Lean manufacturing or “going lean,” refers to a series of methods, philosophies and tools to minimize waste in your business and maximize production. Read about different ways your company can go lean.
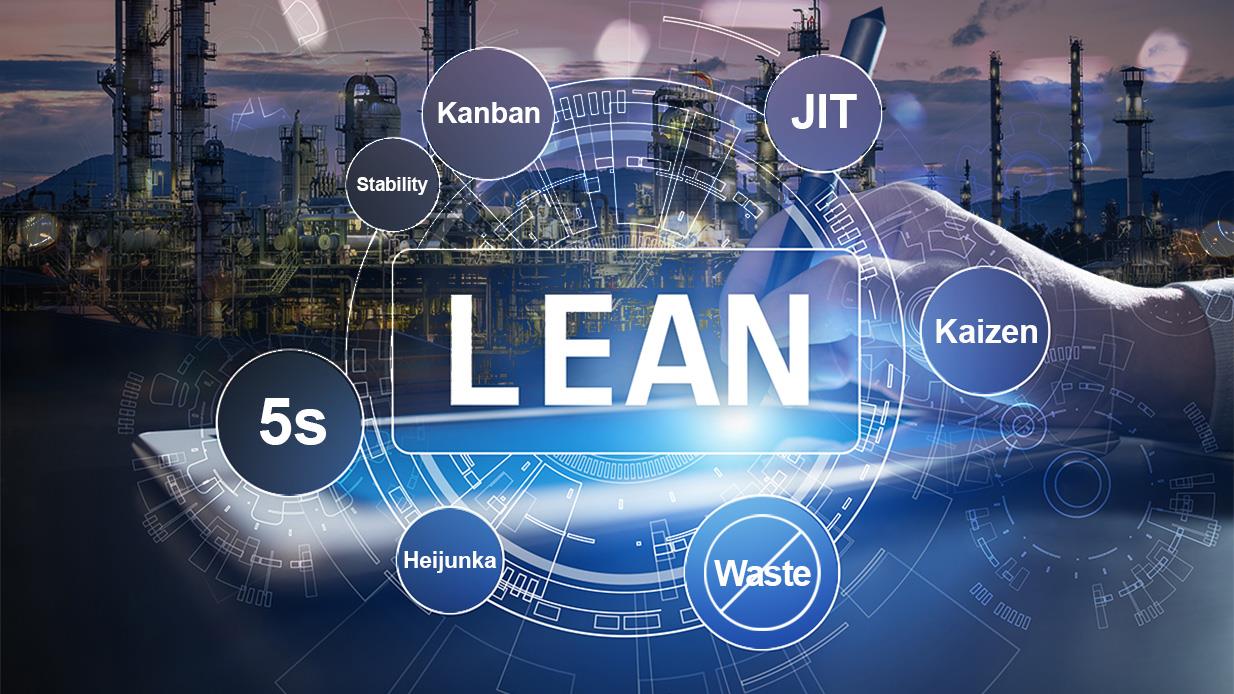
What is Lean Manufacturing?
Lean manufacturing, or simply “lean,” is a systematic method designed to minimize waste in a manufacturing system while productivity remains constant. Originating in Japan in the Toyota Production System (TPS), lean manufacturing strives to minimize waste within a manufacturing operation, with the idea being to clearly portray what adds value by removing what doesn’t. As your company begins to think about lean manufacturing it’s important to keep in mind the process of going lean takes time – like turning a cruise ship around.
There are several different lean techniques, allowing each organization to fit lean manufacturing techniques into its own distinct production process. We’re going to discuss the eight types of waste lean manufacturing seeks to eliminate and five common lean principals, tools and techniques manufacturers around the world have implemented into their manufacturing processes.
Lean Manufacturing: 8 Types of Waste
As we mentioned earlier, going lean starts with eliminating waste to focus on what adds value to your process, which leads to adding value for your customers. It’s important to know the types of waste and how they affect your business. There are eight types of waste:
-
Defects
-
Overproduction
-
Waiting
-
Non-utilized talent
-
Transportation
-
Iventory
-
Motion
-
Extra Processing
-
Defects: Probably the most visible type of waste, defects are scrap products or products that don’t meet commercial specifications. They can lead to many types of waste, most notably one we will discuss later – waiting. Defects cause delivery delays and logistics headaches which most likely leads to a decline in customer satisfaction. It’s also going to cost money to rework defected products. Fixing defects causes your company to spend extra time fixing issues and filing paperwork.
-
Overproduction: Companies love to produce in bulk. While it seems like a good idea initially, customer needs change fairly constantly and the market fluctuates and forces change even more frequently. Overproduction causes excess inventory which leads to storage expenses like paying for space and paying for people and equipment to move the product around.
