At the beginning of my career, I was trained on the shop floor as a change agent. I was part of a group of individuals selected to be coached by Toyota consultants. The organization had hired consultants to coach the team so we could disperse the philosophy, and we certainly did. We learned a great deal from the sensei, our continuous improvement manager and our plant manager.
We were originally introduced to three types of work: non-value-added, value-added and quasi-value-added. Value-added was the work that actually added value or something for which the customer was willing to pay. Of course, non-value-added was the waste. Then there was "quasi-value." The more I contemplate this third category of work, the more it troubles me.
I have heard other organizations and consulting firms use this term. It essentially translates as work that is "non-value-added but necessary" or "non-value-added but under current conditions must be done." I understand the definition of quasi to be "having a likeness to something or resembling something," so this classification of quasi-value-added is perplexing. How can non-value-added activity resemble, be similar to or even comparable to value-added activity?
The first reason I have to strongly disagree with the classification of quasi-value is the "under current conditions must be done" designation. For example, if an individual were to walk out to the gemba and observe a process, he is always viewing the condition in present time, in the current condition. He is certainly not observing a previous or future condition.
Second, this "non-value-added but under current conditions must be done" work would theoretically encompass every non-value-added activity in which an organization engages. Again, if an individual were to walk to the gemba, he would undoubtedly see waste. Depending on his waste-observation skills, he would more than likely identify a great deal of waste.
He may observe individuals walking, turning, unpacking, repacking, reworking, bending, twisting, reaching, cleaning, inspecting, etc., to complete the processes. Therefore, these activities must "currently be done" in the "current condition." All these activities have to be done until they are changed. Every one of them is just as deserving of the non-value-added classification.
Third, not only does the description of quasi-value-added make it nonsensical, but I also believe this classification can be damaging. In reality, it permits the defense of waste and ultimate acceptance of non-value work. As a continuous improvement professional, I want all waste realized and classified in the category it belongs – non-value, nothing more.
To be considered a valuable action, the action must conform to three main criteria: the customer must be willing to pay for it, it must transform the product and it must be completed correctly the first time. If the action does not conform to all three, it is not valuable. I find this to be proper, specific and rather cut and dry.
I have been in organizations that considered some inspections "necessary" or quasi-value-added. These inspections likely were in place because of a safety concern or possibly an adjustment that needed to be verified. This does not mean the process deserved a gray-area classification such as quasi-value-added. No matter how you spin it, the action is a non-value-added task. The inspection is not transforming the product, and due to the fact it is verification, it's not done correctly the first time.
I think value-added and non-value-added are black and white. The process element is either valuable or it isn't. I believe classifying an action in this gray area will eventually produce an attitude of acceptance.
It would be healthier for an organization to eliminate this quasi-value-added classification. Don't use a term to lessen the sting of what exists. Let it sting. Just because you cannot currently eliminate it does not mean that it should be classified in a defunct void of quasi-value-added.
Don't let an action get lost in the muck. If it's a non-valuable action, then call it non-valuable. Bring attention to it, let it be called by its unpleasant name and continue to research techniques, tools and methods to eliminate it.
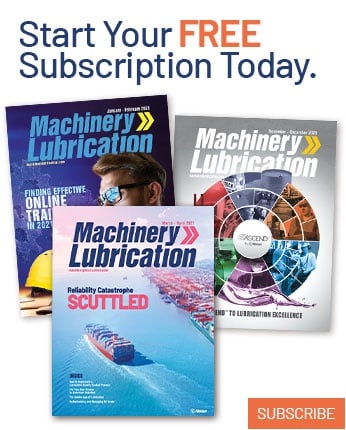