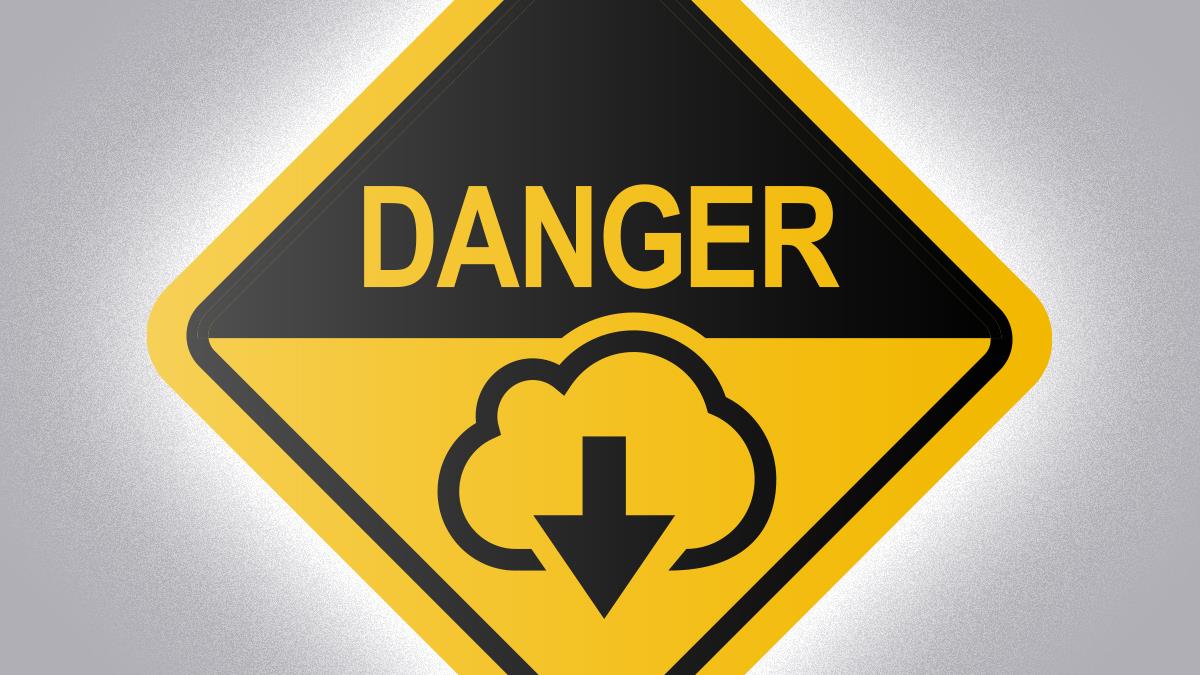
In the early 90s, I started my professional career as an associate consultant in the software business. Datastream was a relatively new company with a product that allowed manufacturing organizations to start capturing the costs associated with maintenance. This revolutionary product was called a
Computerized Maintenance Management System (CMMS). The software tool would capture spare parts inventory and labor expenses tied to a piece of equipment in production. Each spare part (a v-belt costing $10 each) and each labor hour (an electrician getting paid $25 per hour) would be documented on a work order. Once this work order was closed, these expenses were charged back to that equipment. The organization could view expenses associated with critical assets, their departments, cost centers, and production lines through detailed reports. This groundbreaking tool quickly replaced the traditional pencil and paper documentation and was adopted by manufacturing organizations worldwide.
Asking maintenance technicians to log their time and spare parts utilized for a job (into a computer) was received with mixed results at the time. Many maintenance professionals felt their primary duty was keeping the machines up and running. A good bit of education went into creating a uniform understanding of the organizational benefits of running production proactively. As a personal benefit, technicians could learn from each other's mistakes and get an accurate picture of trends that went into day-to-day maintenance on these machines. They no longer had to scavenge through
OEM manuals and wonder who had worked on their machines during off-shift hours. On the other hand, this technology transformed the way organizations view maintenance. It provided a clear line of sight to maintenance expenditures and awarded transparency to the management of the day-to-day activities of their workforce.
Evolution of Maintenance Management: From CMMS to EAM
Enterprise Asset Management (EAM) systems gained prominence in the late 90s and early 2000s as a reflection of a broader, enterprise-wide approach to asset management. EAM systems were built upon the foundation of CMMS systems. Still, they expanded their functionality to encompass a broader range of asset-related activities, including asset tracking, performance monitoring, lifecycle management, and strategic planning. This transition forced many organizations to focus on a broader approach in proactively capturing data and optimizing their processes to support a proactive work environment. We started to see an introduction of roles into the manufacturing workforce, which included planners & schedulers, reliability engineers, predictive maintenance technicians, and data analysts, to name a few. These positions were required to proactively manage the newly formed processes and utilize this data for meaningful results.
Challenges of EAM Adoption: Lessons Learned
These early EAM systems (Infor, SAP, Oracle, IBM Maximo, JD Edwards) laid the foundation for the comprehensive asset management solutions available today, offering organizations the tools and capabilities to optimize their assets' performance, reliability, and lifecycle. Although these were useful programs for the financial folks, many maintenance organizations were not prepared to make another system change so quickly. These systems felt like obvious upgrades for the bean counters and could have been more user-friendly for maintenance departments to adopt easily. The companies who decided to migrate were forced to convert their maintenance data into the EAM system and start all over again. This meant dealing with the headaches associated with data migration, user training, and custom configuration while investing a lot of money to make this transition.
