Chemical manufacturing plants are full of potential threats to the safety of your employees. Every day your workers are exposed to hazardous chemicals, which may lead to serious injuries or death.
Finding ways to reduce the risk of accidents and implementing fall prevention strategies are critical to workplace safety. To do this, it's essential to understand the types of injuries that occur in chemical plants and, most importantly, why they occur.
Common Injuries at Chemical Manufacturing Plants
Chemicals are toxic and highly flammable, making chemical manufacturing plants extremely dangerous. Common injuries that occur at chemical plants include chemical burns, trips and falls, overexertion, cuts and scrapes, chemical exposure, and inhalation of chemicals.
Causes of Accidents in Chemical Plants
Even when precautions are taken to reduce the risk of accidents in chemical manufacturing plants, they still occur from time to time. Knowing how and why accidents occur will help you take additional steps to prevent them in the future.
Here are three main causes of accidents in chemical plants:
Human Error and Complacency
Most accidents at chemical manufacturing plants result from human error and complacency, such as workers taking shortcuts or failing to follow safety procedures set forth by your company.
Improper Training
Shortcuts and workarounds are often the result of improper safety training. Train all your employees on how to operate safety equipment and follow proper loading/unloading procedures. Your employees should also understand what to do if something goes wrong and how to correct the problem before it gets out of control.
Not Properly Maintaining Safety Equipment
Installing safety equipment isn't enough. It is important to conduct regular maintenance at scheduled intervals based on manufacturer recommendations. When your equipment isn't properly maintained, it may malfunction and ultimately result in accidents when employees are working on and around the machine.
3 Strategies to Improve Fall Prevention
One fatal fall is enough to severely impact your business's bottom line. Here are three practices to help improve fall prevention at your chemical plant:
Install Custom Safety Equipment
Installing safety equipment is an important step in reducing the risk of injury at your chemical manufacturing plant. The right safety equipment goes a long way in keeping workers safe without sacrificing throughput efficiency. When choosing equipment, always focus on intuitiveness and accessibility of the solution. When equipment is too difficult to use, your employees will take shortcuts.
Train Employees on Proper Safety Procedures
Safety equipment is important, but it's equally important to train your employees on proper safety procedures, especially when hazardous chemicals are involved.
Make sure your employees understand the dangers of working with chemicals and the importance of wearing protective clothing at all times. Also, teach your team how to safely use fall prevention equipment. Include information on any challenges your team may face and how to safely overcome them.
Create Designated Loading/Unloading Spots
Falls and other injuries are more likely to occur when loading and unloading take place in an area without fall prevention equipment.
Create designated loading and unloading spots in your facility by installing custom safety solutions in those areas. Be sure to communicate this change with all employees, and conduct regular audits to ensure everyone is using safe loading/unloading procedures.
Chemical manufacturing plants are full of safety hazards. Even with safety equipment, employee training and proper safety procedures, an accident is likely to occur at some point. However, by understanding common workplace hazards and taking actions to address them, you can create a safer workplace for all your employees.
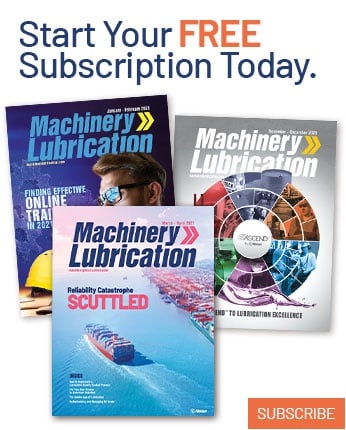