Single-minute exchange of dies (SMED) is a process used to greatly reduce the time it takes to complete equipment changeovers. Below, we'll discuss exactly what SMED is, how to implement it and more.

What Is SMED?
Single-minute exchange of dies (SMED) is a process used to greatly reduce the time it takes to complete equipment changeovers. The term "single-minute" is a bit misleading in that it doesn't mean every changeover should only take one minute, but that every changeover should take less than 10 minutes, or a single-digit minute.
Setup reduction techniques were already being tested in the early 1900s with Ford Motor Co. using some techniques in 1915, as clearly described in the publication Ford Methods and Ford Shops; however, the first set of SMED processes were developed by Toyota.
After observing stamping presses with rapid-change capability, Toyota machine shop manager Taiichi Ohno purchased multiple presses and began working on rapid changeover processes. This eventually led to a reduction in the time it took to change tools from between two and eight hours to 15 minutes in the 1960s, to three minutes about a decade later, and to 180 seconds in the 1990s.
Single-minute exchange of dies (SMED) was officially developed by Japanese industrial engineer Shigeo Shingo – an ousted Toyota employee who moved to the United States and became a lean manufacturing consultant. Shingo's SMED process led to an average reduction in changeover times of 94 percent across multiple industries. That's like going from a 90-minute changeover to one that is less than five minutes.
Implementing an SMED program has multiple benefits in regard to minimizing waste and going lean. A successful SMED program can:
- Lower manufacturing costs. Quicker changeovers mean less equipment downtime.
- Produce smaller lot sizes. Quicker changeovers let you change products more frequently.
- Improve schedule flexibility, which helps with being responsive to customer demand.
- Lower inventory levels.
- Improve machine startups. Standardizing changeover processes ensures consistency and quality.
The Basics of SMED
In an SMED process, changeovers are comprised of steps or "elements." There are two types of elements: internal and external.
- Internal elements must be completed when the equipment is stopped.
- External elements can be completed while the equipment is running.
The main goal of the SMED process is to have as many external elements as possible while streamlining and simplifying all other elements.

Improving your changeover times by an average of 94 percent may be difficult to comprehend, but consider one of the most popular SMED examples: a NASCAR pit crew changing a tire. Pit crews use certain techniques to drastically lessen the time it takes to change a tire; a process that normally takes around 15 minutes for most people to change one tire takes a pit crew around 15 seconds to change four tires. Pit crews employ several SMED techniques, such as doing everything they can before the pit stop begins, using a coordinated team performing multiple roles simultaneously and creating a highly standardized process.
When it comes to the manufacturing world, Toyota noticed the most difficult tools to change were the dies on the larger transfer-stamping machines that make various parts of a vehicle's body. The problem? The dies had to be changed with the production of each car model. They also weighed several tons and needed to be built into the stamping machines with tolerances of less than 1 millimeter.
Taking a look at their current changeover process, Toyota engineers noticed the procedure entailed stopping the line, letting the dies down by overhead cranes, eyeballing positioning of the dies into the machines and then adjusting the positioning using crowbars while making single test stampings. With this procedure, it took anywhere from 12 hours to three days to complete.
To improve this process, Toyota first placed precision measurement devices on the transfer-stamping machines and recorded the measurements for each model's die. These standardized, pre-recorded measurements to install the die, as opposed to using human eyesight, immediately cut the changeover time to an hour and a half. Other improvements included scheduling the die changes in standard sequences as new car models moved through the plant, ensuring all tools needed for the die-change processes were nearby and scheduling the overhead cranes so the new die would be ready to go as the old ones were being removed.
Implementing SMED
Step 1 – Identify a Pilot Area
One of the first things to consider before implementing SMED is the pilot area. It might be tempting to pick a process with the longest changeover time. While that is a factor, you'll want to make sure of a few things, such as the following:

- The changeover time is short enough to fully understand and long enough to show significant improvement.
- There are multiple variations in changeover times. This tells you there is a great chance for improvement.
- There are multiple chances to perform the changeover each week. This lets you quickly test improvements.
- Employees in the proposed pilot area are engaged and motivated.
In this step, it's important to get everyone onboard with the SMED implementation; this includes all employees associated with the selection process and those who will work on the changeover.
Step 2 – Identify Elements
After you've determined your pilot area, it's time to work together with your SMED team to identify all the changeover elements – internal and external. One of the most effective ways to visualize every step is by videotaping an entire changeover as it is currently performed and then sitting down with your team to record lists of each element, reordering as needed. Include a detailed description of each task performed and how long each task takes to complete (cost in time). This video and outline can also serve as a baseline. Some things to keep in mind:
- A typical changeover results in around 30 to 50 elements on average.
- Capture both human and equipment elements. Many elements are human and can be easily optimized, as we'll see later.
- While videotaping a baseline changeover, have multiple team members observe and take notes. Compare their notes with what you discover while watching the video, breaking it down to ensure nothing is missed.
Once step two is finished, you should have a complete list of all changeover elements with a description and cost in time for each.
Step 3 – Separate External Elements
Can this element be performed while the machine is running? This is the question your team needs to ask of each element you documented in step two. Any element in the changeover process that can be completed with little or no change while the machine is in operation must be identified and labeled as "external" to the process; in other words, the element can be done before or after the changeover. In many cases, this step alone can cut changeover time in half.

Elements usually considered external might include the retrieval and inspection of parts, tools and materials (like instructions); any cleaning tasks that can be done while the SMED process is running; and quality checks.
Once step three is completed, you should have an updated list of changeover elements divided into external elements (before changeover), internal elements (during changeover) and external elements (after changeover).
Step 4 – Convert Internal Elements to External Elements
Which internal elements can be converted to external elements? This question should be at the forefront of everyone's mind as you go through the changeover process with a fine-tooth comb. Breaking down the question even further, your team might ask: If there is a way to make this element external, what would it be and how can we do it?
What's left after this evaluation is a list of elements that require further action. Prioritize this list so the elements with the most promising results are dealt with first. In other words, perform a cost/benefit analysis on each element from the list. In this case, "cost" is measured by the labor and materials you'll need to make the necessary changes, while "benefit" is measured by the time that will be removed from the changeover once the element is converted.
Consider the following techniques to convert internal elements to external:
- Advance preparation: Preparing parts in advance and keeping them in a ready-to-go status can cut a significant amount of time.
- Make adjustments prior to the changeover: Consider using duplicate jigs for performing alignment and other adjustments before the changeover process begins.
- Equipment modification: Modify equipment to make it safer to perform tasks (like cleaning) while the machine is running.
- Modularize equipment: Equipment portability and customization can reduce the number of interfaces or interactions, resulting in significantly faster changeover times. For example, designing equipment on skids can make each piece highly mobile.
Once this step is completed, you should be left with a new list of changeover elements that includes fewer internal elements and more external elements which are performed either before or after a changeover.
Step 5 – Streamline Remaining Elements
How can this element be done in less time? Or, how can we simplify this element? Finally, your SMED team should review the remaining elements on your list with the focus of simplifying them so they can be done in less time. Since the goal is to reduce changeover time, give priority to internal elements before moving onto the external. Use a cost/benefit analysis to prioritize the remaining steps.
Some of the easiest ways to streamline elements include replacing bolts with quick-releases or other functional clamps, eliminating adjustments by standardizing numerical settings, using centerlines and shims to standardize die sizes, cutting out motion by adjusting the layout of workspaces, standardizing hardware to use fewer tools, and reducing wait times.
Another technique for streamlining processes is to create simultaneous operations. Just like a NASCAR pit crew changing a tire, multiple operators can perform a task simultaneously. Pay close attention to hazards and safety issues and ensure work is carefully choreographed and standardized.
Once step five is completed, update your standardized work instructions for the changeover.
Factors to Consider While Implementing SMED
While nearly every company that deals with changeovers can benefit from SMED, it's important to look at where productivity time is being lost to determine whether it should be your top priority. This is done by analyzing hard data, such as overall equipment effectiveness (OEE), specifically the OEE loss categories as they pertain to the six big losses. Collect this data for a couple of weeks to get a snapshot of where time is being lost. If you notice that changeovers comprise at least 20 percent of this time, SMED might be a good process to implement. If not, you might want to focus on total productive maintenance processes.
- Capture a baseline. Consistently measuring changeover time is critical, so you need to define how you'll measure it. According to lean manufacturing publisher Vorne, "Changeover time is measured from the last good part of the previous job at normal production speed to the first good part of the net job at normal production speed." Once you've defined how to measure changeover time, create a baseline by recording video of a normal changeover.
- Ask questions. Having an inquisitive mindset and asking how every element can be made external is the best way for SMED teams to approach the process. The following questions can help your SMED team achieve this mentality:
- Separate: Can this particular element be done with minimal to no change while the machine is running?
- Convert: How can we convert this internal element into an external one?
- Streamline: How can this element be simplified, streamlined and completed in less time?
- Standardize best practices. With the implementation of SMED comes a concern that machine operators will tend to rush through the changeover process, putting quality and safety at risk. The most effective SMED programs standardize processes and procedures by using things like single-point lessons for continuity in quality and safety. Treat instructions as living documents by having a process in place to continuously update them as needed.
- Focus on human improvements. Implementing an SMED program should require you to consider two categories of improvement: a human category, which is achieved through organization and preparation, and a technical category, which is attained through engineering and optimization. Ensuring the human factor is in good shape not only is faster but also less expensive, as human improvements are made during setup time as opposed to implementation time/effort.
Human improvements can be made by defining roles, metrics and accountability; offering training, coaching and brainstorming sessions on immediate improvement ideas; and creating standardized work instructions. Other human factors include keeping parts near the changeover areas at all times, labeling known equipment settings, and eliminating waiting and unnecessary motion.