-
Waiting: Waiting is a byproduct of many types of waste and it wreaks havoc on customer satisfaction. A good way to look at waiting is, a product or your customer might be ready for the next step (packaging or shipping for example), but the next step in your process isn’t ready to perform the task. In healthcare, this might look like a full waiting room. In manufacturing, this might look like machinery downtime causing packaging delays.
-
Non-utilized talent: Often overlooked as a form of waste, not using your employees to their full potential, talents or skills can have a big effect on your company’s bottom line. Poor teamwork, minimal training, bad communication and unnecessary administrative tasks are common examples of non-utilized talent waste.
-
Transportation: Transportation is the movement of goods from one location to another. In manufacturing, this might mean performing different tasks in different locations. For example, producing product parts in China and shipping them to America to assemble. This process doesn’t add value to the end product, it doesn’t change the end result and it adds more cost. If you look at Toyota’s manufacturing setup, many of their suppliers are near the production plants.
-
Inventory: Similar to overproduction, inventory waste happens when your product is sitting there waiting to be sold. The difference between overproduction and inventory waste is, inventory has a physical cost associated with it, whereas overproduction is assumed. Overproduction often causes inventory waste by making more than your customers want or assuming demand will be there down the road.
-
Motion: The unnecessary movement of people, machines or items that don’t add value is the waste of motion. In other words, wasting time. This form of waste is usually caused by not following the 5s’ lean manufacturing principal. Common examples include, employees looking for materials or equipment or poorly designed workspaces.
-
Extra Processing: Extra processing or over processing refers to adding work that isn’t required. Extra processing costs hit you in the form of the time of your staff, materials used and equipment wear, and they add up over time. It also makes your process less efficient because employees performing the extra processing tasks could be doing value-adding tasks instead.
7 Lean Manufacturing Principles, Tools and Techniques to Consider
Now that we‘re aware of the types of waste we want to minimize, let’s look at five common lean manufacturing tools and techniques to help you mitigate waste and maximize production.
-
Kaizen: The Japanese term “Kaizen” translates to “change for the better.” The idea behind Kaizen is continuous improvement. It makes teams work together proactively and take responsibility for their areas within the company. Together, employees make incremental improvements in the manufacturing process. With kaizen, there is always room for improvement, and workers should constantly look to improve the workplace. This philosophy also emphasizes that each individual's ideas are important and that all employees should be involved in the process to better the company. An organization that practices kaizen welcomes and never criticizes suggestions for improvement at all levels. This helps to create an environment of mutual respect and open communication.
How Kaizen benefits you
Implementing Kaizen improves your productivity, effectiveness, safety and lessens waste |
Benefit |
Description |
Less waste |
Inventory and employee’s skills are used more efficiently |
Employee satisfaction
& commitment |
Employees have a direct impact on how things are done which
gives them more of a stake in the company,
leading to a commitment to do a good job |
Improved retention |
Happy and engaged employees are more likely to stay put |
Customer satisfaction |
Engaged employees means improved product quality and fewer defects |
-
5s System: The 5S system is an organizational method stemming from five Japanese words: seiri, seiton, seiso, seiketsu and shitsuke. These words translate to organize, tidiness, clean, standardize and sustain. They represent a five-step process meant to reduce waste and increase productivity and efficiency.
How the 5s System benefits you
The 5s’ help you minimize multiple areas of waste |
Benefit |
Description |
Reduces cost through
less storage space |
Getting rid of unused materials, tools and equipment, and organizing frees up a lot of space.
This kind of cost savings hits on not only storage rental costs but heating and cooling,
cleaning and the maintenance of the space |
Cleanliness |
Cleanliness translates into improved maintenance and less downtime.
If a machine is clean, you’ll be able to spot defects and issues like oil leaks.
This lets you perform preventative maintenance to prevent downtime |
Safety |
Cleanliness directly relates to improved safety.
It removes clutter which can reveal electrical, chemical or mechanical hazards.
Organizing tools and equipment in areas close
to where they’re needed minimizes movement, reducing injury |
-
Seiri (organize): The first step, Seiri, involves eliminating clutter and unnecessary items from the workspace.
-
Seiton(tidiness or orderliness): Next, workers must set an order by ensuring there is a place for everything, and everything is in its place.
-
Seiso (clean): This step involves cleaning the workspace and always keeping it in a clean state.
-
Seiketsu (standardize): Standardizing all work processes and keeping them consistent, so any worker can step in and perform a job if necessary is vital.
-
Shitsuke (sustain): Finally, we want to constantly maintain and reinforce the previous four steps.
