Many companies say they use standard work, but actually very few do, at least in the manner that leverages lean fully at the operational level. Instead, most firms use some form of work standards or work instructions.
Frequently, plants trying to implement standard work within their lean efforts will do a kaizen event and, in the process of the event, develop and post a number of forms (standard work sheet, work combination sheet, etc.) at the new cell. This action is a helpful exercise for the event but does not really help with the performance and sustainability of standard work or the continual performance of production.
The problem is that while the operators may be referenced to the new forms (this is what you need to do) or even involved in the development of the forms (the new standard work) during the event, this is not the purpose of the standard work forms or standard work for that matter. The forms are only for management, not the operators.
This is where training within industry (TWI) comes in. The operators are not going to be able to perform the new standard work (even if they were involved in the development of the forms) to the level that it needs to be — to maintain the necessary stability of the process. TWI’s job instruction tool is the source of training operators in order to properly and consistently perform to meet the standard. TWI’s job method is the source of continuous improvement needed to develop and implement improvements to the process day in and day out. Traditional methods of training will not cut it.
The development of good standard work is a fundamental key to lean success, but unfortunately most companies do not go nearly far enough with their effort — and, in most cases, are not even aware of this. If you want to be successful with standard work, there is no alternative other than TWI.
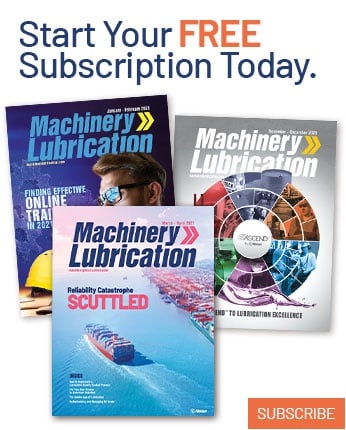