data management system, the technology facilitates quicker turnaround and sales by making laboratory sample processing more efficient. This increased throughput in sample analysis enhances overall laboratory performance, allowing for faster results delivery to clients, thereby improving satisfaction and potentially driving further sales.
-
Include a feedback mechanism on the digital platform to gather customer feedback on services and results, allowing for continuous improvement in efficiency and client satisfaction.
Implementing these steps can streamline and automate the entire process, resulting in a more efficient operation and higher client satisfaction.
Conclusion
When acted upon, regular oil analysis can significantly improve plant efficiency by minimizing downtime and associated production losses, reducing energy consumption through optimized lubrication, lowering maintenance costs by preventing failures and extending equipment life, and optimizing oil usage and disposal costs through informed decisions.