Building a Strong Culture in Maintenance & Reliability
Badil Elhady, Reliability Centered Roadmap
Tags:
kaizen,
maintenance and reliability
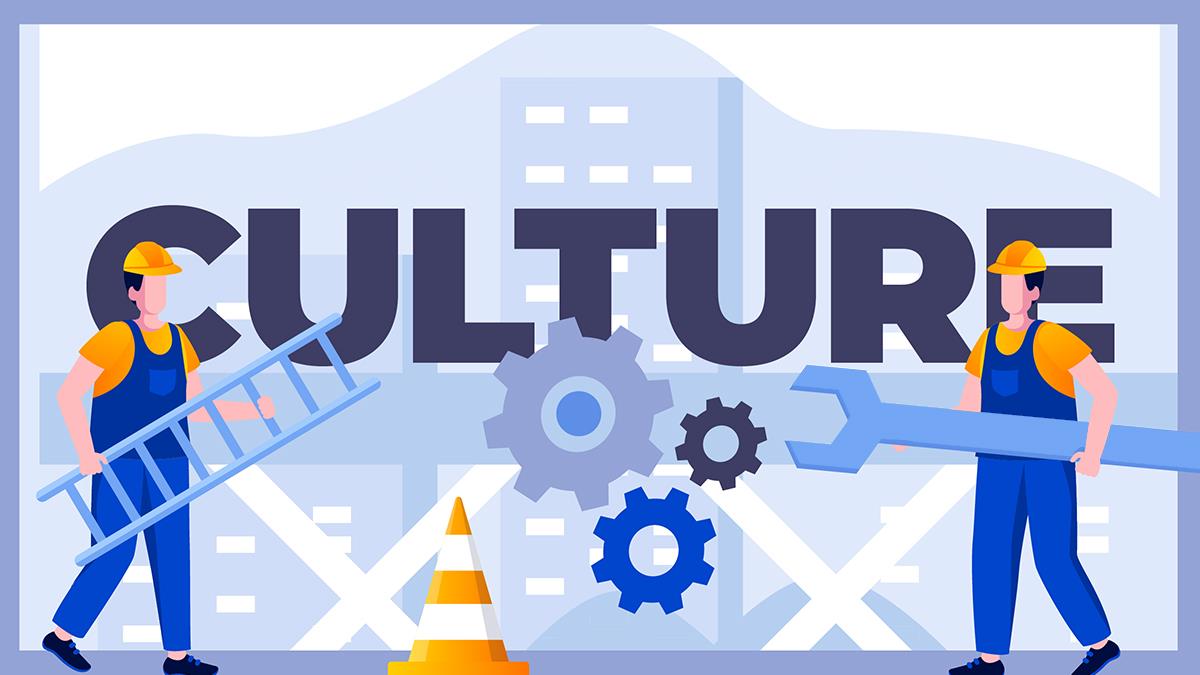
In my extensive career as a maintenance and reliability engineer, and later as a consultant specializing in maintenance and reliability (M&R) and asset management, I've had the privilege of collaborating with plant leaders and maintenance managers across diverse industries. My journey has taken me from organizations at the early stages of maturity to those operating at world-class standards. This spectrum of experience has provided invaluable insights, aka “key takeaways,” particularly in understanding the distinct challenges faced by less mature organizations and the best practices employed by more advanced organizations.
Culture is one of the most significant areas I've identified for driving sustainable improvement. A strong, positive culture is foundational to achieving excellence in M&R. Maintenance managers frequently seek guidance on cultivating such a culture, leading to a consistent request for actionable strategies and recommendations. When working with customers, I emphasize the importance of culture in our work. The following insights serve as the cornerstone of our approach. I am honored to share my modest experience and provide high-level recommendations (with examples) I’ve used to guide maintenance leaders.
Key Takeaways and Recommendations
-
Leadership Commitment - Leadership commitment is crucial for driving a culture of reliability. Leaders must actively demonstrate their support for maintenance and reliability initiatives, prioritizing these efforts within the organization’s vision. Regularly communicate the importance of reliability, allocate necessary resources, and participate in maintenance activities to show engagement. Avoid a hands-off approach and underestimating the impact of leadership visibility on team morale and motivation. For example, a plant manager who frequently attends maintenance meetings and acknowledges the team's efforts can significantly boost morale and commitment.
-
Continuous Training and Development - Investing in continuous training and development ensures the team has the latest skills and knowledge. This fosters a culture of learning and improvement, which is essential for maintaining high standards of reliability. Organize regular training sessions, workshops, and certifications. Encourage team members to pursue further education and professional development. Avoid neglecting training due to budget constraints or time limitations, leading to skill gaps and decreased performance. For instance, offering online courses and workshops on predictive maintenance technologies can keep the team updated on industry advancements.
-
Effective Communication - Open and transparent communication is the backbone of a reliable maintenance culture. It builds trust, ensures everyone is informed, and aligns the team towards common goals. Implement regular meetings, updates, and feedback loops. Use clear, concise, and consistent messaging across all levels of the organization. Avoid siloed communication and withholding information, which can lead to misunderstandings and negatively impact morale. For example, a weekly newsletter detailing maintenance schedules, upcoming projects, and team achievements can keep everyone informed and engaged.

-
Recognition and Reward Systems - Recognizing and rewarding outstanding performance boosts morale and motivates the team to maintain high standards. It also reinforces positive behaviors and achievements. Develop a structured recognition program, celebrate successes publicly, and provide tangible rewards such as bonuses or career advancement opportunities. Avoid arbitrary or infrequent recognition, which can diminish its impact and fail to motivate the team effectively. For instance, a monthly "Employee of the Month" program with rewards such as gift cards or extra leave days can encourage consistent high performance.
