Brian Kenny, a plant manager at Paulco Inc., had a good problem. He had just gotten off the phone with Randall Tinsley, the company's vice president of operations. Mr. Tinsley had let him know - in enthusiastic and optimistic terms - that Paulco had a great opportunity to achieve a sales upside of 15 percent this quarter, if it could deliver quickly. As the VP said, "These are the moments that make careers!"
"Make careers?" Brian mused to himself. "How about making shipments?"
The increased shipments were to start within a month.
Figure 1. The components of OEE are availability, performance and quality.
In his plant management role, Brian always relished a challenge. Unfortunately, this relish also had some mustard, ketchup and sauerkraut thrown in. He quickly counted three problems standing in the way of increasing Paulco's revenue by 15 percent:
1) He was maxed out on equipment capacity.
2) There was no time to buy and install needed equipment.
3) And, there was no time to hire and train new people.
Other than that, he was in great shape.
"How am I going to get more out of what I have?" he ruminated. "I'm already handing my people excessive overtime and the machines always look busy. Yet, somehow, there must be some waste out there."
Brian remembered his plant had someone who knew how to identify and reduce process waste, but could this concept work well on equipment? He summoned the plant's resident lean principles expert, Linda Amoroso, to assist and explain the situation to her.
"Yes, I understand," said Linda. "But often, even busy-looking machines and operations have wasted and lost time that could be turned into positive output. The key is to improve the overall equipment effectiveness, or OEE, at key operations."
"Great. Another acronym. So, what is this OEE, and how can it help me?" asked Brian.
Linda took her cue. "OEE is a measure of how close to perfection a piece of equipment is running. Think of perfect OEE as if the equipment ran with no downtime, no idle time, no quality issues or no speed slower than the maximum."
"What fantasy world is that?" retorted Brian. "This is Paulco. We make things for a living - real things. Real … imperfect … things."
"Well, as you know," replied Linda, "lean often deals in absolutes, and so does OEE. It is an ultimate goal to be perfect. Several companies have achieved 85 percent of this perfection, and strive toward higher marks every day. But bottom line, OEE is the ratio between what was produced in a time period, say a week, vs. what could have been produced in the time period under the perfect conditions I mentioned earlier. Here, let me draw a picture." (See Figure 1.)
She explained that the availability efficiency is lessened when the machine is down and can't perform its intended function. The downtime can be unplanned, planned, changeover, etc. For desired down activities, it is the time that's the waste. For unplanned work, it's frequency and duration that are the wasters.
Performance efficiency is reduced when the machine is functional but idle (no work in progress, no operator, no fixture, etc.) or if it's slower than the maximum speed (the result of mechanical/electrical/software imperfections, minor unrecordable stoppages, under-batching, etc.). Quality rate is hit when there is rework, scrap or redo activities. The final OEE figure is determined by multiplying the Availability percentage by the Performance percentage by the Quality percentage.
"I can go into these equations if you … no? … OK," said Linda. "So you see, it's an optimization game. You can't maximize one thing at the expense of another."
"So, you're a lean person. How does all this relate to lean principles?" queried Brian.
"Good question. It certainly does," answered Linda. "Lean is about reducing wastes, and OEE is about the same thing - identifying wastes of machine time and reducing them. OEE measures the waste in equipment availability, performance and quality."
"OK," offered Brian. "I know for a fact we have problems with downtime and mysterious slowness. We never hit the speed we used to. Can we start there? But, tell me, can this OEE really make a difference?"
Figure 2. Comparing a company with 40 percent OEE against one with 80 percent OEE.
"Yes, it can," she said. "Let me show you here on the board (see Figure 2). Here are two companies, one with 40 percent OEE and one with 80 percent at key tool sets. The 40 percent company wastes its resources related to equipment. The 80 percent company uses them efficiently. I will write below the characteristics of each. Most companies look more like the 40-percenter, and we may look like it, too. If we could move from the 40 percent environment at least partially toward the 80 percent, we would have a chance at the increased output opportunity - without buying new equipment or adding people."
"So, how do we do this?" asked Brian.
"Let me tell you," started Linda.
At that moment, the phone rang. It was Mr. Tinsley, the VP.
"Didn't I just talk to him a few hours ago," Brian thought to himself.
After the call ended, Brian turned to Linda.
"He wants to meet right now on my approach for meeting our opportunity," he said. "Well, at least now I have something to tell him. Linda, let's you and I meet later today to continue our discussion. I want to know how we'll use an OEE and lean partnership to get this 15 percent."
Read Part 2 of this story: Spelling Lean O-E-E: The Next Day
Mike Verdin is a principal consultant with Aveus (formerly Supurna Solutions), a change and customer experience company located in St. Paul, Minn. Contact him at 480-231-3368, or mverdin@aveus.com. To learn more, visit www.aveus.com.
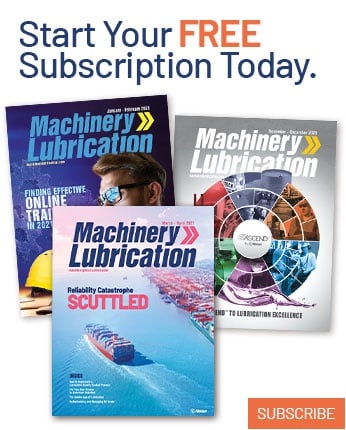