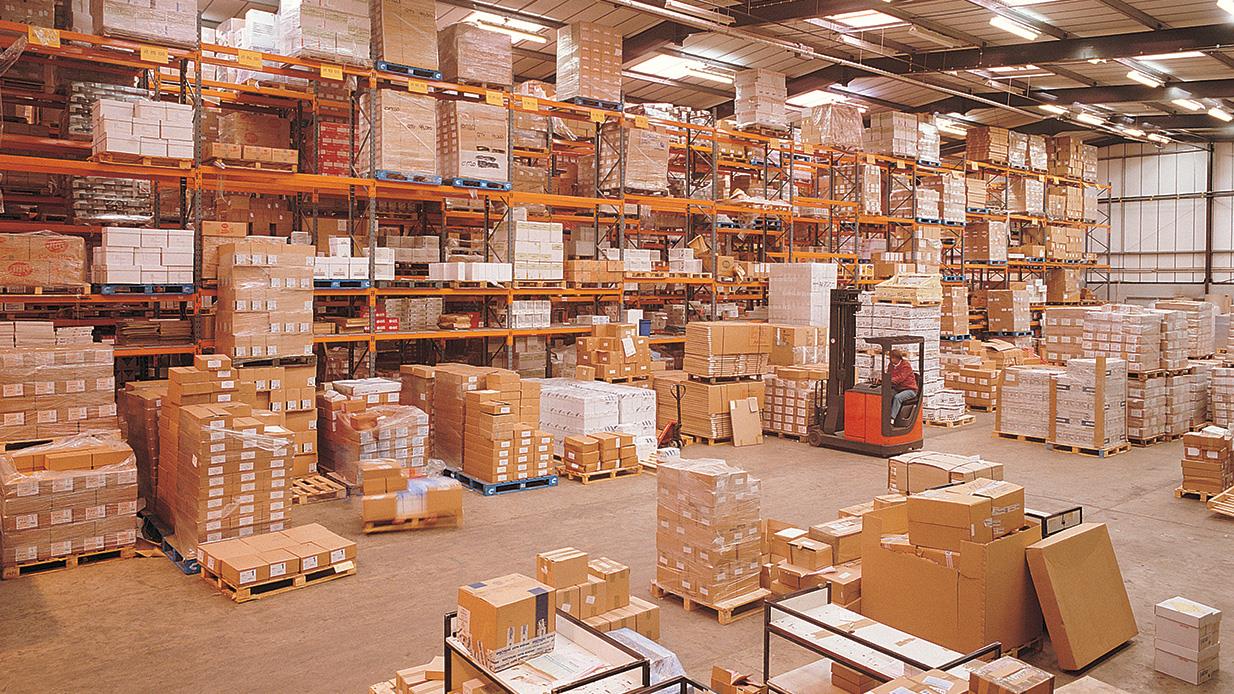
Warehouse space is at a premium these days, and the cost of under-utilizing your warehouse adds up quickly. The following space-saving tips will help you optimize your warehouse space, improve efficiency and decrease costs.
1. Calculate Your Current Space Utilization to Know Exactly How Your Space Is Used
Optimizing your warehouse space starts with determining exactly how much of your warehouse is being used and what it’s being used for. These warehouse utilization metrics are important to determining what steps you should take next.
Here are four easy steps to calculate your current space utilization:
Calculate Your Total Warehouse Size
-
Start with the total square footage of your facility.
-
Subtract office space, restrooms and any other space that isn’t used for storage.
-
Multiply the remaining square footage by the warehouse clear height. It’s the distance from the finished floor of the warehouse to any overhead object.
-
This leaves you with the total warehouse size.
For example:

Calculate Your Storage Area Size
-
Multiply the length and width of the outside dimensions of your racking by the height of the highest load in that area.
-
Don’t forget the height of the highest load may not be uniform throughout the warehouse. If you have one area with a 26-foot load height and another with a 20-foot load height, calculate them separately and add them together after.
-
This leaves you with a cubic volume for your storage area size. It’s your potential storage space or maximum storage space based on your current setup.
For example:

Analyze Your Potential Storage Area
-
Divide your storage area size by the total warehouse size and multiply by 100. What percentage do you get?
-
This number represents the amount of your warehouse that can potentially be used for storage. You should be between 22-27 percent. This range means your workers have enough room to move efficiently for picking, loading and unloading without wasting available space. If your percentage is lower than 22 percent, your space could be improved by optimizing your rack locations and aisle widths.
For example:

Now Calculate Your Space Utilization
-
Add up the volume of all the products that are stored in your warehouse. This information is likely available to you already in your warehouse management system (WMS).
-
If you’re using a WMS, simply divide the total volume of all the products by the storage area size and multiply by 100.
For example:

-
If you aren’t using a WMS, divide your storage area into logical sections (like rows of racking). Estimate the percent utilization of each row. Next, add the results together and divide by the number of each logical section or row.
For example:

-
This leaves you with your warehouse space utilization.
Warehouse space utilization is completely dependent on your specific warehouse, your storage system and your inventory characteristics, including the number of items, their size and how much you carry.
Once you’ve determined your warehouse space utilization you can analyze that number. For example, you may ask yourself, “Why is our utilization only 60 percent?” The answer might be, “We use a floor-stacking method which requires the entire row to be emptied before it can be filled again.”
Use this number to evaluate your warehouse for possible improvements and changes.
2. Pull Extra Space out of Thin Air with Strategic Beam Placement
The space between the top of the stored product and the bottom of the rack beam is reserved for forklift interaction. You’re only required to allow for 6 inches here, but you might have 8 inches or more between the load and the rack.

Here’s how to fix it:
-
Get out in the warehouse and measure!
-
Place a ruler or tape measure on the top of the product.
-
Measure up to the racking beam above it.
-
How much space do you have there?
If it’s more than 6 inches, evaluate why. Is the same size product placed here every time? Or is a larger item stored here at times? Can the racking be optimized by lowering the beams to just 6 inches above the top of the product?
3. Use Containers That Fit the Stored Item to Find Extra Space
Unpackaged parts are often placed in storage containers and stored on racks or shelves. Many warehouses use a “one size fits all” approach when it comes to these containers instead of having a variety of sizes.
“When the containers are stored on the rack, the space maximization can appear to be good, but in reality, there is a lot of wasted space inside of the containers, which is costing the company money,” says Martin Murray at The Balance Small Business
Here’s the solution:
-
Sort your unpackaged items by size.
-
Keep a variety of container sizes on hand and place items in the appropriate container for their size.
-
Then store smaller containers in one area of racking and larger containers in another.
You’ll find extra space you never knew you had and increase your storage capacity by simply storing items in containers that are the right size.
4. Maximize Your Space by Storing Items According to Size
You can optimize your available space by separating products by size and storing them with like-sized items. The process is similar to the previous tip, and it’s easier than you may think.
-
Determine how many different sized items you have in your inventory. For example, you may primarily use a 48-by-40-inch pallet, but a few products are smaller or larger.
-
Place those smaller or larger items in separate areas of racking. It doesn’t necessarily need to be a completely different row, just separated from the other items.
This strategy helps maximize the space you already have in your warehouse, and you’ll minimize the chance of misplacing the smaller items since they will all be together.
5. Follow the Pareto Principle to Use Your Space Effectively

You may have heard of the Pareto principle. It can be applied to many areas of business, including warehouse storage.
Victor Coronado said it best in his article on optimizing warehouses: “Eighty percent of the activity in a warehouse comes from 20 percent of the items, and these items are the fast-movers within the warehouse.”
Coronado outlined a product analysis to determine the optimum location for your SKUs according to the Pareto principle:
Sort Your SKUs into Different Product Categories
-
Look at average inventory levels and growth projections by SKU.
-
Don’t forget to include the unit of measure for each SKU in your facility (pallets, cases, etc.).
-
Consider other variables. Do you have date-sensitive products or items that require refrigeration? Is special material handling equipment needed to move certain products?
Classify Each Product Category According to Activity
-
You could classify the categories by the number of shipments or picks that are involved over a span of time.
-
Choose an activity measurement that makes sense for your warehouse.
Establish How Quickly Each SKU Is Moved
-
For example, you can use letters to reflect the velocity of movement. Use “A” to reflect the fastest and “C” the slowest.
Allocate Warehouse Space
-
Prioritize based on the SKU’s combination of each element. For example, you may have one area for pallets and another area for cases.
-
Store your highest turn SKUs together in the most accessible locations, such as nearest the shipping doors and at ground level.
6. Nix Obsolete Inventory to Increase Storage Space
Your storage space is extremely valuable, and obsolete inventory shouldn’t be taking up any of it. Here’s how to find and remove the space invaders:
-
Pull a velocity report from your warehouse management system (WMS).
-
Check to see how often each SKU is picked in a year.
-
Get rid of any items that haven’t been picked in that time. You could sell them for a huge discount, donate them to charity or see if they could be returned to the vendor. The point is to free up that precious storage space for items that sell.
7. Put Vertical Space to Use in Your Warehouse
You can increase your storage capacity by using the vertical space already available in your warehouse. This can be a huge win when trying to optimize warehouse space. It's already there! You just have to use it effectively.
-
Determine your warehouse clear height. It’s the distance from the finished floor of the warehouse to any overhead object.
-
Check local building code restrictions and make sure you can stay within their regulations.
-
Review your inventory to establish what can be moved. For example, you might consider moving your slower-selling products up higher to free up more accessible locations for quick sellers.
-
Research your options. This next step is completely dependent on the storage system you already have in place. Do you need a completely new racking system or can you add on to what you currently use? Keep your future needs in mind and select an option that provides the flexibility you need.
Using the vertical space available in your warehouse can be more cost effective than acquiring an off-site warehouse, and the increased storage capacity often brings improvements to productivity and operating efficiency as well.
8. Minimize Your Aisle Widths to Add Warehouse Space
Decreasing the width of the aisles between your racking can boost your available warehouse storage and add some much-needed square footage.

