Power generation companies have implemented well-developed plans to improve equipment performance in terms of availability, reliability, efficiency and compliance. However, most companies have reached a performance plateau — undermining their ability to achieve corporate goals, objectives and strategies.
The problem is exacerbated by aging equipment; “right-sizing” initiatives; the retirement of skilled blue-collar workers; younger, inexperienced staff; and restrictive OEM service agreements.
The result is an equipment performance gap that inhibits corporate performance. In fact, when equipment fails to perform to expectations, it sends a shock wave throughout an enterprise — disrupting normal operations, maintenance procedures and financial performance.
For power generation companies who are looking to close the equipment performance gap, SmartSignal’s EPI*Center software solution enables operators to increase equipment reliability, availability, efficiency and compliance beyond their current plateau.
Unlike traditional condition monitoring tools like vibration monitoring, EPI*Center provides early, actionable warning of abnormal performance across all critical systems and operating states.
Challenges for the Best-Run Plants
To help understand the value of predictive analytics, the following is a sampling of customer-verified EPI*Center case histories. It is important to note that all of these power generation companies:
• Fielded rigorous preventative maintenance programs.
• Applied “state-of-the-art” condition monitoring programs, e.g. vibration monitoring, thermography, etc.
• Utilized “trending” programs consistent with industry standards on priority equipment throughout their fleet.
In spite of these programs and a well-trained staff, these operations found that equipment problems continued to occur on an unpredictable basis. As a result, these utilities decided to add Predictive Analytics from EPI*Center in order to receive early, actionable warning of emerging faults.
Predictive Analytics in Action
Each of the ensuing case histories describe a situation in which SmartSignal clients turned early warning into demonstrable value. In each case, the emerging problem was not identified by traditional condition monitoring or trending programs. The sampling serves to:
• Highlight the broad range of critical equipment for which EPI*Center provides predictive analytics.
• Give insights into the typical actions instigated by EPI*Center WatchList incidents.
• Detail the resulting value.
Lastly, the following case histories have been purposely selected to feature an array of fossil fuel plant equipment and issues. In all cases, SmartSignal Corporation clients have given approval to disclose these real-life occurrences on an unbranded basis.
Case Study #1 — Air Heater Support Bearing Problem
Problem: On December 22, high air heater support bearing temperatures began posting incidents to the WatchList — an exception-based listing of equipment and systems indicating abnormal performance.
More specifically, a fossil fuel plant’s secondary air heater support bearing temperature increased 40 degrees Fahrenheit above what would be considered normal for ambient temperature based on EPI*Center predictive analytics. This increase was not seen to be abnormal by any of the other plant systems, e.g., DCS, condition monitoring programs, etc.
Solution: Operators added 3.5 gallons of oil to this bearing (25 to 30 gallon capacity) and the temperature came back down and has been running normal ever since.
Benefits: The EPI*Center early warning of abnormal temperatures resulted in the addition of oil, preventing possible bearing damage. These bearings have a very tight oil max/min range and have been troublesome for the plant in the past. Previously, an air heater support bearing failed in July.
At that time, it took nine days to fix the problem, which resulted in 138,804 MWHs of lost generation. A similar support bearing failure would cost the company between $1.5 million and $4 million in lost generation alone based on current costs of lost generation at $10 to $30 per MWH.
Case Study #2 – Early Warning of Shorted Turns on an Exciter
Problem: A two-unit, 1,500-plus-megawatt-capacity plant began posting incidents to the WatchList on high exciter amperage. The deviations were 5 amps higher initially and then increased to 15 amps higher versus EPI*Center estimated norms (i.e., predictive analytics).
Solution: Based on this information, engineering staff believed that the exciter amperage increase was attributed to shorted turns in the rotor. In fact, the plant was approximately two weeks from an 80-plus-day planned outage to replace large portions of the turbine and rewind the generator — providing the ideal opportunity to verify the diagnosis.
When the exciter was inspected during the outage, physical damage was found on the exciter and shorted turns were found as well. The plant proceeded to have the exciter rewound during the outage.
Benefits: The EPI*Center’s early warning of shorted turns in the exciter was validated by the physical damage found during the outage inspection of the exciter.
Case Study #3 – Early Detection of Developing Bearing Issue on Turbine Generator Avoids Potential Outage
Problem: The customer runs a multi-unit generating station with 2,000-plus MW capacity. An abnormally high bearing temperature was detected on a turbine bearing on one of their units — a gas-fired, 420 MW General Electric steam turbine — by the SmartSignal’s EPI*Center low-pressure turbine model (one of several in the solution set).
The model flagged this as abnormal behavior even though the 14-degree increase was well within the normal temperature threshold. That same day, the PM&D Center informed the plant of the irregularity and the center continued to monitor the situation.
Six days later, EPI*Center detected another slight, but significant, step change in vibration for the bearing. Specifically, the actual sensor signal value was 1 Mil greater than SmartSignal’s “estimated value” during 24 out of 36 data samples. With this corroborating evidence of deterioration, a PM&D Center specialist recommended a more thorough evaluation of the bearing.
