In our competitive environment, every manufacturer struggles to do more with less and to find capital for "nonproduction" areas, such as maintenance, safety, training, housekeeping and human resources. If done in a short-sighted fashion, the employer learns through painful experience the sacred law of "unintended consequences."
A recent magazine article detailed the harm to production and profits that resulted from gradually shifting almost all maintenance functions to production employees. You're probably thinking, "I wouldn't do that," but many employers have eliminated certain housekeeping workers and relied upon production employees to clean up their area or machine.
Let me share some of my experiences where "nonproduction" functions were neglected:
At one company, management of change (MOC) was overlooked as conveyors were modified and used machines and lines were added. Overstretched plant engineering and maintenance departments missed the new point of operation and other areas requiring guarding. Interlocks were not connected. Holes were left in boxes and panels. Lockout training was not updated. No annual evaluation of lockout was connected, and training was not revised. After an injured line employee complained to the Occupational Safety and Health Administration (OSHA), the agency issued hundreds of thousands of dollars in citations and penalties relating to guarding, lockout, training and electrical violations. Even worse, the company has significant "repeat" citation OSHA exposure throughout its many plants.
At another plant, the overall safety responsibility was shifted to a production supervisor (or maintenance or lab director, etc.), and the plant safety manager was laid off. The supervisor/safety manager responded to the loudest voice (the production manager) and the seemingly most urgent matters (getting product out the door). A worker was killed but not "directly" because of safety lapses (a poor safety culture was a factor), and OSHA learned that new hires had not received proper training. Written policies looked good until the company terminated the safety manager, so the decline in compliance was even more glaring. The poor pseudo safety manager was so underwater that he never acted on the recommendations from the last three yearly audits by the insurer, so OSHA cited the employer for numerous willful citations.
A third company didn't feel that it could retain additional experts and relied on its own staff and its general mechanical contractors to select and install new food production lines. These individuals were actually solid people, but they did not have experience with the process hazard analysis (PHA) experience in selecting and operating lines with combustible dust issues. After several hundred thousand dollars in OSHA citations and retrofitting costs, the organization now wishes it had spent the money on a full-time safety manager and used a consulting engineer with combustible dust experience to address system design and management of change issues.
These are safety and engineering-related "unintended consequences." Don't get me wrong. I embrace the lean movement and realize that sometimes you have to select the "least bad option," but you must also think ahead.
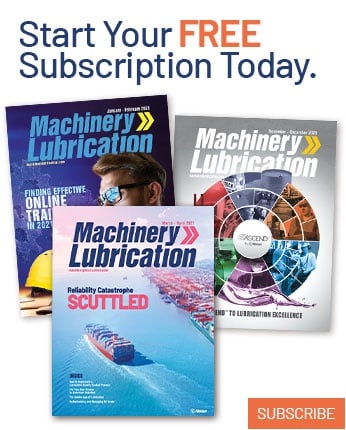