This case study takes place in a packaging facility. The packer on Module 8J0 was checked for vibration integrity during a pre-machine care evaluation. A problem was detected in the folding arm gearbox. The frequency characteristics indicated that a bearing was deteriorating.
This photo, taken with a fiber-optic camera, shows damage to the packer's roller bearings.
This seems straightforward, but is it? The gearbox is located in a section of the packer that is not easily accessible. The necessary repairs require separating the two sections of the machine. When the packer is split, it will take an additional two days of work before the unit can be restored to service.
In this case, the maintenance leader does not believe in the technician's ability to make a vibration call correctly. He has vowed to bring the technician and the technician's boss under the scrutiny of leadership for poor performance if the vibration assessment is wrong.
The added pressure from the maintenance leader has caused the vibration technician to look for other means to confirm the call to replace the gearbox bearing. The original call was based on a vibration signature that showed a frequency peak at 36.9 with harmonic side bands at amplitude of .10 inch per second (IPS).
This means that there is frequency where there should not be. The amplitude of this frequency by most standards is not considered to be a serious problem, and the machine was running fine. This is not a good set of circumstances to request repair work to be performed.
To be confident in the call, several steps must be followed:
-
Go back and look at the trend data on this particular gearbox. This was done and the data was taken on a regular basis (once per month).
-
Retrieve the packer's gearbox drawings and find out exactly what kind of bearing was installed in the gearbox, what it was driving, the particular gear that was installed, etc.
-
Explore other alternative tests that could increase the confidence of a correct call.
After looking at the drawing, it was determined that the bearing was a 1208 roller bearing. With this information, the technician could look more closely at the match of frequency placement to the characteristics of the bearing. The results were close but not exact. The frequency placement and the bearing characteristics were off by a small amount, adding some uncertainty about the original call.
The trend data had to be reviewed again. The frequency was so close and had all of the characteristics of a bearing based on experience. Reliability management was convinced the problem was a bearing that had doubled in amplitude for more than four months. If this gearbox were to fail catastrophically during operation, several million dollars would be lost in parts, labor and lost production opportunity.
The technician explored other tests to add confidence to the call and decided to use fiber-optic technology to take a visual look at the bearing. A monitor attachment allowed several people (including the maintenance leader) to view the test live as the camera was viewing the bearing.
The packer was shut down, the oil drained and the inspection covers were removed for access. There was just enough room for a smaller person to get far enough in to do the inspection. The results were conclusive as the visual images showed the damage on the bearing rollers (see photo).
The repair could now be completed with full confidence. When the maintenance crew removed the gearbox assembly, a thorough visual inspection was conducted to determine the failure mechanism. The results of the inspection revealed the cam driven by the gearbox had significant damage because the cam follower bearing had failed.
The closest gear to the gearbox had tooth damage, and the 1208 bearing that showed up on the vibration signature was a double roller bearing instead of a single roller bearing as the drawing had indicated. This explained why the frequency placement didn't line up. The primary failure was the cam follower bearing. The secondary failures were the 1208 bearing damage, cam damage and gear damage.
After the work was completed and the equipment restored to service, the lessons learned were explored. These included the following:
-
The trend data was critical in making an accurate call.
-
There are two different roller configurations with the same stock number in the stockroom.
-
The cam follower bearing was too delicate for the service it provided.
-
The maintenance leader is now confident in the technician's vibration calls.
-
Other reliability tools, including a fiber-optics camera, should be purchased for the facility.
The job of the reliability department, as far as this writer is concerned, is to "trend, trend and trend." The understanding, documentation and sharing of the reliability lessons learned are the future of a company's success.
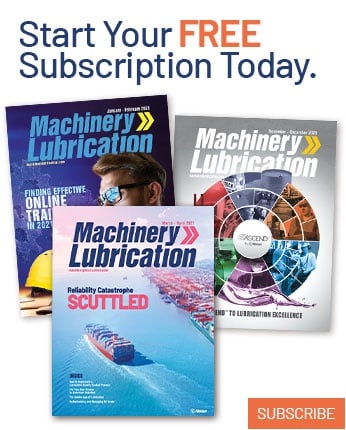