My last two columns have explored the five stages that condition-based maintenance programs go through as they grow and mature - starting with Level 1 plants that do very little CBM and moving to best-practice programs at Level 5. This time, let's look at the relationship between CBM and reliability engineering support.
The criticality analysis: Everyone knows that having a good criticality ranking is important in maintenance. Yet, you'd be surprised how few plants do this the right way. Ultimately, it's criticality that helps you determine which assets should be in your CBM program and how work orders get prioritized.
A big problem, though, is that many companies use the ABC approach to criticality - where equipment is assigned an A, B or C ranking.
A compressor might get an A while the lunchroom refrigerator gets a C. That's the easy part. But, the reality is that the majority of equipment falls somewhere in the middle and gets a B. So at the end of the day, when it comes to priorities, which B are you going to work on first?
That's why you need a single score and overall ranking for each asset. That gives you the level of granularity you need to take the guesswork out of decision-making and the confidence to know you are working on the right assets at the right time.
In truth, criticality rankings should consist of a composite score based on factors such as safety, the environment, maintenance costs, and the impact on throughput and quality. That means getting agreement from people not just in maintenance, but in production, purchasing, safety, accounting and marketing.
Are you reporting asset health?: A true understanding of asset health is the best indicator for reliability. But for top leaders to take asset health seriously, it must be standardized, meaningful and repeatable.
In the past, asset health has been a philosophy. Today, we can run a battery of CBM tests to determine whether an asset is healthy or not, plus we have the software necessary for reporting and scorecarding.
As a result, it's never been easier to get a true picture. Top CBM performers report asset health for all of their equipment according to consistent standards.
Failure isn't final: You can't change failures after they occur, but you can change how you respond to them. That's why handling failure investigations is one of the biggest differences between successful and unsuccessful CBM programs.
A CBM manager from a big chemical company wrote: "We don't spend enough time on eliminating defects. When you write up the same piece of equipment 19 times in one year, and make no proactive effort to eliminate the cause, your program is not focusing on the right things."
A failure is an opportunity to learn something, such as what happened, why it happened and what changes to make so it won't happen again.
In level 1 and 2 programs, a formal, documented failure investigation is a rarity. In Level 3s, you see limited root cause analysis done on the most expensive failures, and a few employees are trained in the RCA process.
At top-level CBM programs, you'll find established triggers for failure investigations according to factors such as cost, number of failures, operational impact, etc. These investigations may include experts from the supplier or OEM.
The process is well-documented and published when complete. Many employees are trained in RCA and metrics are in place to measure the results. At which level are you?
Considering each level's characteristics, where would you place your CBM program?
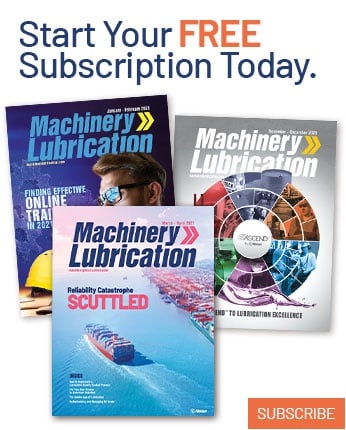