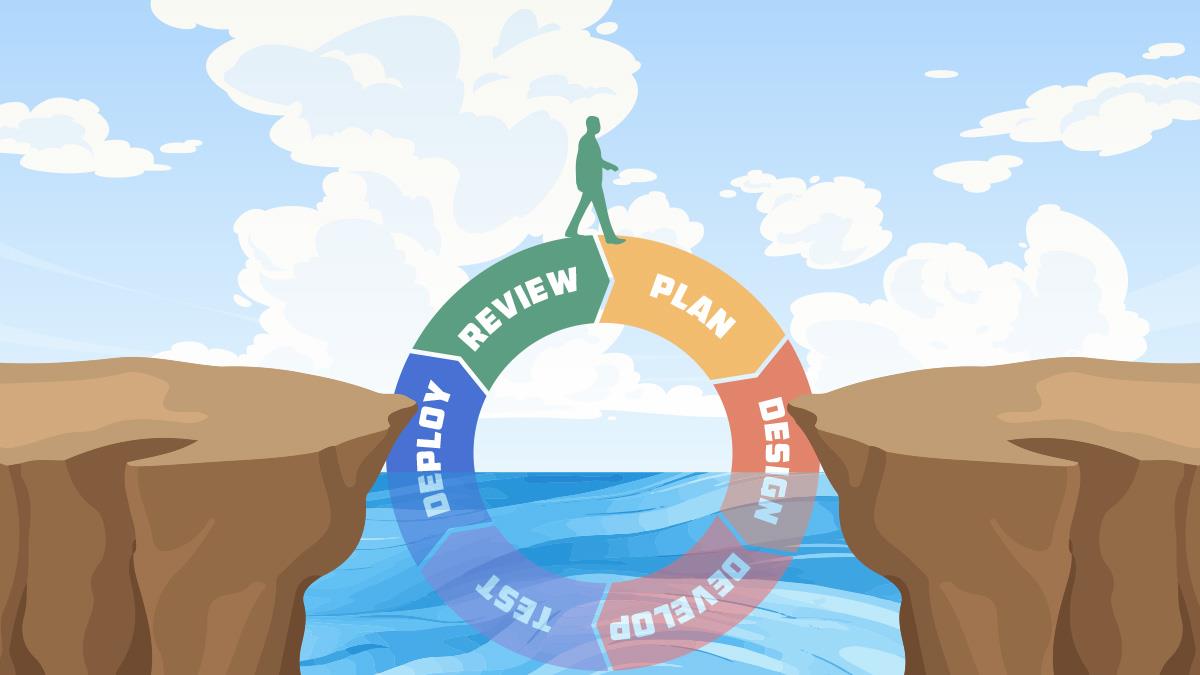
As the Software Engineering Director at
Noria Corporation, I have witnessed first-hand the benefits of leading my engineering team with agility. The high-trust environment has empowered them to innovate, adapt to changing requirements, and focus on delivering quality, working software. This got me thinking about how the methods to our madness in our technological world can benefit the manufacturing and lubrication worlds. Let’s explore some key concepts in becoming an agile organization that values flexibility, adaptability, and innovation.
The Agile Manifesto
While agile practices in software development have been around since the nineties, Agile development became popularized in 2001. Seventeen practitioners gathered at a resort in Utah to discuss various development methods. Although they did not all agree on everything, they did at the conclusion of their talks birth a manifesto with declarations of what their combined experience valued in software development. These were:
The authors believed that while there is value in the items on the right, the value of the items on the left were more influential on how work should be approached. Let’s see how this manifesto applies to manufacturing and the lubrication industry.
Individuals and Interactions
When it comes to my team of empowered engineers, I am thrilled to see the joy on their faces when they are allowed to utilize and share their skills, creativity, and problem-solving abilities, unbounded by strict regulations on processes or tools. Sure, some processes are important, but the key is to not focus so much on the processes that it detracts from an individual’s engagement with the work.
It is important to understand, however, that individuals don’t always naturally start off as free-thinking contributors. Like any cultural change in the realm of reliability and lubrication, we must first
get the team to buy in to change and break the status quo. A common challenge is that some people just have a mindset or fear that big brother is watching over their shoulder to ensure changes are made. This can be assuaged by focusing on the team and making sure they understand the “why” behind what we do and showcasing their wins early and often.
Companies that encourage open communication, knowledge sharing, and teamwork foster an environment of healthy collaboration, faster problem-solving, and a greater sense of ownership. This bottom-up approach of enabling their frontline workers to contribute ideas for process improvement and innovation leads to greater flexibility and responsiveness in production.
By prioritizing individuals and interactions, Agile Manufacturing cultivates a culture of continuous improvement and sets the team up for success. Employees are encouraged to experiment, learn from failure, and adapt quickly to new challenges. All of which are essential for staying competitive in today’s dynamic marketplace.
Working Product
My experience has taught me the importance of prioritizing the delivery of working software over the following:
-
Getting bogged down with comprehensive and often excessive documentation.