-
Use this simple equation to determine the minimum aisle width needed to accommodate your forklifts.
-
Once you have your minimum aisle width, compare it to your current aisle widths. You may find that you can save 2 feet in every aisle. By reducing the aisle width and adding more racking, you end up with more space for storage.
All that’s left now is to make the change and take advantage of all that extra space.
9. Clean up Your Floor to Gain Valuable Space
Whether you use a racking system or floor stacking, your floor space is extremely valuable since it’s one of the most accessible locations in your warehouse. It should be reserved for active inventory only. Here’s how to clean up those floors.
-
Remove debris. Not only is it a safety hazard, useless debris should not be taking up the most valuable space in your warehouse. Conduct regular sweeps of the warehouse and move waste to designated trash locations.
-
If you have unused equipment taking up floor space in your warehouse, evaluate its condition and determine if it can be resold. If the equipment can be used at a later date but isn’t useful at the moment, consider storing it in another location.
-
The same goes for unused pallets. Evaluate their condition and determine if they can be reused. If not, many pallets can be recycled rather than cluttering up your warehouse.
-
Eliminate obsolete inventory. We mentioned this in one of our previous tips, but it bears repeating. Get rid of any items that haven’t been picked in the last year (or an appropriate time span of your choosing).
10. Add a Mezzanine to Maximize Inventory Storage
Mezzanines provide the opportunity to increase usable square footage without actually expanding. Here’s how to get started:
-
First, you should determine your warehouse clear height. This is the distance from the finished floor of the warehouse to any overhead object.
-
Check local building code restrictions and make sure you can stay within their requirements for safety.
-
Review what can be relocated and how easily. In order to maximize inventory storage, other items such as supplies, small parts, equipment, files and even offices can be relocated to the mezzanine.
11. Reduce SKU Quantities to Minimize Overloading
Storing too many of one particular SKU can overwhelm your warehouse. This is more common than you might think. Someone in purchasing may get a great deal on a six-month supply of a certain product and your warehouse ends up clogged with too much inventory.
This scenario can be remedied fairly easily.
-
Speak to the supplier to work out a program where these products can be delivered in stages. This will reduce the impact on your facility.
-
Another option is to work with the purchasing department to create policies that prevent overloading in the warehouse. This can be the best long-term solution. For example, you could develop a policy that restricts purchases larger than a three-month supply. Or larger purchases must be arranged with staggered deliveries from the get-go. Find a solution that fits your facility
12. Implement Cross-docking
With cross-docking, stock isn’t stored unnecessarily between legs of its journey. Instead, it’s quickly sorted and returned to the distribution chain. The technique can be difficult to manage, but it certainly saves space.
Here’s how to get started:
-
Research the advantages and disadvantages of cross-docking. Look online, talk to supply-chain experts and get the answers you need.
-
Determine if cross-docking is right for your warehouse. Some materials are more suited to cross-docking than others. Just a few include retail products with consistent demand, pre-picked and packaged orders from another warehouse or production plant, perishable items, etc. Cross-docking also requires a high level of organization and up-to-date technology.
-
If you’ve decided to go ahead with cross-docking, you’ll have to implement strict inventory control practices.
-
Make sure to train employees on these new processes, safety procedures and best practices for the new system.
13. Improve Forecast Accuracy to Reduce Excess Inventory
Inaccurate forecasts can result in excess inventory that complicates warehouse inventory management. Here are a few ways to improve your forecast accuracy:
Use the Right Forecasting System
Instead of using a spreadsheet to generate forecasts, utilize software designed to manage inventory. Determine if the size of your facility and the complexity of your forecasting constitute the use of a different solution.
Forecast at the Right Level
You should periodically review the current forecast level. Is it still appropriate for your goals? For example, forecasting at the SKU level may not be enough. You may need to use greater detail by forecasting by sales region or channel.
Measure Your Forecast Accuracy and Track the Results
Check your forecasts against actual sales. You can use this information to fine-tune your forecasts and further improve your results.
14. Use 5-S and Lean Management Principles to Improve Warehouse Space
The 5-S methodology can improve your warehouse space, reduce waste and increase efficiency. You’ll be able to identify issues quickly, address their causes and prevent them from happening again.
Here are the basics for implementing 5-S in your warehouse:
Identify Potentially Unnecessary Items in the Warehouse
Evaluate their usefulness and eliminate any items deemed unnecessary, such as obsolete inventory or unused equipment.
Place All Necessary Items in Their Optimal Positions
In terms of inventory, place the highest selling products in the most accessible locations.
Look for the Root Cause of Every Problem That Arises
As you continue through the process, you may notice inconsistency or lack of organization in your warehouse. Make changes and implement countermeasures as you go. For example, you may notice that inventory is scanned individually when it could be done in batches.
Develop Rules or Policies That Allow You to Duplicate the Process Every Time
This way you can share the process with your team and onboard new associates.
-
Divide tasks into simple steps.
-
Perform the steps in the same way every time. This will help you easily identify systematic breakdowns and continue to replicate your successes.
-
Provide the items needed to efficiently and successfully complete the process every time.
Finally, make the process a habit so that associates follow standards as second nature.
15. Choose the Right Storage System to Increase Storage Density
Selective racking may not be the ideal storage system for your warehouse if you’re looking for more storage density. Here’s how to pick the right storage system for your warehouse:
Determine Your Top Requirements for the Storage System
Do you need a high storage density? Is pick selectivity still a big factor? Does the system need to accommodate a first-in/first-out (FIFO) or last-in/first-out (LIFO) inventory management system?
Identify Your Options
Research which storage system will work best for your warehouse and your top requirements. Here’s a quick overview of common storage options:
Floor Stacking
Pallets are stacked on the floor in rows. If products or loads can be stacked directly on top of each other, you can achieve extremely high-density storage with this option.
Selective Racking
Selective racking is one pallet deep. The racks can be placed back to back or against walkways. This option offers low storage density but high pick selectivity.
Double-Reach Racking

