In this column, I hope to influence you to think about our old friend overall equipment effectiveness (availability x yield x quality = OEE) in a different light.
As an educator and consultant in the field of reliability management, I've observed that most organizations struggle to define their version of OEE. In particular, they have trouble with availability. In some instances, defining quality is challenging, but that's a topic for another column. Availability is our focus here.
Within the field of reliability engineering, there are several technical definitions of availability, which I'll not bore you with here (e-mail me if you'd like to see these definitions). But with few exceptions, for business purposes, availability is the number of hours you are running in a year divided by 8,760 (the number of hours in a calendar year).
In other words, availability is total equipment, line or plant running time divided by total elapsed time. For a manufacturing firm, availability and yield determine how much product you have to sell.
So, where do things go wrong? In a nutshell, we fiddle around with the denominator of the availability and yield equations, which may make us feel better about how we're doing, but it compromises the validity of the metric.
It's a bit like supporting part of your weight on the bathroom counter as you step on to the scale to weigh yourself in the morning. The number looks nice and may make you feel good, but our trousers still feel tight around the middle.
The fact is, when you reduce the denominator in the availability equation by one hour, you're proclaiming that the management of that hour is and always will be completely out of our control.
Only the occurrence of "acts of god" - like hurricanes and floods - are completely out of your control, and those can't really be factored into the plan. Moreover, your preparedness for such events will to a large extent determine the extent of the damage and the speed with which you recover.
For discussion purposes, I've outlined three common mistakes that organizations make in eroding the denominator of the availability equation. After which, I propose a more all-inclusive model for OEE that more accurately reflects the firm's entire business.
To accurately address problems, availability, yield and quality defects must be classified as market-, production- or equipment-induced.
1) Marketing downtime: Many organizations fall into the trap of convincing themselves that if the plant is available to produce product, but the market doesn't want to buy the product it makes, those non-productive hours shouldn't count against OEE performance. OEE, along with cost management, drives your profit, which in turn drives return on net assets (RONA), your firm's primary measure of management effectiveness.
While marketing downtime might not reflect how you're doing from an equipment reliability perspective, it's certainly important to the business. You see, if your plant remains in an undersold position, returns, relative to the net assets required to produce them, will suffer, and shareholders and prospective shareholders (investors) may decide to take their money elsewhere.
We may need to modify our marketing strategy: make different products, promote them differently, evaluate our pricing strategy, etc. Or, if we find that we can't address the marketing issue, we may need to reduce the net operating assets in place (the denominator in the RONA equation).
While marketing downtime isn't specifically an equipment issue, it is naïve to suggest that it doesn't affect the business. It's certainly not free. A notable exception to this rule is the military, whose mission is operational readiness to defend the country, not active fighting (the equivalent of production).
2) Production downtime: This, for example, is the time it takes to retool/adjust for a product changeover, for equipment cleaning and decontamination, and for regulatory checks and inspections.
Failure to capture product changeover limits the OEE metric's ability to reveal opportunities to streamline the changeover process with single-minute exchange of die (SMED) analysis, or to improve shutdown and/or startup procedures that cause equipment problems or destabilize the production process.
Cleaning and regulatory inspection time often sneakily erodes away the validity of our availability measurement. We get drawn into this due to our near-term lack of choice. For example, food processing plants must clean the plants to decontaminate them and assure food safety.
However, when you discount the denominator, you reduce your motivation to search out technologies and strategies that can enable you to run more hours without compromising food safety. In other words, by changing the denominator, the lack of choice is psychologically made permanent.
3) Planned maintenance downtime: While it's less common today than it was 10 years ago, many firms still fall into the trap of removing scheduled downtime from the production plan in the availability equation. This is analogous to proclaiming that scheduled and planned maintenance downtime is free.
It's not! For certain, planned downtime is typically preferable to forced downtime. We want to count those hours against our availability measurement to inspire the organization to think creatively to implement proactive measures that reduce the need to perform maintenance, improve planning and shutdown work management practices, and improve design for maintainability. That way, we can transition more tasks to run-time activities and improve the speed with which we complete downtime maintenance.
So, in reality, overall business effectiveness (where OBE = yield x availability x quality) is mathematically identical to overall equipment effectiveness (OEE). However, it is reflective of a more holistic view of your business in that availability reflects your firm's overall performance relative to perfection, as it should be. Here is a more modern general equation for plant availability measurement:
(Dm + Dp + Def + Dpm)
Where:
Dm = Marketing downtime
Dp = Production downtime
Def = Equipment forced downtime
Dpm = Planned maintenance downtime
Measure each of the four downtime components individually so you can address opportunities and threats. Moreover, develop a standardized taxonomy for defining the nature of a downtime event in each of the categories.
I've focused this column primarily on the availability factor of the OEE metric. However, the logic is applicable to the yield factor and, to a lesser extent, quality. I encourage you to classify instances where production yield is reduced into market-driven, production-driven and equipment-driven categories so you can more effectively address the underlying root causes of production slowdowns. Talk internally about how to break down your quality defects relative to the specific characteristics of your industry.
Metrics, when they are valid, enable us to identify threats and opportunities, and make more effective decisions. When we compromise the validity of the metric for "feel good" purposes, we're not doing ourselves or our stakeholders any favors.
Keep the metric pure and set about the business of being the best plant you can be - with an unrelenting focus on economically justified reliability improvement.
Also, forget about broad claims about what constitutes "world-class OEE" that are often espoused as general goals. While these may be valid averages, what and who is average? I've seen these so-called benchmark numbers ranging from 80 to 90 percent - an OEE that is absolutely unattainable in some industries without compromising the metric itself, and at the same time constitutes extremely poor performance in some other industries.
Pursuit of these so-called benchmarks causes some organizations to manipulate the metric and others to become dangerously complacent. Metrics are here to serve us, not us them. Keep your OEE (or OBE) pure, valid and real, then focus your energy on running the plant.
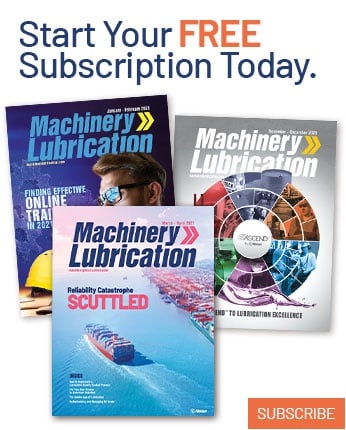