If your company was manufacturing automobiles, appliances, iPads or even cardboard boxes, you certainly wouldn’t think about scheduling production without a complete and accurate bill of materials (BOM) for each finished product so you could determine your raw material requirements from a master schedule.
So why is it that many process industries not only begin operation without equipment BOMs, but go for years – sometimes decades – without them?
When we ask people to assess the quality of their equipment BOMs, the comments we get most often are: “They don’t exist,” or “We have some of the data, but we don’t know if it’s accurate.”
When we ask why that’s the case, the response is usually: “We don’t have the information,” or more likely, “We don’t have the resources to do all that work.”
So instead of taking the time to build and maintain the BOMs, they just go on without them. That means planners, maintenance and reliability engineers, mechanics, materials management and procurement personnel, and others have to go outside the system to do things like:
- Determine material requirements for planned work
- Query and locate parts for emergency and other unplanned work
- Associate critical spares to specific assets
- Evaluate part substitutions
- Assess non-moving material for obsolescence
- Identify opportunities for part standardization
Somehow there’s time for most of these workarounds, and although it’s hard to calculate, it probably takes two to 10 times as much effort to deal with the lack of information as it would to just fix the problem in the first place.
Unfortunately, the focus is on the reactive aspects of what “really needs to be done” and not on the proactive aspects of getting the information into the system. If you don’t keep up, it’s hard to catch up. So what are the five critical success factors for establishing and maintaining effective BOMs?
1. The most important thing you can do is get the information into the system as early as possible. As soon as you have made a commitment to buy a new piece of equipment, you should be on the phone with the manufacturer or supplier to get the BOM information. Unless there’s a possibility that something could change, you should have the BOM data in the system even before the equipment is installed.
2. Don’t kill yourself trying to get every last little item into the database. If your system supports an automatic upload of BOM data from an electronic file, then take advantage of it. However, if you have to enter the data manually, make sure you get the most important stuff in there first. A good rule of thumb is that anything you reasonably expect to repair and/or replace should go on the BOM, with the exception of consumables and free issue parts.
3. Make sure you have a robust process in place to manage changes to the asset base. Whether you call it “management of change,” “configuration management” or “Mikey,” the important thing is that all equipment redesigns, material changes, part substitutions or even significant modifications are assessed to determine the impact on the BOM.
4. Don’t forget about retired assets. How many times have you had someone look at an expensive or supposedly critical part that hasn’t moved in the storeroom and heard them say, “Oh, we stopped using those years ago when we took out the …” (whatever). It’s so much easier and cost-effective to deal with these situations as they occur.
5. Make it part of the culture. This isn’t something that can be done randomly or easily driven from the bottom up. It requires management commitment to make it a priority, with clearly defined responsibilities and expectations for each person involved in establishing and maintaining the integrity of the BOMs and accountability for making sure it happens.
Of course, it’s not easy. The easy thing is to do nothing and continue to live with the consequences. Even if you can’t erase all the mistakes of the past, at least put something in place to keep the situation from getting worse. Once you can keep up, it’s easier to catch up.
About the Author
Doug Wallace has more than 30 years of combined experience in supply chain operations and management consulting, specializing in the areas of global enterprise planning, production and inventory control, and materials management. As a materials management subject matter expert for Life Cycle Engineering, his primary focus is on implementing best practices in procurement, warehouse operations, inventory optimization, and utilization of associated business and information systems. He can be reached at dwallace@LCE.com.
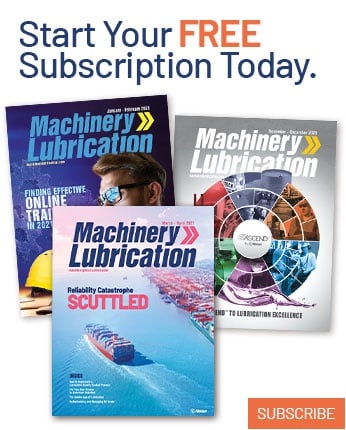