-
Empowerment and Accountability - Empowering employees to make decisions and take ownership fosters a sense of responsibility and engagement. Coupled with accountability, it ensures that team members are committed to their roles. Delegate authority, provide necessary resources and set clear expectations. Hold regular reviews to ensure accountability and support. Avoid micromanaging and the lack of accountability, as these can stifle initiatives and lead to complacency issues. For example, allowing maintenance technicians to make on-the-spot decisions during equipment breakdowns can speed up recovery and demonstrate trust in their expertise.
-
Data-Driven Decision-Making - Utilizing data and analytics for decision-making ensures that strategies are based on facts and trends rather than assumptions and emotions. This leads to more effective and efficient maintenance practices. Implement robust data collection and analysis tools, train the team on data interpretation, and use KPIs to guide decisions. Avoid ignoring data insights or relying solely on intuition, resulting in suboptimal strategies and missed opportunities. For instance, using vibration analysis data to predict bearing failures can help schedule timely replacements and avoid unexpected downtimes.
-
Collaboration and Teamwork - A collaborative environment enhances problem-solving and innovation (this is a communication outcome). When team members collaborate and share knowledge, they can address challenges more effectively. Encourage cross-functional teams, foster an inclusive culture, and create knowledge-sharing and collaboration platforms. Avoid fostering competition over collaboration, as this can lead to silos and reduced overall effectiveness. For example, organizing regular cross-departmental workshops to tackle common issues can lead to innovative solutions and more robust team bonds.
-
Proactive Maintenance Strategies - Shifting from reactive to proactive maintenance minimizes downtime and extends the lifespan of assets. It involves planning and performing maintenance activities before issues arise. Implement predictive and preventive maintenance programs, schedule regular inspections, and use condition monitoring tools. Avoid a reactive approach that only addresses problems as they occur, which can lead to higher costs and more frequent breakdowns. For instance, using thermal imaging to detect electrical issues before they cause failures can prevent costly downtime and repairs.
-
Safety First Culture - Prioritizing safety in all maintenance activities protects employees and assets. A strong safety culture also enhances overall operational reliability. Enforce safety protocols, conduct regular safety training, and encourage reporting and addressing safety concerns promptly. Avoid complacency towards safety measures and overlooking minor safety issues, as these can escalate into major incidents. For example, implementing a "Stop Work Authority" policy empowers employees to halt operations if they identify unsafe conditions, ensuring safety is never compromised. It also demonstrates the priority of safety within the reliability culture.
-
Continuous Improvement Mindset - A continuous improvement mindset drives the pursuit of excellence. It encourages the team to constantly seek ways to enhance processes and outcomes. Implement a structured continuous improvement program, encourage innovative thinking, and regularly review and refine maintenance processes. Avoid stagnation and resistance to change, as this can hinder progress and limit the potential for improvement. For instance, conducting regular kaizen events to identify and eliminate inefficiencies can lead to significant process improvements and cost savings.
Recommendations
-
Establish Clear Vision and Goals - Setting a clear vision and well-defined goals aligns the team’s efforts with the organization's objectives. This clarity drives focus and purpose, ensuring everyone understands their role in achieving success. Develop and communicate a compelling vision for maintenance and reliability, and set specific, measurable, achievable, relevant, and time-bound (SMART) goals. Avoid vague or unrealistic goals that can lead to confusion and lack of direction. For example, a clear goal could be reducing unplanned downtime by 20% over the next year by implementing predictive maintenance strategies.
-
Develop a Robust Maintenance Plan (Department Strategy) - A comprehensive maintenance plan outlines the necessary tasks, schedules, resources, and budgets required for effective maintenance operations, serving as a roadmap for achieving reliability. Create detailed maintenance schedules, allocate resources efficiently, and regularly review and adjust the plan based on performance and feedback. Avoid neglecting plan updates or failing to consider resource constraints, which can lead to inefficiencies and unexpected downtimes. For instance, a robust plan might include quarterly equipment inspections, monthly calibration checks, and an annual overhaul schedule.
-
Invest in Technology - Advanced maintenance technologies such as optimizing the Computerized Maintenance Management Systems (CMMS), Internet of Things (IoT), and Artificial Intelligence (AI) can significantly enhance maintenance efficiency and effectiveness. Assess current technological needs, invest in relevant technologies, and provide training for staff to leverage these tools entirely. Avoid underinvesting in technology or failing to train staff, as this can result in underutilized tools and missed opportunities for improvement. For example, implementing and improving a CMMS can streamline work order management, track asset performance, and schedule preventive maintenance.
-
Engage and Involve Employees - Involving employees in decision-making fosters a sense of ownership and commitment, leading to proactive contributions. Create forums for employee feedback, involve them in problem-solving sessions, and encourage their input on maintenance strategies. Avoid top-down decision-making without employee input, which can lead to disengagement and lack of buy-in. For example, forming cross-functional teams to address specific maintenance challenges can harness diverse perspectives and innovative solutions with knowledge sharing.
-
Benchmark and Learn from Best Practices - Benchmarking against industry leaders and adopting best practices helps an organization stay competitive and continuously improve its maintenance processes. Identify industry benchmarks, participate in conferences, and engage in professional networks to gather insights and implement best practices. Avoid complacency and the assumption that current practices are the best without exploring external innovations and improvements. For instance, adopting a leading organization's best practices, such as reliability-centered maintenance (RCM), can optimize maintenance strategies and improve asset reliability.
Implementing these recommendations can significantly strengthen the culture within maintenance and reliability programs, fostering continuous improvement and driving organizations toward world-class maintenance standards.