With typical EAM deployments costing hundreds of thousands of dollars, company leaders wanted to see immediate results for their software investment. Minimal consideration was put into the danger of converting garbage data into another legacy system while meeting aggressive project deadlines set forth through IT. Furthermore, many of these projects should have included an executive sponsor and key stakeholders from maintenance and finance. The exclusion of key stakeholders throughout this period often led to misalignment with business objectives, inaccurate data being transferred, limited visibility into actual asset performance, and missed opportunities for process improvement. Organizations should have involved finance and maintenance departments early to mitigate these risks and actively engaged them throughout the
EAM implementation process.
Now that the damage has been done, how does an organization identify and correct these mistakes moving forward?
Mitigating Data Migration Risks and Solutions
Some common signs of data migrations gone wrong can be reflected in more apparent equipment numbers, inaccurate materials (BOMs) bills, and disjointed asset hierarchies. When making the transition from mainframe (green-screen) computers to PCs, equipment numbers would often reflect things like the asset's site (10), location (05), type (02), manufacturer (06), model (21) in a numeric sequence (example 10-05-02-06-21). Unless you had a photographic memory or a series of Post-it notes beside your computer, it took a lot of work to quickly reference what equipment was being identified through its equipment number. Future CMMS programs eliminated this problem by adding fields on the record that contained this valuable information. It is expected to find organizations that still operate with these equipment numbers in their EAM system today, displaying a history of numerous system conversions.
Optimizing Maintenance Operations: BOMs and Asset Hierarchies
A Bill of materials is a structured list of MRO items required to keep a machine up and running. BOMs help a maintenance planner and technician quickly identify the spare parts and materials needed to perform a job. Without a good BOM, we are asking our maintenance technicians to go out and perform a job without the necessary tools to achieve the desired result (i.e. to prevent future failures). Unfortunately, this can be one of the most significant obstacles to overcome. Organizations must adequately consider the initial inventory item numbering scheme to add records for MRO spares by identifying them through a vendor part number or a general description. This led to duplicate inventory entries for the same item. With thousands of inventory items being brought into an EAM system throughout the history of the legacy program's existence, this can be a significant project required prior to building your first BOM. Duplicate inventory entries for a single inventory item can lead to disastrous results if not managed properly through the initial setup.
Assets are typically organized into levels or tiers, with each level representing a maintainable component as part of an asset hierarchy. It is easily described through an automobile example where you have a car (1), the car's engine (2), and the car's alternator (3). You can track costs back to each component, but you really want to get a holistic understanding of expenses for the entire automobile (1, 2, and 3). To do this, a tiered structure must be in place that ties each component to the primary asset. A disjointed asset hierarchy hinders reporting, as it limits the ability to aggregate data and generate meaningful reports. By establishing a clear and consistent asset hierarchy, organizations can improve asset visibility, streamline operations, optimize resource allocation, and make more informed asset management and investment decisions. Defining asset hierarchy is relatively easy but requires a systematic approach to identify the parent-child relationship. An asset hierarchy provides a clear roadmap to drive proactive maintenance activities when executed correctly.
Harnessing Technological Advances: APM and AI Integration
As EAM systems have matured throughout the years, system capabilities have grown to provide a wealth of information to fuel proactive behaviors in the workforce.
Asset performance management (APM) systems have real-time integrated sensors, data analytics, predictive maintenance, and condition monitoring. The amount of data APM systems generate can be substantial, especially in large-scale manufacturing environments with diverse asset portfolios. Managing and analyzing this data effectively requires robust data management practices, advanced analytics capabilities, and scalable infrastructure to handle the volume and velocity of data generated by asset monitoring and diagnostics.
Historically, world-class companies prioritized process efficiency over data optimization simply because the software system capabilities were not available to support proactive decision-making at the time. Today, we find ourselves in a world where it is no longer an option to take your time working on the process without considering the massive amounts of data being generated simultaneously. Generative artificial intelligence (AI) has opened a world of transformation through immediate data cumulation. By leveraging AI technologies, businesses can unlock the full potential of their data assets to drive innovation, competitiveness, and strategic growth in the digital era. Companies that are still processing the dangerous data dump mistakes will find themselves automating bad data and making even poorer decisions.
SAP S4/HANA: Transforming Maintenance Management
SAP is the world's most widely used system for enterprise resource planning (ERP). The SAP plant maintenance (PM) module has been updated to provide full capabilities in support of maintenance and reliability organizations effectively. SAP S4/HANA has opened the door for advanced capabilities in predictive maintenance, asset management and resource scheduling – eliminating the need for costly add-on modules found in previous versions. It's a perfect storm with most Fortune 500 companies making the transition to consolidate systems and convert to a single platform. This represents another opportunity for your organization to solicit stakeholder feedback, gain alignment, and plan for a successful conversion.
Partnering for Success: Addressing Data Quality
It can be overwhelming at times, but remember that outside firms can help you address poor data quality to remedy past mistakes and prepare for a proactive culture. If you find yourself cleaning up the errors from previous CMMS conversions gone bad, select a partner with practical experience in maintenance coupled with the technical capabilities to work with your IT team to create a mutually effective strategy. Companies that align business strategies with IT projects are better positioned to have a competitive advantage in today's marketplace.
Total Resource Management (TRM) has a practice dedicated to process and system efficiency. Our specialized services help align SAP Asset and Service Management with maintenance, reliability, and service best practices and eliminate gaps in your people, processes, and systems. The TRM Team is comprised of seasoned Maintenance experts and SAP PM professionals with a proven track record of successful implementations.