Case Study: Efficient Maintenance Saves Thousands in Gearbox Replacement Costs
Javed Ahmad, Safwa Cement Company
Tags:
vibration analysis,
condition monitoring
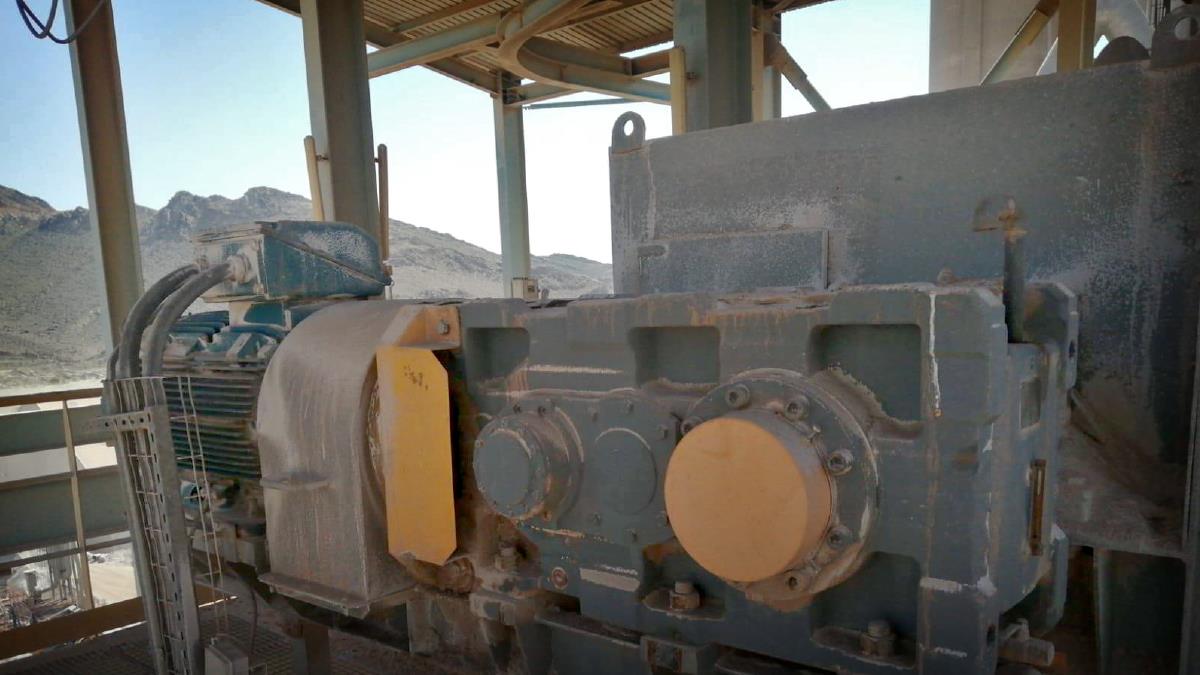
A limestone transport belt conveyor
gearbox, which had been running smoothly for four years with normal vibrations below 2 mm/sec, began to show increased vibrations and jerks. The mechanical inspector reported the gearbox’s behavior had changed, and within three weeks, the vibration at the gearbox input shaft vertical position surged to 14 mm/sec, accompanied by abnormal noise. This situation was critical as the gearbox fed two raw mills, and a spare gearbox was unavailable for several months.
Gearbox Details and Initial Observations
-
Gearbox Type: SWE-EURODRIVE X3KA180/HH/BB
-
Power: 183.3 kW
-
Motor RPM: 1451
-
Gearbox RPM: 51
-
Oil Type: SHC ISO 320 (Synthetic oil)
Initial observations incorrectly suggested looseness in the 1st stage gear bearings.
Inspections and Actions Taken
-
Visual Inspection: No abnormalities were found in the gears and bearings.
-
Oil Replacement: The gearbox oil was replaced and flushed to remove possible metal particles.
-
Air Breather Cleaning: The gearbox air breather was cleaned.
-
Motor Testing: The motor was decoupled and tested alone, and no issues were observed.
-
Drive Coupling Alignment Check: The alignment was confirmed to be good.
-
Rubber Elements Replacement: Drive coupling rubber elements were replaced, although the older ones were still good.
-
Vibration Analysis: An external resource used an EMERSON CSI 2140 condition monitoring analyzer. The vibration spectrum indicated peaks at frequencies matching the belt drive drum bearing, suggesting the issue was with the drive drum bearings rather than the gearbox or motor.
Upon further inspection, the non-drive side bearing clearance was 0.5mm, exceeding the acceptable range of 0.22mm. This
defective bearing was replaced, leading to normal equipment operation with vibrations reduced to less than 2 mm/sec.
Conclusion
The drive drum’s non-drive end bearing was defective. By addressing this issue promptly, significant costs and downtime were avoided.
Savings and Safe Operation
-
Gearbox Preservation: Continuous operation under high vibration would have damaged the gearbox, costing approximately $27,000.
-
Manpower Savings: Planned maintenance saved manpower costs compared to emergency breakdown repairs.
-
Safety: No safety incidents occurred, thanks to a comprehensive risk assessment.
Cost Savings Comparison

Production Cost Savings Comparison
Photographic Evidence

Lessons Learned
-
Systematic Diagnostics: Combining visual inspections with advanced vibration analysis is crucial.
-
Cost-Saving Benefits: Timely maintenance prevents expensive breakdowns.
-
Safety Importance: Planned maintenance helps avoid safety incidents.
-
Hidden Defects Challenges: Diagnosing hidden defects requires careful analysis and expertise.
-
Maintenance Strategies: Effective preventive and predictive maintenance strategies are essential for operational efficiency.
By meticulously diagnosing and addressing the gearbox issue, the maintenance team not only saved substantial costs but also ensured the continuous and safe operation of the plant’s critical equipment.