Reliability-Centered Maintenance (RCM) is a systematic method of developing an optimized maintenance policy for a physical asset. Born from the aviation industry, where it is very effective, RCM has gained popularity within the manufacturing and process industries.
While some have succeeded in deploying it, many others have been disappointed or become frustrated with the tedious process and given up altogether. I believe we need a fresh approach.
If you've read my previous Exponent columns or attended my workshops, you're aware of my preference for a more holistic approach to plant reliability management. For example, I've targeted the overall equipment effectiveness (OEE) metric, proposing instead a more encompassing view - overall business effectiveness (OBE).
Unavailability and quality and yield losses can result from equipment issues (such as scheduled and unscheduled downtime), production issues (product changeovers or supply chain disruptions) and/or marketing issues (low demand or overselling the plant's capabilities). OBE better reflects the true nature of the business and enables managers to target waste elimination areas with precision. We need to take a similar view with RCM.
Getting down to the nitty-gritty, the problem with RCM in industrial facilities is two-part: it's predominantly based on conjecture and it's one-dimensional.
In the commercial aviation business, RCM is applied based upon extensive testing to understand a component's failure rate, failure modes, etc. "In God we trust; all others bring data" is the aviation reliability engineer's mantra.
Lacking data about the nature of failures, most industrial reliability engineers must rely upon a great deal of guesswork when completing the failure modes and effects analyses (FMEAs) required to carry out the RCM process. As such, our results are typically biased based upon the individuals performing the analysis, the most recent failure modes, politics, etc.
Perhaps of more concern is that RCM, almost by definition, limits your reliability improvement efforts to maintenance. What's the problem with that? Well, in the aviation industry, the creation of the maintenance policy presupposes that the equipment is designed to be reliable and maintainable and that reliability and maintainability have been measured and quantified to assess risk.
Few industrial plants can boast the same. Likewise, RCM, as it is applied to the commercial aviation industry, presupposes that equipment is operated to exacting and procedure-based standards. Again, this is rarely the case in industrial manufacturing and process plants.
In the plant, reliability problems that may adversely impact availability, yield and/or quality can be caused by any of a number of factors. Why limit your reliability improvement initiatives to maintenance?
RCM, if done correctly, is based upon an FMEA or a failure modes and effects & criticality analysis (FMECA). If you're going to go so far as to create a failure modes-based risk profile for your plant, why would you limit your risk-mitigation measures to maintenance?
In many instances, changes in supply chain reliability, operations, sales and marketing, design, etc., will yield more reliability improvement than any changes strictly to equipment maintenance.
Here are a few examples illustrating where RCM misses the mark.
Supply chain disruptions: If your raw materials supply chain is disrupted to a sufficient degree, availability will suffer. How can we pin this on the equipment? Can you describe a maintenance policy change that will correct this problem and mitigate the risk?
Excessive customization: If your sales organization commits the company to a high degree of customization - which extends the time it takes to complete a product changeover, increases the frequency with which product changeovers must be completed and/or increases the amount of time required to stabilize production - it's tough to come up with an equipment maintenance strategy that will offset this risk.
Misoperation: Suppose that your operations team is simply operating the machines incorrectly and inducing failure. It's unrealistic to expect that a change in maintenance policy will offset this risk.
I could create dozens of other examples, but you get the point. The bottom line is that the logical process that we call RCM works, but limiting it to equipment and changes in maintenance policy is naïve. Risks can be induced by many other factors.
If you're going to subject yourself and your organization to the arduous process of performing an FMEA/FMECA, you must think holistically. Be sure to take a balanced approach when mitigating your operational reliability risks.
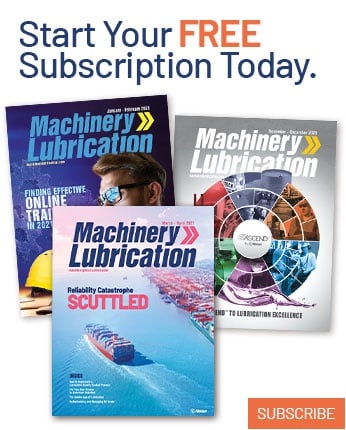