Safelite Glass Corporation, a leading producer of windshields for the automotive aftermarket, knew that to remain competitive with its Chinese counterparts, the company had to reduce costs. To do this, Safelite brought in experts from North Carolina State University’s Industrial Extension Service (IES) to meet its goals of reducing costs through improved efficiency and productivity within the company’s Enfield, N.C., plant. By implementing the principles of lean manufacturing, Safelite was able to retain sales to the tune of $2.6 million and save $670,000 in costs.
For this reason the company was recognized on August 25 for its contribution to the 1B4NC promise: to create $1 billion in economic benefit to the state of North Carolina from 2006 to 2010.
Bottlenecks
Downtime is not an option for the Halifax County facility, which produces approximately 700 different parts (20 simultaneously) and distributes them to 84 warehouses across the country. When any one of three furnaces shut down, bottlenecks occur, which can lead to a shutdown of the entire plant.
The goal of reducing bottlenecks prompted IES to facilitate a value stream map of the furnace department. A lean tool, value stream mapping (VSM) is a powerful technique for visualizing the flow of raw materials, information and finished products through all production steps for a particular product. For a VSM to be successful, it requires a group effort. In this case, it included members of the furnace department, Safelite leadership and IES facilitators.
The map indicated a need to reduce “no-loads”, as the company refers to them. No-loads, in the simplest of terms, are lost opportunities. Once a windshield is set, it is heated and then bent to specifications based on a vehicle make and model. This process follows an assembly line that passes through a high-temperature furnace. For every available slot that does not have a product, the company is wasting time, energy resources and, inevitably, money.
The group developed a future state map, aimed to improve flow, layout and reduce inventory.
Johnny McDonald, process engineer and 11-year veteran at Safelite, stated, “Lean changed the way we think around here. It used to be run, run, run. Now we run only what we need.”
Savings in work-in-process save investments in raw materials, space and labor, which all add to the bottom line.
Results, clear as glass
Another large component of Safelite’s lean work included the adoption of 5-S (sort, standardize, straighten, shine and sustain).
Quality manager Len Davis was amazed at the time that was saved by simply not having to dig for what you need. “Not having what you need when you need it is huge,” said Davis.
The lean work that was done in the furnace area decreased no-loads and increased production potential to an extra 57,000 units annually. Lean also decreased overtime in the area.
Once witnessing the power of lean in the furnace area, Safelite brought it in to the glass processing center with the goal of reducing changeover time, or the time it takes to switch a machine from making one product to another. On one particular line, there are seven changeovers per shift at an average of 15 minutes each. Lean helped reduce changeover time by one-third, allowing more parts to be produced in less time.
But lean isn’t just about producing more. The principles also lead to improved quality. By standardizing work instructions, the glass processing center saw the level of poor edge quality improve, which decreases breakage, again saving the company raw material dollars and labor.
Speak the language
IES is the extension department of the College of Engineering at North Carolina State University. IES provides technical expertise, training and education to help improve and sustain North Carolina industry. IES extension experts typically have more than 15 years of direct industry experience in their field.
Rich Glover, assistant vice president of manufacturing and distribution, said that working with IES lean specialist David Yates was more of a partnership than a typical client/vendor relationship.
“With all due respect, David’s not an academic; he understands production and the constraints of an organization,” said Glover.
Glover likes the concept that lean requires input from the people on the floor.
“Lean offered a baseline (for improvement), and it challenged our people to provide outcomes and solutions to their problems,” said Glover. “It also provided a common ground for engineers and plant employees to speak the same language while working toward a shared goal.”
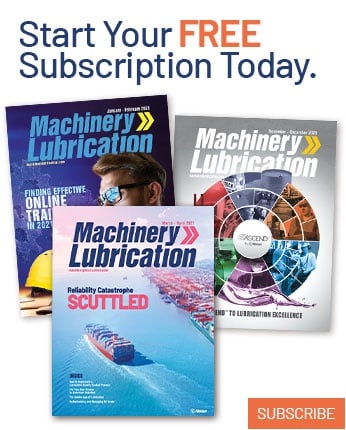