-
Investing time in the implementation details of requirements that will likely just change tomorrow.
-
Investing effort in other activities not directly related to the value a customer will ultimately get from the product.
This is like how
Lean Manufacturing principles preach the minimization of waste. Quality is key and you only get one shot at a good first impression. Though our initial release of any app may not have all the bells and whistles we can imagine, we focus on the minimal viability that the product can provide while still bringing value to the customer. Then, through an emphasis on rapid iteration and continuous feedback, we deliver ever-improving new releases to our end users.
Likewise, manufacturers practicing agility place an emphasis on rapid prototyping, iterative testing, and continuous refinement to bring products to market quickly and adapt them to changing customer needs. They have learned to minimize bureaucracy, reduce overhead costs, streamline processes, and eliminate unnecessary paperwork that doesn’t directly contribute to the production of their goods, the only thing the customer really cares about.
In a
lubrication program people often fall into the “paralysis by analysis” mode where it becomes unclear what the best path forward should be. We end up striving to fully optimize all processes, equipment, and lubricants, when making small, simple moves towards lubrication excellence can yield significant benefits as we go along. Warren Buffet said, “It is better to be approximately right than to be precisely wrong.” If we take this approach of improving before everything is completely perfect, we begin to showcase savings and benefits earlier and garner more attention and investment in our program.
Customer Collaboration
We live in a world where customers want to buy products tailored specifically for them. Customized the way they want it. It is up to us to be able to deliver these turn-key solutions or risk losing that business to somebody who will.
Take for example, Dell Technologies. Dell began by letting their customers pick and choose what they wanted in a personal computer and then built it for them to those specifications. This model made them a force to be reckoned with against other competing computer manufacturers at the time who were not as flexible or agile. Thus, equally important to collaboration within our own team is working closely with our customers throughout the development process to ensure their needs are met. We must seek to understand their expectations, answers their questions, and guide them down the right path to workable solutions because in the end they will only use what they find value in.
In Agile Manufacturing, organizations engage customers early and often to help understand their evolving needs and preferences. These manufactures forge strong relationships with those they serve. This tight collaboration affords them to gather valuable feedback, iterate on product designs and ultimately deliver products that meet or exceed expectations. What better way to build trust and loyalty among customers, leading to increased satisfaction and repeat business. The front-line personnel often have great insight and ideas into where improvement efforts would be most valuable, especially in lubrication. Their feedback is critical to making a program successful and their engagement is a must.
Responding to Change
Years ago, when I was just a junior developer at my first job out of college, I was subjected to the waterfall method of development. We would meet with the customer at the start of a project to gather all their requirements. Next, we would spend months perfectly planning out how the product should work in its entirety, with elaborate flow charts and diagrams. Meeting after meeting was held to go over every “what if” scenario and several gallons of energy drinks and coffee were imbibed. Then we spent months coding and testing before finally dropping a finished product on the customer’s desk and watching them in anticipation with wide, eager eyes. The result, however, was that over the last several months, the customer’s needs completely changed and we had to go back to the drawing board. This was the result of following a detailed plan.
Today, when my team works on a project, we aim to complete a set of features over a 1–3-week block of time called a sprint. The features we work on all live on a prioritized list of features known as the Product Backlog and we only figure out the implementation details for those features. We work with customers and other internal stakeholders to determine the prioritization of the features before each sprint to ensure that only the most important and still relevant work is being done. Thus, customer feedback is of utmost importance when deciding what to keep doing, what to modify, or what to stop doing completely. Often features that were requested previously but put lower on the product backlog either drop off as new situations invalidate the need for those features or rise to the very top due to new opportunities. This constant refinement of the product backlog allows us to adapt and adjust the work being done and enable us to continue to deliver a great product with each iteration.
Agile manufacturers also need to have a mindset where they can adapt quickly to shifts in market demand, technological advancements, or supply chain disruptions. They must be able to react to customer demands by adjusting how much they produce or leverage strategic partnerships all without sacrificing quality or incurring higher or additional costs. By embracing uncertainty and volatility, Agile Manufacturing organizations can capitalize on emerging opportunities, mitigate risks, and maintain a competitive edge in a rapidly evolving business landscape.
Kaizen, or continuous improvement, events, are often used in industry to quickly adapt to changing production or increasing reliability in an area. These events could be as simple as keeping lubrication techs properly trained and informed or ensuring that the lube room is kept clean and organized. A sprint, or Kaizen, may only last a couple days or weeks and in a lubrication program these are essential to showing steady improvement and creating buy-in among the team.
In today's fast-paced business landscape, Agile Manufacturing emerges as a transformative paradigm, mirroring the principles of Agile Software Development to navigate uncertainties and drive success. Drawing upon the foundational values of the Agile Manifesto, Agile Manufacturing prioritizes flexibility, adaptability, collaboration, innovation, and responsiveness, echoing the experiences of software development professionals who have long embraced these principles.