SMED Pitfalls to Avoid
For a successful implementation of an SMED program and for these concepts to work, teams should avoid a few common pitfalls.
- Failure to organize: At least half of reducing changeover times revolves around better organization. That's why step three of the implementation process – separating external elements — can cut changeover times in half. After you've done this, it's time to get organized.
Your SMED team should address who will perform these external elements. Should it be an operator? A dedicated setup person? A combination of the two? The answer most likely depends on the types of processes and external activities. For example, most modern presses are highly automated, so an operator will be able to perform all the necessary activities. If you have more traditional machines, multiple people may be needed to complete the required duties.
Organization also means effectively rearranging the areas around the equipment so it's optimized for minimal motion. This involves setting up storage areas to make tools and material more easily accessible and applying point-of-use storage concepts wherever possible. Staging areas for dies and other materials should be identified nearby and ready to go for the next job.
- Not standardizing new processes: Failure to standardize the new-and-improved changeover processes results in highly variable outcomes that are dependent on the individual doing the changeover. One person might be able to perform a setup quickly, while another might take much longer, needing multiple tries to complete the setup.
Everyone should know the best sequence of events for each process. Standardizing a changeover process should be a team activity where everyone involved in the setup is fully engaged. Standardized procedures are particularly important when more than one person is working on a changeover at the same time. This coordination is sometimes referred to as the pit crew ballet, where multiple jobs are performed with precision simultaneously.
- Failure to maintain equipment: Studies have shown a strong correlation between changeover times and equipment condition. Setting up a poorly maintained piece of equipment is more difficult than the alternative, as more experienced or highly skilled employees will be needed, and achieving the required accuracy will be challenging.
Maintenance technicians are often seen as overhead, and their numbers have been reduced in efforts to cut costs. In some cases, the desire to keep equipment running has trumped preventive maintenance from being performed. This can result in a run-to-failure maintenance practice, which can have serious ramifications on equipment condition and lead to longer changeover times.
- Making unnecessary equipment investments: Companies frequently try to gain more flexibility by purchasing new equipment or technology – most likely to add more capacity. While doing this might be worth considering, it is crucial to ask whether it's necessary.
If you will be investing in new equipment or software, be sure to consider the different skill sets required to operate the assets. If insufficient training is provided or there is a lack of manpower to operate the equipment, you probably won't be reaping the full benefits of your investment.
Another thing to keep in mind is that not all equipment manufacturers take SMED into account when designing assets. This leads to a more complicated changeover, particularly with highly automated operations where multiple processes are combined into one line.
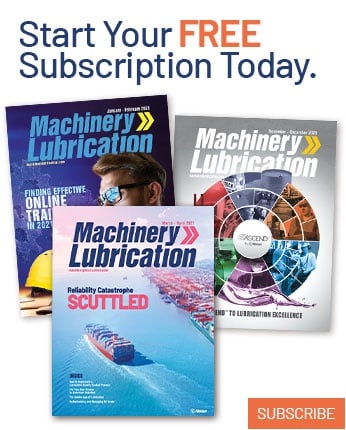