The next time you get into your automobile, you should take a moment and think about what it took to design, build and get it into your hands in the first place. As consumers, we’re familiar with the advertising that created our interest and the sales process that resulted in the purchase decision, but this is a very small fraction of the immense activities that went on before the vehicle was manufactured.
When it comes to making vehicles economically, it’s all about productivity, and that translates directly to the number of labor hours it takes to build each one. According to the 2006 Harbour Report for North America, the Productivity Gap between Detroit automakers significantly narrowed in 2006. In-plant quality improvements at all plants have been dramatic.
DaimlerChrysler improved assembly productivity by the largest margin (6 percent) and General Motors had five of the 10 best assembly plants in North America. Ford Atlanta came in as the best single assembly plant, but Nissan led all manufacturers with 28.24 labor hours per vehicle. It’s worth looking into how this was accomplished.
The enormously complex processes involved in building a new vehicle are best described as a "ballet," wherein several thousand parts come together on an assembly line. In not-too-many minutes, these parts are fastened together and at the end of the line a new vehicle drives off to be shipped to a dealer. To watch such an operation is both entertaining and awe-inspiring because it is choreographed so well that it looks easy.
It only looks that way as a result of millions of man-hours of effort directed toward the design and implementation of the assembly plant to ensure that thousands of vehicles – each one a different color with varying options – can roll off the line in unbroken succession, 24 hours a day.
Nissan’s Canton, Miss., plant is a very good example of how planning and execution come together effectively. Each year, the 3.5-million-square-foot factory is capable of producing a total of 400,000 new Altima sedans, Quest minivans, Pathfinders, Armada sport utility vehicles, Titan King Cab and Crew Cab full-size trucks, and Infiniti full-size sport utility vehicles. More than 4,000 workers are employed at the plant, where new people, four new products and a host of suppliers were all brought together to do what no auto plant had ever done before – build five separate products in the same building.
An aerial view of Nissan’s plant in Canton, Miss.
Before any of this can happen, however, a good business case must be made for a particular model with a decision to start the design process to follow. Designers must take into account the target customer, existing market, how many of the new models can be sold, the available plant capacity and an endless number of other issues. Nissan’s need to expand Altima production, along with its decision to enter new markets with the Titan truck and Q56 Infiniti SUV, led to investment in the new Canton plant.
The plant location was chosen after much consideration, but according to Frank Gallina, director of product quality and supply chain management, the most important factors were direct access to interstate highways, rail and water – the "trinity" of basic needs for any automobile manufacturing operation. Once these important decisions are made, a factory can be designed and built, but fitting it out is a very involved process that starts with the design of the vehicles themselves.
During the vehicle design phase, the chassis engineers and body stylists must interact with production engineers at the plant. Parts and subassemblies must be refined in design to make them "buildable," so that assembly technicians are able to put them together in an efficient manner. Otherwise, the process will be too slow or expensive and the cost of the product will exceed budgets.
Consequently, vehicles are designed to be as modular as possible. The 2,000 to 3,000 individual parts of a modern vehicle are built into discreet sub-assemblies to be brought together along the line. Complete dash assemblies containing all instruments – HVAC, sound systems, steering column, wiring and controls – are installed in minutes by technicians working almost exclusively outside the vehicle (having to crawl under a dash to connect wires and controls wastes valuable time and causes fatigue and muscular damage to the technician. So, great care is taken to design maximum comfort to line workers).
The worst place to solve design/assembly/component problems is at the plant level. That’s why today’s vehicle design depends a great deal on computer simulation and prototyping so that the goal of only needing one "hard part" trial is achieved. During manufacturer all important components receive diagnostic checks, periodic audits and sampling, all of which ensure product quality.
Drivetrains usually contain all the accessories, steering components and other associated items. On front-wheel-drive vehicles, the entire powertrain can be installed as a single unit into the body. Frame-based vehicles such as trucks and SUVs require different assembly techniques because the suspensions are mounted to the frame members.
The plant is set up in "workforce zones" that are comprised of a manager, leader (a trained technician who knows how to do everything) and the required number of workers. Interfacing with these groups are behind-the-scene individuals who write the service manuals, owners’ manuals and a host of other documentation specialists. These, in turn, are in constant contact with dealership service management to monitor warranty issues and investigate possible failure mechanisms in various components, so that necessary changes can be incorporated directly into the assembly line without interruption.
On-site suppliers are utilized at the plant. A number of OEM suppliers (front-end assemblies, wheels/tires, etc.) share walls with the production floor. This allows virtually instant communication with all facets of the production process and insures that the right parts are supplied at the right time. Other suppliers are located very close to the plant, usually within a few miles. Seats, plastics, frames and other components are manufactured and inventoried a very short distance from the production floor. Operating this way aids significantly in today’s just-in-time inventory business system. Off-site suppliers depend upon the rail and truck infrastructure to get all the components to the plant on time.
Just as a great ballet performance depends upon a large and complex behind-the-scenes coordination of musicians, stagehands, dancers, set designers, lighting technicians and a host of others, building a quality vehicle depends upon far more individual elements and significantly greater complexity. The final product, in either case, is very impressive and often quite beautiful.
About the author:
Les Jackson is a contributing editor for the American International Automobile Dealers Association. For more information about this organization, visit www.aiada.org.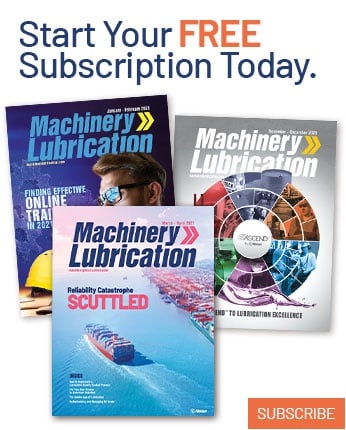