-
Kanban: Kanban helps eliminate inventory and overproduction waste by implementing a method for regulating the flow of goods inside and outside the factory. It translates to “billboard” or “visual signal” and relies on visual signals to help employees control inventory. A Kanban card can be placed in a visible area to signal when inventory needs to be replenished. With this process, products are assembled only when there is demand from the consumer, allowing companies to reduce inventory and waste. The Kanban method is highly responsive to customers because products can be manufactured by responding to customer needs instead of trying to predict their future needs.
A basic form of Kanban is having three columns: “To Do,” “Doing,” “Done.” Once you’ve begun a project or the first step in a process, move a colored sticky note with your name on it to the “Doing” column, so everyone knows where you’re at in the process. Columns can be labeled to match your particular project and there can be as many columns as you need.
How Kanban benefits you
Kanban is a great way to manage work processes and maximize time and efficiency |
Benefit |
Description |
Flexibility |
With the Kanban technique, priorities are always being reassessed based on the most recent information |
Continuous delivery |
Kanban helps you deliver exactly what your customers want by continuously delivering smaller batches of product.
This lets your team constantly update processes based on new business requirements |
Waste reduction |
Kanban improves your productivity and efficiency, reducing waste like over-production,
unnecessary motion, defects and waiting |
-
Heijunka: Heijunka is the Japanese word for “leveling.” Level scheduling is a type of production that purposely manufactures products in smaller batches by sequencing varying products in the same process.
For example, let’s say you produce sunglasses and you get an order for 500 of the same style of sunglasses each week. The orders come in as 200 orders on Monday, 50 on Tuesday, 100 on Wednesday, 100 on Thursday and 50 on Friday. Rather than trying to meet that order in sequential order, you could use Heijunka and level the demand by making an inventory of 100 sunglasses close to shipping for Monday’s order. Make sure 100 sunglasses are in inventory every Monday and the rest of the week, produce 100 sunglasses each day (a level amount).
Implementing Heijunka requires you to set the pace of your manufacturing according to what’s known as Takt time. Takt time is the rate at which your customer makes a purchase or the time it takes to finish a product to meet customer demands. In other words, you’re matching your production rates to meet your customer’s demands, creating a level process.
How Heijunka benefits you
Heijunka brings three major benefits to your manufacturing facility |
Benefit |
Description |
Predictability |
Leveling your production schedule enables predictability when it comes to producing goods |
Flexibility |
Leveling your production schedule reduces your changeover time |
Stability |
Leveling your production schedule lets you balance the use of labor and machines and predict demand |
-
Just in Time (JIT): Just in Time is a management philosophy involving only producing a product when the customer wants it, in the amount the customer requested it and sent to where they want it without it being hung up in inventory. In other words, instead of making and stockpiling products in anticipation of what your customers might want, you make what customers order when they order it. This lets you allocate your resources (employees, machines, etc.) to only work on things you’ll be paid for. Just in Time helps improve inventory costs, reduce space, reduce lead time, increase productivity and more.
What’s required for Just in Time?
Just in Time lean manufacturing plays off of many other lean tools and techniques. Here’s what you’ll need to implement the Just in Time philosophy.
-
Reliable equipment is vital for JIT to work properly. You can’t have machinery constantly breaking down or producing low-quality products.
-
Well designed workspaces are key for the JIT flow. Use the 5s system to improve workspace layout and flow to minimize inefficiencies.
-
Improve the quality of your workforce by setting up Kaizen teams, so employees take ownership of their own areas.
-
Define standards for how each operation should be performed.
-
Since JIT lean manufacturing doesn’t create inventory, it strives to produce only according to customer demand. Using the Kanban technique signals the previous process what needs to be made.
-
SMED: Single-minute exchange of dies (SMED) is a process used to greatly reduce the time it takes to complete equipment changeovers. Officially developed by Japanese industrial engineer Shigeo Shingo, the SMED process led to an average reduction in changeover times of 94 percent across multiple industries. Implementing a SMED process has multiple benefits when it comes to going lean and minimizing waste. These benefits include:
The SMED process involves a series of steps or "elements", which are categorized in two types: internal and external. Internal elements need to be completed while the equipment is stopped, while external elements can be completed while the equipment is running. The goals of SMED is to have as many external elements as possible while streamlining and simplifying all other elements.
Implementing SMED consists of five steps:
For a more in-depth look at implementing SMED and the SMED process, check out the link in the beginning of this section.
-
A decrease in manufacturing costs;
-
The ability to produce smaller lot sizes;
-
Improved schedule flexibility and responsiveness to customer demand;
-
Lower inventory levels;
-
Improved machine startups;
-
Identifying a pilot area;
-
Identifying elements;
-
Separate external elements;
-
Convert internal elements to external elements;
-
Streamline the remaining elements.
