Most, if not all, companies use computerized maintenance management software (CMMS) systems to oversee their maintenance activities. From home-grown systems to complete enterprise resource planning (ERP) systems, leveraging technology allows companies to more efficiently and effectively manage their maintenance, repair and operations activities. So as a core maintenance function, surely routine, lubrication-related preventive and predictive activities such as regreasing motor bearings, taking oil samples, and executing oil top-offs and inspections belong in the CMMS system like any other maintenance task, right?
While at a strategic level this may indeed appear to the correct approach, such decisions can and often do present more problems than they solve. Take, for example, the simple act of planning and scheduling routine work. Unlike some maintenance tasks, lubrication occurs at the lube point level (e.g. drive-end bearing), rather than the component level (e.g. gearbox) or train level (e.g. conveyor system). Yet very few CMMS users elect, with good reason, to define their machine hierarchy to such a level of granularity. The reasons are many and varied, but the most obvious is the sheer number of lubrication tasks which need to be planned and scheduled, resulting in a proliferation of the number of work orders which must be raised, scheduled and closed.
For example, consider a medium-sized plant with 1,000 machine trains. Now let's assume that each train is fairly simple (e.g. the motor is directly coupled to a pump) and count the number of lube points. The total is three to five depending on the design of the system: a drive and non-drive bearing for the motor; the coupling (assuming it's lubricated); and drive and non-drive bearings for the pump, which may or may not be lubricated together (e.g. wet sump bath-lubricated system vs. individually greased bearings). Assuming an average of four lube points, and just one task (e.g. regrease bearings) performed on each point every six months, we are faced with issuing eight work orders per train per year, or 8,000 work orders per year. Now consider a "real" plant with more complex machine trains with more lube points requiring more PM tasks, and the total number of lubrication PMs per year can amount to tens and often hundreds of thousands of work orders per year.
CMMS system designers and users are aware of these problems, so most planning and scheduling modules allow for the assimilation of common tasks into groups - often referred to as lube routes, which may contain several hundred discrete tasks. Under this scenario, one work order can be issued for the route (e.g. six-month regreasing of motor bearings), greatly simplifying the tasks of planning and scheduling. But this in itself can create further problems.
For instance, consider trying to track PM compliance. By combining lubrication tasks into one macro-task (lube route) associated with one work order, users are often forced with a difficult decision. They may be unable to complete just a single task on the route, perhaps with good reason (e.g. the machine was running and inaccessible, or conversely, wasn't running but should be in order to perform the task properly). Should they leave the work order open, perhaps for weeks or months until they can complete the task, and achieve zero percent PM compliance for those tasks that have, in fact, been completed? Or, do they close the work order and get 100 percent, even though some activities remain open?
Though neither approach is correct, the most common is for the work order to be closed, virtually guaranteeing that the "missed" tasks will not get done until the next scheduled interval.
Even if all tasks are completed each time on every route, how likely is it that every single task will remain the same, and that the periodicity of the task will remain the same in perpetuity? For the "real" plant, work planning and scheduling needs to have a dynamic component, whether it be a planner actually evaluating work plans and modifying them to make the most efficient routes or utilizing a software-driven tool capable of dynamically adjusting workloads and task urgency. Under this model, work gets moved around to best fit the available time and resources.
However, by defining macro-tasks or lube routes, it may become necessary to rewrite work orders and move tasks around to account for changes in lubrication schedules, or to accommodate emerging or ad hoc tasks such as an on-condition oil change or unscheduled offline filtration event. Even worse, lubrication tasks are often unknowingly duplicated, resulting in a proliferation of unnecessary and sometimes harmful events, while others are missed altogether, as the shear number of tasks which need to be performed swamp the overworked, understaffed planning department. A recent Hartford Steam Boiler study estimated that up to 50 percent of all PM tasks are unnecessary.
For many reasons, a strong argument can be made to exclude basic lubrication PMs from the CMMS system. After all, what is the true motivation for including this work there in the first place? It's surely not to add complexity and administrative overhead to planning and scheduling maintenance work. Rather, it's to insure that pertinent data (such as accruing time spent lubricating specific areas of the plant) or asset classes can be applied to the correct cost center (maintenance accounting), and to track global metrics such as PM compliance (maintenance management).
However, with a well-developed system to capture and enter this type of data back into the CMMS, you are probably better served with a dedicated system, administered and managed by the lube team, and designed to handle the day-to-day minutia of lubrication. Leave the excellent planning, scheduling and work order management tools built into modern CMMS systems to do what they do best: handle major maintenance activities and serve as a repository of macroscopic management data.
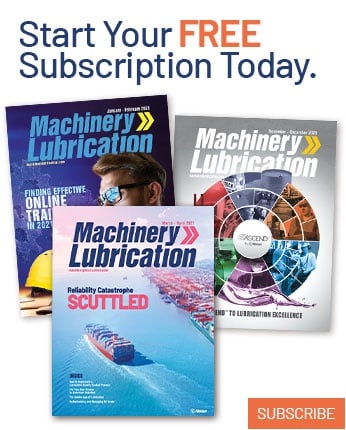