On August 6, British Petroleum ordered the shutdown of the Alaska Pipeline, which supplies approximately 8 percent of the crude oil supply to the United States. The shutdown couldn’t have come at a worse time, with oil trading at more than $75 per barrel. The shutdown is costly for oil producers, costly for the U.S. consumer and devastating for BP’s public image. Regrettably, the shutdown was avoidable; it was reportedly caused by the age-old mistake of deferred maintenance. Experts estimate the repair time at 16 weeks.
The reported cause for the failure is pipeline corrosion. Over time, as crude passes through the pipeline, sludge collects. The acids in this sludge corrode the pipeline material which, over time, reduces the wall thickness of pipeline. If left uncorrected, the wall thickness will reduce to the point that its integrity may be compromised. Inspectors concluded that more than two-thirds of the pipeline’s wall thickness was lost, which prompted the shutdown.
The process for removing the sludge, often called “pigging” the lines, is a routine, proactive maintenance task designed to reduce corrosion by clearing out the sludge. The pipeline in question was last scrubbed in 1992 – 14 years ago. The event is being investigated, but according to James Wiggins, a U.S. Pipeline and Hazardous Materials Safety Administration spokesman, “poor maintenance was obviously a factor.”
In addition to concerns about the company’s policy regarding pipeline scrubbing frequency, one must bring into question its policy regarding the employment of non-destructive testing techniques (e.g. ultrasonic, radiographic, etc.) to evaluate the pipeline integrity. This will undoubtedly be reviewed in the ensuing investigation.
What is the takeaway lesson from the mistakes BP allegedly made in managing maintenance of the pipeline? Equipment managers are tempted to defer maintenance on a daily basis. A dollar of reduced maintenance today equates to a dollar of increased profit this quarter. The problem is the long-term effect. Looking at this from a financial perspective, arbitrarily cutting maintenance is analogous to moving money from the asset column of the firm’s balance sheet to the profit line on the income statement. It looks good in the short term, but if you “spend” your assets, their true value diminishes over time, which ultimately increases your operating costs (see figure). In retrospect, which do you think is less expensive: monitoring and pigging crude oil pipelines periodically or shutting down all or part of the pipeline for weeks or months to replace parts corroded as a byproduct of neglect?
Maintenance costs can only be reliably reduced if the need for maintenance is engineered away by improving the machine’s design, changing the operating context or managing the operating environment. In other words, you must reduce the stressors that affect machine reliability or increase the strength of the machine so it can better resist the stressors that produce failure. You can also engineer away maintenance costs by improving design for maintainability, rationalizing PMs, utilizing inspections and monitoring techniques, etc.
For an arbitrary maintenance cutback to increase the long-term profitability of the firm, the manager making the decision must get lucky – and luck isn’t a very dependable partner.
Comments? E-mail Reliable Plant technical editor Drew Troyer at dtroyer@noria.com.
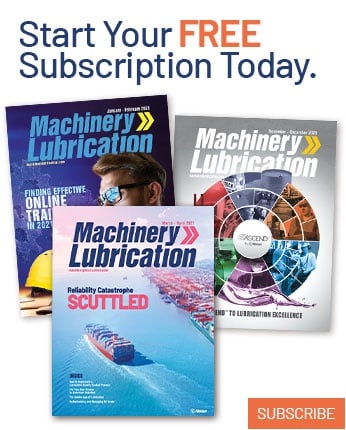