Solution: By coincidence, the unit was scheduled for a two-week planned outage for basic maintenance beginning about a month later. Due to the data from the PM&D Center, the plant performed an in-depth inspection of the bearing during the planned outage.
Since it was unscheduled, the bearing inspection would not have been part of normal plant maintenance without the predictive analytics from EPI*Center. Upon inspection, the bearing was damaged along with scoring of the shaft. Babbit material was replaced in the bearing and the journal was smoothed to rectify the issue.
Benefits: Without SmartSignal’s EPI*Center’s early warning of abnormal equipment behavior, the bearing would have continued to deteriorate. Most likely, this would have resulted in an in-service failure or forced outage in late April or early May, when demand begins to rise, leading into the summer season. Early detection also avoided impacting the company’s Peak Power Reliability Rating (PPRR).
Typical industry savings, at a minimum, range from roughly $503,800 to $655,000 depending upon the length of the outage. If the forced outage occurred during peak period demand, replacement power costs would have escalated dramatically.
Case Study #4 – Early Warning of Inboard Bearing Damage on a Boiler Feed Pump
Problem: The customer has a fossil fuel plant with 800-plus MW in capacity. Early warnings posted that the motor bearings on the boiler feed pump were rising in temperature. This warning occurred seven days prior to when the temperature readings would have reached an unacceptable level based on traditional monitoring devices.
Solution: A planned outage was promptly scheduled at a time most suitable to the plant so that the bearing could be replaced. This action averted an unplanned, forced outage that would have occurred given a catastrophic event with the pump.
Benefits: The customer was able to schedule a planned outage for replacement of the bearing at a time that was least costly in terms of generation revenue. In addition, the planned outage was conducted in a much shorter time frame, due to maintenance team preparation, compared to a potential machine trip.
Case History #5 – Early Detection of Loose Coupling on ID Fan D
Problem: On January 31, high ampere incidents began posting to the WatchList. ID Fan D was posting incidents to the WatchList, indicating high motor amperage.
Solution: Based on the predictive analytics, plant personnel initiated further analysis on fan loading. Fan loading was found to be no longer corresponding with blade pitch since previous work had been done on this fan. Personnel suspected this might be due to a problem with the Beck Drive, control linkage, servo and/or blading.
Benefits: Based on the EPI*Center’s early warning of abnormal current on the fan, the plant determined that this fan could be taken out of service and the problem investigated prior to the planned outage. The shaft-coupling setscrew on the fan side of the shaft was found to be loose and it was tightened prior to the outage. Had the fan been lost, a possible load reduction would have occurred.
Case Study #6 – Early Warning of Bearing Cooling Issue on a Circulating Water Pump
Problem: A single-unit generation plant with 700-plus MW capacity had bearing temperatures that began posting incidents to the SmartSignal WatchList in early February. The deviations were 20 to 80 degrees F higher vs. EPI*Center-estimated norms. The temperatures had not exceeded the normal operating range and had not yet initiated an alarm in the DCS system.
Solution: EPI*Center’s early warning of abnormal temperatures initiated an investigation that found that the bearings were being starved of cooling water, as water was being biased to an alternate pump. A new circulating water pump motor had been added and the cooling line had been modified for bearing cooling on the new pump.
It was found that there was a restriction of cooling water flow to the problem circulating water pump. The problem was quickly addressed with a temporary cooling line that resulted in the bearing temperatures coming down about 20 degrees F. A few months later, a new cooling water line was installed during a planned outage.
Benefits: The EPI*Center’s early warning of abnormal temperatures initiated an investigation into the reason for elevated temperatures on the circulating water pump.
Without the investigation and discovery of the restricted cooling to the pump bearings, the bearings and shaft could have been damaged. Taking this pump off during winter operation for bearing and shaft repairs would have resulted in increased backpressure and load reduction due to insufficient flow through the condenser.
EPI*Center is a software solution that provides owners and operators with predictive analytics using existing equipment data. By automatically analyzing all relevant sensor data — process, condition monitoring and electrical sensor data — EPI*Center provides early, actionable warning of emerging reliability, efficiency, throughput and compliance (environmental and safety) problems. Furthermore, EPI*Center:
1. provides early warning of equipment anomalies that other systems do not detect.
2. delivers this early warning across all equipment and operating regimens.
3. is quickly configured, deployed and delivering value.
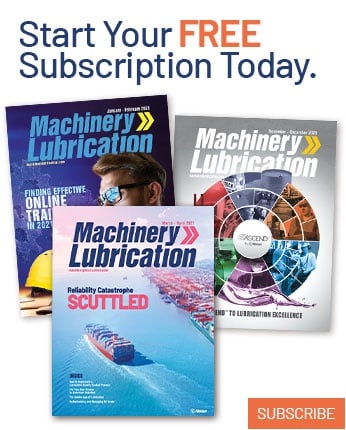