Instead of one row of racking or back-to-back rows, the racking is two rows deep. You could even place racking both back to back and two rows deep. This option reduces the number of aisles and maximizes storage density. Keep in mind that a specialty forklift is required for this system to work.
Drive-in/Drive-through Racking
With this option, pallets are stored on rails rather than shelf beams. Forklifts drive into the structure for pallet placement and removal.
Push-Back Racking
This style of racking features pallets placed on a series of nested, mobile carts which then glide on rails. When a new pallet is loaded, it pushes the other carts back. This is ideal when there is limited storage space available and the product is a consistent size and weight.
Pallet Flow Racking
When pallet flow racking is used, pallets flow down an incline on a series of rollers or wheels.
Weigh Your Top Options
There are trade-offs for each storage system. One may have a higher pick selectivity but takes up too much space for the storage density it provides. Consult experts and stakeholders. Get input from others to compare the choices and determine the best solution.
16. Run Racking Lengthwise to Increase Storage Capacity
For rectangular facilities, racking should most likely be set up lengthwise. You will get the most storage capacity by running the rows as long as possible, rather than in short sections.
Here’s how to check if this tip will work for you:
-
Create a warehouse layout schematic. Typically, it’s easiest to set it up using a one square = one square foot scale. You can use Excel for this.
-
Make sure you’re working with accurate measurements (sometimes that means measuring the space yourself). Every inch matters, because once you start installing your racking, you don’t want to run into problems.
-
Identify important sections like loading dock bays, packaging areas and offices.
-
Add in racking. Create one schematic for racking run lengthwise and one for racking in the opposite direction.
-
Calculate your potential storage area size for each option by multiplying the length and width of the outside dimensions of your racking by the height of the highest load in that area. Calculate areas with different highest load heights separately and add them together. This leaves you with a cubic volume for your storage area size. This is your potential storage space or maximum storage space.
-
Now compare the potential storage of racking lengthwise to racking in the opposite direction.
17. Add Storage in Unexpected Places to Optimize Your Space
Adding extra space in your warehouse can be as easy as installing racking over dock doors and above cross aisles. This additional storage doesn’t interfere with shipping, receiving or forklift operation. Plus, it adds extra space without physically adding square footage.
Here are suggestions for implementing this tip:
-
Determine what capacity you need. Over-dock racks in particular are usually built for lower capacity storage like lighter loads, empty pallets or packaging materials.
-
Consider your building and current racking. Over-dock racks often require wall ties or ceiling support. Keep in mind that cross-aisle or bridge-aisle racking is typically for selective racking only.
-
Check building codes. Ensure your additional storage is up to code.
-
Train your operators. Make sure your operators are aware of the changes at loading dock doors or cross aisles. They should be trained on any potential hazards and how to operate in these areas.
Now It’s Time to Add More Space
These 17 tips should help you save space, improve efficiency and decrease costs in your warehouse. Keep in mind that not all of these tips will make sense for every facility, so use the ones that will work best in your warehouse. Now it’s time for you to start optimizing your warehouse space.