-
Poka-Yoke: Poka-Yoke – a Japanese term roughly translated to "mistake proofing" – is a technique used to make sure your lean process produces quality products. It's purpose is to minimize or eliminate defects by preventing, correcting, or bringing to light any human errors that are occurring.
A simple example of poka-yoke is when a car with a manual gearbox requires the driver to step on the clutch pedal before the vehicle will start. For cars with automatic transmission, the poka-yoke (process or step) is the switch that requires the car to be in park or neutral with the driver's foot on the brake before the car will start.
In manufacturing, poka-yoke can be implemented at any step of the manufacturing process where human error can cause something to go wrong. For example, a device holding pieces for processing might be modified to only allow pieces to be held in the correct orientation required for input. Another example would be a digital counter that counts the number of spot welds on each manufactured piece to ensure the welder makes the correct number of welds.
There are three types of poka-yoke for detecting errors in a manufacturing setting:
-
The contact method identifies defects by testing the product's shape, size, color and physical makeup.
-
The fixed-value method (constant number) sends out an alert to the operator if a predetermined number of movements are not executed.
-
The motion-step method (sequence) makes sure the predetermined number of steps for a particular process have been followed.
Generally, the operator is alerted when a mistake is impending (known as a warning poka-yoke) or the poka-yoke device prevents the mistake from being made itself (known as a control poka-yoke). Benefits of implementing poka-yoke include less money spent training operators; elimination of certain quality control operations; lessening the number of repetitive operations; a reduction in the number of product rejects; built-in quality control; preventing defected products from reaching your customers and more.
Benefits of Lean Manufacturing
Using lean manufacturing principals, techniques and philosophies to go lean gives you a competitive advantage by eliminating the eight types of waste discussed earlier. Let’s take a look at some real-world examples of how going lean gave companies the upper hand.
-
Thrustmaster of Texas: This case study from Lean Enterprise Institute (LEI) takes us to Thrustmaster of Texas. Thrustmaster manufacturers heavy-duty thrusters that rotate 360 degrees around a fixed axis. These thrusters are used on ships and other vessels so they can maneuver efficiently. During an 18-month process of going lean (considered a short time in the eyes of LEI), Thrustmaster implemented lean manufacturing techniques to streamline work and material flow which led to a 100-percent increase in on-time delivery. Now, the company’s production can fluctuate with market demand and new market opportunities are presenting themselves thanks to changes in cost structure.
-
Velux: is a Danish company that manufacturers skylights and roof windows operating out of Poland. It focused their lean manufacturing transformation on their production area. Its employees completely changed the layout of the production floor for better flow. The idea for this change stemmed from a five-day Kaizen. Once they saw the effects going lean had on their production, they decided to implement it to the whole supply chain – from design to final product. Through various lean manufacturing principals and tools, Velux introduced Kanban and the use of visual tools to help with realizing changes in their processes. Today, Velux continues to practice lean manufacturing and holds 5s assessments each month with different people to look for ways to keep improving.
Bottom Line
Nearly 60 percent of production activities in manufacturing operations around the world are waste, according to Vorne Lean Production. When it comes down to it, almost every company has room for improvement when it comes to minimizing waste, making high-quality products and lowering their overall production cost. If you decide to go lean, remember it takes time to implement the correct methods, tools and philosophies we’ve discussed. Once you’re team(s) learn these techniques, they’ll be able to reduce one or more of the eight types of waste just by doing their job.
As you consider implementing lean manufacturing, it's important to keep the lean manufacturing cycle in mind. There are five steps in the lean manufacturing cycle:
-
Identify value. This means thinking about the end customer and what they deem valuable.
-
Map the value stream. Layout all the steps within your process and get rid of those that don't add value.
-
Create flow. Figure out ways to make the valuable steps more streamlined in a tight sequence to provide the end customer with as much value as possible, quickly.
-
Establish pull. Create more demand from your end customers, so they're looking for the product rather than you having to push it on them.
-
Strive for perfection. Continuous improvement is key in lean manufacturing. The goal is to always be thinking of ways to eliminate waste and document and standardize the processes that generate success.
Finally, it's important to always respect the human elements when talking about going lean and implementing lean principles. This means striving to keep employees happy and engaged with their work by making this goal a core principle. Without a respect for employees and the people within your organization, people tend to disengage and not perform at a consistently high level. It's a relatively easy principle to put into practice as there are only a few elements to keep in mind, but each element tends to become difficult to manage since you're dealing with humans and not machines. Key elements include:
-
Don't overwork employees.
-
Show them their purpose by outlining what their work is achieving and align their purpose with their own goals.
-
Maintain a high level of accountability for successes and failures.
-
Always get to the root of any issue by speaking with employees directly.
-
Give stability and a little variety in their tasks.