Methods of manufacturing have changed a great deal since the Ford assembly line, shifting from the rigid, push-oriented production principles of the early 20th century to more flexible, pull principles. If you find yourself wondering what a pull principle is, you’ve come to the right place.
Put simply, assembly line manufacturers historically pushed mass production ahead based on estimates of future demand, which often resulted in wasted effort and resources when customers failed to produce the estimated demand. Modern companies can’t afford this kind of waste, so they wait for actual demand to pull production forward, manufacturing products when they’ve been requested by customers or when the previous batch of products has sold out.
Consider this analogy: By trying to guess potential demand, manufacturers often found themselves in the same situation as someone carrying an umbrella on a sunny day because the forecast predicted rain; it was extra effort for no reason. Modern manufacturers prefer to stick their head out the window and check for rain before grabbing their umbrella, so to speak, limiting waste and maximizing efficiency.
Unfortunately, understanding the many complex strategies behind these new manufacturing methods can be as difficult as predicting the weather, as they have brought along with them a series of three-letter acronyms that dominate jargon-filled conversations about current manufacturing trends, like JIT, TPM, QRM and JIS. These letters don’t exactly help to explain the basic ideas behind pull-production manufacturing, which actually make a lot of sense when spoken in plain English. So, I’ve decided to break down the key concepts of lean manufacturing, Six Sigma and flexible manufacturing. While I couldn’t cover every concept – a Google search for “lean manufacturing glossary” should satisfy most pedants – I have reviewed the important terms. Leave a comment below if there are others you’d like us to explain. Let’s get started.
Basically, modern manufacturing methods boil down to three key concepts:
-
- Reduce waste – reduce the amount of materials, capacity and manpower wasted in the process by producing just enough product to meet current demand
- Maintain quality – devise more effective manufacturing methods in order to continue making quality products despite strict reductions of waste
- Accelerate production – decrease the amount of time needed to manufacture product, making up for the lack of surplus
Reduce Waste
If this first concept sounds like the motto of the recycling movement, it’s because manufacturing, like so many other industries these days, is basing its methods on efforts to avoid waste. Earlier manufacturing methods allowed for waste and an excessive consumption of supplies in order to meet their goals of mass production, but the rebranding of modern manufacturing goes by a new name: lean manufacturing.
Lean manufacturing describes the method used to achieve all three of the aforementioned concepts; in theory, a lean manufacturer would have the right supplies arrive at the right place at the right time in the right amount to create only the products that are necessary to meet demand. A number of concepts, defined in the table below, are influential in meeting this goal.
Maintain Quality
In order to manufacture a product of consistently high quality, it’s necessary for manufacturers to not only perform frequent maintenance on their equipment, but on their entire process as well. This means identifying errors or defects in the production flow and eliminating them to maximize productivity. This is where Six Sigma comes in.
The origin of the term itself is very complex. A manufacturing process is given a sigma rating based on the percentage of its product yield determined to be defect-free. A One Sigma rating designates a process with a disastrously low percentage of defect-free yield, 31 percent, while a Six Sigma rating is reserved for processes that are nearly perfect, 99.99966 percent defect-free. In other words, every company wants to achieve Six Sigmas for all of its manufacturing processes.
To meet this goal, the Six Sigma method was created, which focuses on measuring and analyzing process data in order to find and remove defects. Whereas lean manufacturing is concerned with improving the flow between processes to reduce waste, manufacturers use Six Sigma to improve the processes themselves. The table below includes some of the concepts that make Six Sigma work.
Accelerate Production
In the era of lean manufacturing, when surplus product is considered waste, the manufacturing process must work faster to make sure products are made available and demand is met. However, speeding up the process has become more difficult than ever due to an increased customer desire for customization.
In the 20th century, mass production and mass consumption went hand in hand. Assembly lines made it possible to make hundreds of thousands of the same product, and customers were entirely willing to own the exact same thing as their friends and neighbors. Now, with the advent of Internet shopping and its capacity to provide shoppers with a variety of choices, manufacturers must be prepared to adapt and change not only its products but its entire process as well.
Enter flexible manufacturing. Though manufacturers would undoubtedly prefer to continue producing standardized products at low costs, they must nevertheless make the best of their customers’ new tendencies toward individualized, unique products. These manufacturers can limit their cost increases by designing processes that adjust quickly and effectively to change. This table provides a few of the concepts that allow manufacturers to remain flexible while continuing to reduce waste and maintain quality.
With customer demands shifting constantly on a global scale, manufacturers must utilize a number of strategies to maximize their profits and continue to compete. As this guide suggests, the three major goals of reducing cost, maintaining quality and accelerating production are achieved through the combined efforts of lean manufacturing theories, Six Sigma methodologies and flexible processes. It’s not a question of which manufacturing method is the right one, it’s a question of how to implement them all for optimum results.
About the author:
Stephen Jannise is the ERP market manager for Software Advice. For more information, e-mail stephen@softwareadvice.com or visit http://www.softwareadvice.com/manufacturing/.
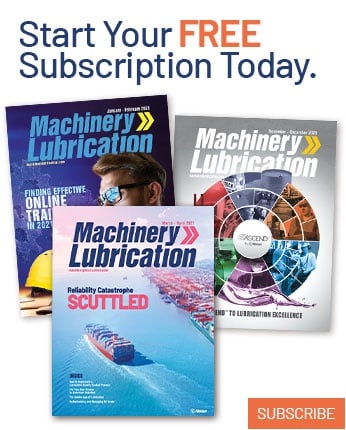