In my pre-retired life, I managed the development of maintenance procedures, PM programs, methods and service tools for all deployed equipment within the U.S. Postal Service. We also monitored our maintenance procedures manuals which incorporated support policies for the maintenance management information system. Any local changes were to be approved on a trial basis by my shop.
At that time, we were scratching our heads on how to get the supervisors out of their desks and out on the floor for more face time with the craft employees. I received a call from a plant maintenance manager requesting to stop recording the employees’ work order time on the daily work schedule forms. This was accomplished at the end of each shift by the supervisors from completed work orders. Each supervisor spent about an hour on this clerical task.
It seems the data entry to the MMIS is taken off the work order itself. The schedule sheet is only used for work assignments. He had devised a simple process to audit to assure accuracy. We gladly accepted his proposal.
About two months later, he called and told me that his supervisors were still tied to their desks. Somehow they had found more administrative work to do. His further investigation indicated that his supervisors did not know what to do with the added floor time. He asked for help with this oxymoron.
I will write several follow-on blog postings, prompted by this symptom, of a larger problem that we uncovered over the ensuing months, but I want to focus on the Murphy’s Law that covers what happened here: The work will expand to fill the time allotted. An overall truism is that when you remove some repetitive work from a person’s day, you had better have something to replace it or the employee will find something to fill the void. This is a big issue with any changes in work design.
It goes further when we consider that there is a ripple effect in any system when we make a change. We have to really understand how the system actually operates if we really want to manage for results. This is especially important when we are affecting a person’s work day. And over the years, seemingly small changes in many legacy systems have nurtured and matured work-around processes/methods, resulting in relying on individuals to perform that which the organization is responsible for: training and development. And I submit that the victim is usually the first-line supervisor.
The larger issue which we encountered was the abilities of our supervisors to supervise and even more telling was “what did we mean by supervise?” What does face time mean? How does a planned work order fit into the supervisor’s tool bag? How do we communicate change? What tools does the supervisor have? What are industrial best practices for supervisors?
Maybe we should start with the question: Why do we need supervisors? I am not an expert but will give actual examples of how some companies have addressed the question. They may include a plant with no management, face time as an interpersonal skill, learning organizations, “empowerment”, training and development, and hopefully some examples sent in by my faithful readers.
Remember: humility trumps pride.
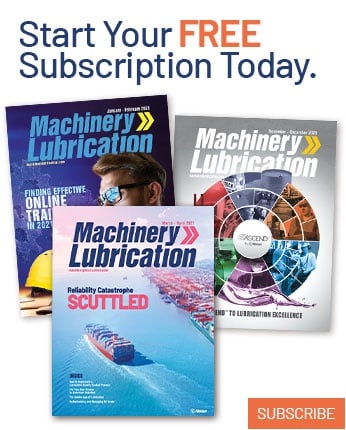