When I first got involved in the enterprise applications market in the early 1980s, no one was trying to measure overall equipment efficiency (OEE) – or even talking about it. Most companies in asset-intensive industries had only their homemade maintenance management applications running on mainframe computers. But over the years, as competitive pressures increased and manufacturers started looking for ways to improve the cost-effectiveness of their operations, smart managers realized that maintenance is not a standalone activity. It is a function that must be integrated tightly with production, business performance and other elements of the enterprise to reduce costs, and maximize productivity and quality.
When IFS and other enterprise application vendors started offering standardized enterprise asset management (EAM) and maintenance, repair and overhaul (MRO) tools, end-users approached these tools as strictly maintenance-focused. But after running these maintenance management systems for a period of time, they naturally found new ways to improve maintenance and operations, and learned to benchmark things so they could optimize maintenance activities by performing various functions at the right time and in the right way. As this maintenance data was collected and analyzed, the correlations between maintenance and other parts of the manufacturing organization became apparent.
In time, EAM system users learned that, to optimize their maintenance and operations activities, they also needed to optimize the design of their plants. It became necessary to integrate systems for design and engineering with EAM. In the years that followed, the dynamic connections between production, maintenance and engineering became clear. By the beginning of this century, many manufacturing and maintenance professionals had a fundamental idea of what needs to be done to improve the effectiveness of the overall operation through an aggressive OEE program. But even today, few companies have implemented a thorough OEE system. In many cases, equipment operation information, maintenance records and business performance data are still in separate data silos and cannot be integrated. In other cases, the silos have been partially eliminated, but processes and interfaces have not been implemented to enable collaboration and effective data sharing between manufacturing operations, maintenance and financial management.
Tighter integration for greater profitability
The need for ERP/OEE integration is driven by that fact that, in asset-intensive industries, the importance of capturing real-time information cannot be underestimated. Although at one time there were walls between automation information and EAM systems, these worlds are now melding together. Greater integration became possible with the introduction of OPC, a communication standard based on Microsoft’s OLE COM and DCOM technologies. OPC defines standard objects and protocols for use in process control and manufacturing automation applications. These protocols enable enterprise resource planning (ERP) providers to provide integration points between their enterprise-wide systems and plant-floor automation technologies.
OPC lets automation tools from major providers such as ABB, Siemens and Rockwell Automation communicate with other systems using a standard language. It is now much easier to tie in with other systems’ information about how equipment is operating, at what speeds it is operating, when stops and faults occur, and the dynamic factors that lead to stoppages and slowdowns.
Although the technological walls have been broken between automation, operations and maintenance, business practices that would enable companies to truly benefit from this newfound freedom have been slow to change. By working with leading-edge companies, I have personally seen how forward-thinking manufacturing and maintenance professionals can work more closely together not only to maximize uptime and productivity in their organizations but also to increase customer satisfaction and boost profitability.
Challenges of implementing OEE
The main challenge in launching an effective OEE program is that OEE tools and processes must encompass many different roles and disciplines in the company. The program must hold up to daily use by the production line operator, allow for analysis and follow-up by manufacturing professionals and management, support maintenance technicians and design engineers, and fulfill many other functions throughout the plant.
In the past, plant-floor-oriented OEE systems united multiple equipment databases and provided a good interface that allowed operators to view data on the operation of automated components and equipment, but they were still missing the integration to the EAM or ERP world. Other OEE products offered OEE as an add-on to the maintenance management application, but did not capture any of the data and business intelligence contained in real-time equipment operations records.
Real-time information for improved decision-making
Think of things for a moment from the standpoint of a production line operator. Imagine coming in for the start of your shift after being home over a long three-day weekend. You need to quickly get an update of what has happened in your absence. Have there been specific problems that might reoccur? You might find records from the previous shift in a logbook or in hand-scrawled notes. But these notes can provide only a limited amount of data and, by their very nature, cannot capture the insights of those staffing the plant in the operator’s absence. When data on equipment operation is collected automatically and refined by the operator, the quality and quantity of data – and the ability to view it in ways that are meaningful – are greatly increased.
In researching maximum OEE functionality, IFS found that, after switching from manual to electronic event recording, the number of stoppages, slowdowns and other events recorded for two production lines increased from 5,000 events per year to 300,000 events per year. Equipment slowdowns, in particular, can be subtle and often can be detected and interpreted only by digital real-time information capture.
The fact that this volume of information contains valuable business intelligence is undeniable. But organizing this massive quantity of information in a way that makes sense and suggests changes in the decisions operators and managers make is one challenge that must be surmounted. The results of human/computer interaction (HCI) research suggest that visualization tools are essential for manipulating and interpreting large quantities of data. Timelines and tree maps are especially effective in allowing plant operators to distill usable information from hundreds of thousands of operational metrics.
Once we discard the printed logbook in favor of information captured digitally in real time, the operator need not see only the notes of the previous shift – or even the shift before that. An entire data history is available in a format that allows for easy access and interpretation to optimize the shift. The ability to evaluate data over a longer period is essential if OEE is to improve over time.
An operator might look at a month of OEE data and find that quality dipped significantly – or unplanned stoppages increased – when equipment was operating near maximum capacity. Based on this data, the operator could find that it actually makes sense to reduce speed to optimize the output. Data will sometimes reveal that reducing production speed prevents breakdowns and unplanned stops, and sometimes positively affects the quality of the end product. But establishing the optimal combination of speed, quality and uptime requires excellent data analysis tools that the equipment operator can easily use. This information is also available to people working on continuous improvement initiatives in other parts of the organization, presenting an even greater opportunity for increasing profitability.
Putting it all together
Although the technological barriers between maintenance, manufacturing and business performance systems have fallen, these barriers, in practice, often still exist. But many organizations have taken the first steps toward collaboration between operation and maintenance. Their EAM applications are used by production to issue work orders, fault reports and technical data about the equipment. For example, when a pump breaks down, OEE notifies maintenance automatically. Later, the EAM system tracks the maintenance department’s progress toward completing the work order. Fault report data is reviewed to spot trends pointing to the need for preventive maintenance. When operations personnel take an active part in the execution of the EAM system, an easy-to-use interface, well integrated into the ordinary process portals on the shop floor, is extremely important.
The ideal OEE application also enables financial and business management to pull essential data from the ERP system, marry it to data in the OEE system, and make the information available to the rest of the organization. Management can analyze how maintenance, manufacturing operations, personnel activities, raw materials and other factors contribute not only to OEE but also to productivity and profitability. This data can be used to drive decision-making throughout the organization on either an ongoing or a case-by-case basis.
Here is an example of how ERP/OEE integration can be used on a case-by-case basis: Let’s say your company is operating a test run for a new customer, and quality is a priority. Perhaps additional maintenance can be performed before the run, or speed on the run can be reduced to improve the consistency of the end product.
On an ongoing basis, an integrated ERP/OEE system can play an important part in getting information from different management levels for use in production and maintenance decision-making. Total OEE, production throughput and end quality are only some of the criteria used in production decision making in an optimized manufacturing organization. Data from a workforce management system can be used to track patterns of productivity given the experience level, training and capacity of the staff on each shift. Supply chain management data can track how raw materials from different suppliers contribute to OEE, for example, whether a particular material results in a higher frequency of unplanned stoppages, slower equipment speed or higher scrap rates.
Data for these analyses can come from finance, maintenance, manufacturing, supply chain management, workforce management or customer relationship management systems. All of it must be linked to determine whether the number of faults, stops and slowdowns is being influenced by the people operating the equipment, the maintenance program that supports the equipment, the design of the plant or equipment, the materials being run through the equipment, or other factors.
Conversely, management needs to understand the inner workings of the manufacturing operation and maintenance to budget intelligently for maintenance and capital equipment – and to plan appropriate staffing levels, training and production forecasting.
In the next few years, I predict that more and more manufacturers will close the gap between ERP and OEE. The technology is already available to do this, but more manufacturing professionals need to be made aware of the importance and underlying potential presented by this fusion of departmental information.
OEE, the next generation
Meanwhile, the next level of OEE operations is already in the offing. At IFS, we are working with several major manufacturers in workshops to determine how OEE can be transcended. As even more information about customers, quality and the supply chain is married to OEE data, we are finding that plant operators, at some point, may be able to allow OEE to take a back seat to profitability. For example, let’s say that a company has used its OEE data to schedule maintenance. However, a transcontinental ship is waiting for the next run of goods to come off the production line, and the manufacturer has been given a financial incentive to make the goods available on time. In this instance, it might make sense to delay the planned maintenance long enough to execute the production run in time for shipment.
Today, various shifts in a manufacturing facility can track their uptime and productivity, and engage in healthy competition as they track these metrics. As technology evolves, manufacturing shift leaders can track their financial returns and compete on the basis of profitability. The priority today is maximizing OEE, and using all the tools and capabilities offered by modern ERP systems. The priority tomorrow will be using OEE and ERP together to maximize profitability.
About the author:
Ulf Stern is one of the co-founders of IFS AB, a world leader in component-based enterprise applications. Stern is IFS’s primary expert on EAM and maximum OEE, and is intimately involved in developing the next generation of these technologies in cooperation with major manufacturers around the world.
About IFS
IFS, the global enterprise applications company, provides solutions that enable organizations to respond quickly to market changes, allowing resources to be used in a more agile way to achieve better business performance and competitive advantage. The company was founded in 1983 and now has 2,600 employees worldwide. IFS has pioneered component-based enterprise resources planning (ERP) software with IFS Applications, now in its seventh generation. IFS Applications provides extended ERP functionality, including supply chain management (SCM); enterprise asset management (EAM); maintenance, repair and overhaul (MRO); product life cycle management (PLM); customer relationship management (CRM); and corporate performance
management (CPM) capabilities. For more information, e-mail info@ifsworld.com or visit www.ifsworld.com.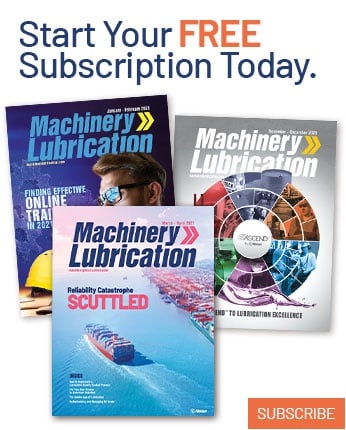